5901 Botham Jean Blvd, Dallas, TX 75215
Understanding Permanent Magnets: Key Concepts and Applications
March 5, 2025Permanent magnets are materials that create their own persistent magnetic field without requiring an external power source. Unlike their electromagnetic counterparts, these magnets maintain their magnetic properties indefinitely, making them indispensable in countless applications.
At their core, permanent magnets harness the intrinsic magnetic properties of certain materials, primarily iron, nickel, cobalt, and their alloys. These elements possess unpaired electrons that align to generate a stable magnetic field, a phenomenon known as ferromagnetism.
The strength and durability of permanent magnets have made them essential components in various industries. From the speakers in your smartphone to the heart of electric vehicles, these magnets play a crucial role in converting electrical energy into mechanical motion and vice versa.
One of the most significant applications of permanent magnets is in electric motors and generators. In these devices, magnets interact with electromagnetic fields to produce rotational motion or electrical current. This principle powers everything from your electric toothbrush to massive wind turbines generating renewable energy.
Advanced Materials in Permanent Magnets
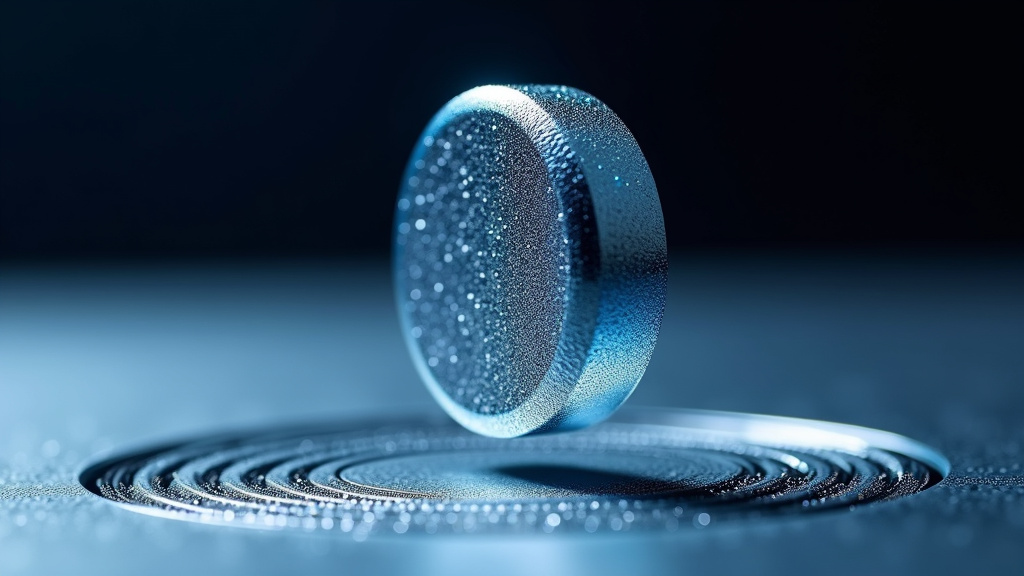
In magnetic technology, rare-earth elements have transformed the production of powerful permanent magnets. Neodymium, samarium, and cobalt are key components, enabling magnets with unmatched strength and durability. These elements form the foundation of high-performance magnets used in various advanced technology sectors.
Neodymium, a silvery-white metal, is the basis of neodymium-iron-boron (NdFeB) magnets, which have the highest magnetic strength available today. Their exceptional power-to-weight ratio makes them ideal for applications where size and weight constraints are critical, such as in electric vehicle motors and wind turbine generators.
Samarium cobalt magnets offer unique advantages in high-temperature environments, maintaining their magnetic properties at temperatures up to 350°C. This makes them invaluable in aerospace and military applications where reliability under extreme conditions is essential. Their resistance to corrosion further enhances their durability.
Material Properties and Technological Impact
The magnetic properties of rare-earth magnets stem from their unique atomic structure. These elements possess unpaired electrons in their 4f orbital, contributing to their strong magnetic moments. When combined with transition metals like iron or cobalt, they form compounds with exceptional magnetic anisotropy, resulting in magnets that are difficult to demagnetize.
This remarkable resistance to demagnetization, known as high coercivity, is crucial for the reliability of devices using these magnets. It ensures that the magnetic field remains stable even under challenging conditions, such as strong opposing magnetic fields or mechanical shocks, which is vital in precision instruments and high-performance electronics.
The impact of these advanced magnetic materials on technology is significant. They have enabled the miniaturization of electronic devices, improved the efficiency of electric motors, and enhanced the performance of MRI machines in healthcare. In the renewable energy sector, rare-earth magnets have been instrumental in increasing the efficiency of wind turbines.
Challenges and Future Developments
Despite their remarkable properties, the production and use of rare-earth magnets face challenges. The limited global distribution of rare-earth elements raises concerns about supply chain stability. Additionally, the environmental impact of rare-earth mining and processing has prompted research into more sustainable extraction and recycling methods.
Researchers are exploring ways to reduce reliance on heavy rare-earth elements like dysprosium, often added to neodymium magnets to improve high-temperature performance. Innovations in material science aim to develop magnets with similar performance using more abundant elements or novel compositions that require fewer rare-earth materials.
The future of permanent magnet technology looks promising, with ongoing research into new magnetic materials and improved manufacturing processes. Scientists are investigating materials like iron nitride and manganese-based compounds as potential alternatives or complements to current rare-earth magnets. These developments could lead to even more powerful, durable, and environmentally friendly magnetic materials.
As we continue to push the boundaries of technology, the role of advanced magnetic materials will grow in importance. From powering the electric vehicles of tomorrow to enabling new frontiers in quantum computing, rare-earth magnets and their successors will remain at the forefront of technological innovation, driving progress across multiple industries and applications.
Permanent Magnets in Electric Vehicle Technology
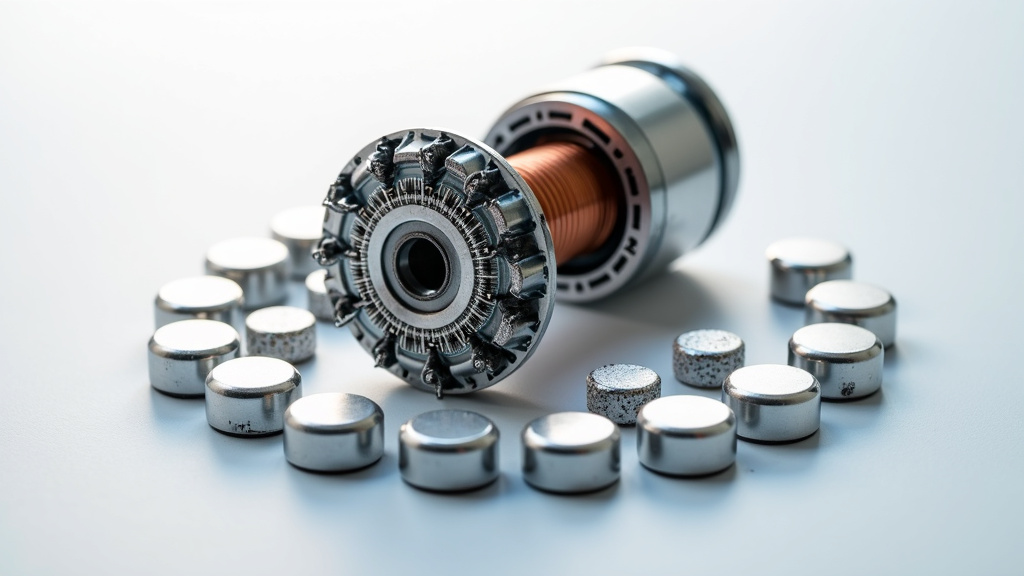
As the automotive industry embraces electrification, permanent magnets have become integral to electric vehicle (EV) motors. These magnets enable the most efficient and compact EV powertrains, enhancing performance in modern electric cars. However, their increasing significance presents supply chain challenges that need addressing.
Permanent magnets, particularly those made from rare earth elements like neodymium and dysprosium, offer significant advantages in EV motor design. Their strong magnetic fields enable high-torque motors in compact forms, crucial for EVs where space and weight savings improve range and performance.
The efficiency of permanent magnet motors is notable. They can convert over 90% of electrical energy into mechanical power, greatly surpassing the efficiency of internal combustion engines. This efficiency contributes directly to the extended range and lower energy consumption that attract consumers and environmentalists.
The Growing Demand for EV Magnets
As global EV adoption accelerates, demand for these specialized magnets is rising rapidly. A recent report indicates that by 2030, up to 45% of vehicle sales could be electric, significantly increasing magnet production needs. This growth presents opportunities and challenges for the automotive and technology sectors.
This demand has spurred innovation in magnet design and manufacturing. Engineers are developing magnets that are more powerful, temperature-resistant, and economically viable, potentially enhancing EV performance and reducing costs, making them more accessible to consumers.
However, the surge in demand highlights vulnerabilities in the global supply chain. Currently, rare earth element production is concentrated in a few regions, with China dominating the market, raising concerns about supply stability and geopolitical risks.
Supply Chain Challenges and Solutions
The limited sources of rare earth elements have led to the search for alternative solutions. Some companies are reducing the amount of rare earth materials in their motors, while others are exploring different motor designs that don’t rely on permanent magnets.
Recycling is emerging as a crucial strategy to address supply chain concerns. As the first generation of EVs reaches the end of its lifecycle, there is growing interest in recovering and reusing valuable magnetic materials from their motors. This circular approach could help alleviate pressure on raw material supplies and reduce the environmental impact of magnet production.
Governments and industries are investing in developing new sources of rare earth elements outside traditional mining regions. From deep-sea mining to urban mining of electronic waste, innovative approaches are being explored to diversify the supply chain and ensure a steady flow of these critical materials.
The Future of EV Motor Technology
Despite challenges, the future of permanent magnets in EV technology is promising. Ongoing research into new magnetic materials and motor designs aims to push efficiency and performance boundaries further. Some scientists are exploring exotic materials like high-temperature superconductors that could revolutionize electric motor technology.
As the EV market evolves, diverse solutions are expected to emerge. While permanent magnet motors are likely to remain dominant in the near term, alternative technologies like induction motors and switched reluctance motors may gain ground in certain applications. This technological diversity will help create a more resilient and adaptable EV ecosystem.
The story of permanent magnets in electric vehicles is one of innovation, challenge, and opportunity. As the industry overcomes supply chain hurdles and pushes motor efficiency limits, we stand on the cusp of a new era in automotive technology. The solutions developed today will shape the future of transportation and contribute to sustainable and clean energy systems worldwide.
Region | Production (Metric Tons) | Percentage of Global Production |
---|---|---|
China | 210,000 | 70% |
United States | 43,000 | 14% |
Australia | 18,000 | 6% |
Burma (Myanmar) | 12,000 | 4% |
Thailand | 7,100 | 2% |
Other countries | 10,900 | 4% |
Total | 301,000 | 100% |
The Environmental Impact of Permanent Magnet Production
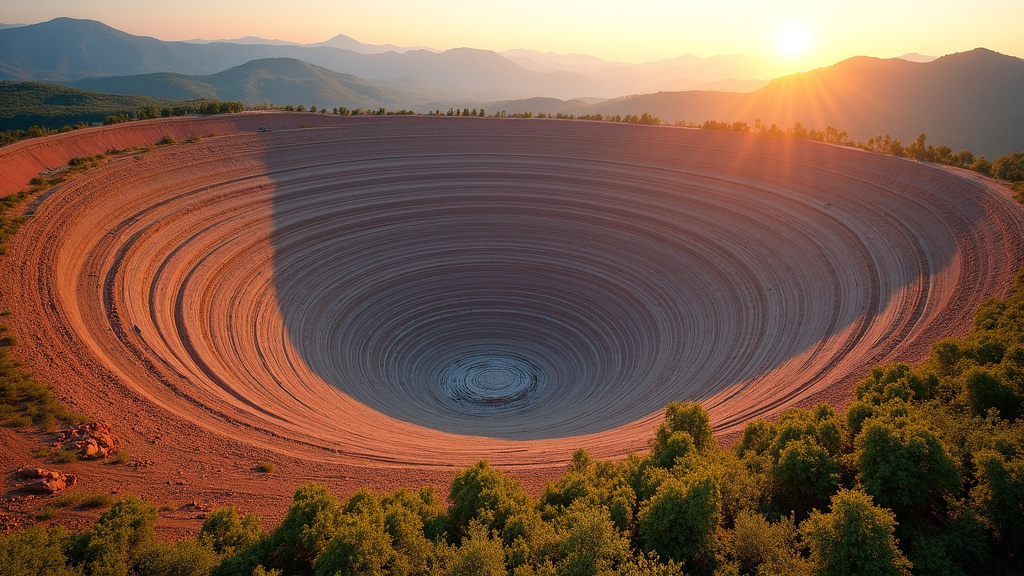
The production of permanent magnets, essential for many modern technologies, presents significant environmental challenges. These powerful magnets, especially those made from rare earth elements like neodymium and samarium, require energy-intensive manufacturing processes that can leave a considerable ecological footprint.
A primary concern is the mining and extraction of rare earth elements, often involving open-pit mining, which can lead to deforestation, soil erosion, and habitat destruction. For instance, satellite imagery of the Bayan Obo mining district in Inner Mongolia, China—the world’s largest rare earth element mine—reveals vast areas stripped of vegetation and scarred by mining activities.
The refining and processing of rare earth elements pose additional environmental risks, typically involving toxic chemicals and generating significant waste. According to a report by the United States Department of Energy, rare earth element production can release harmful substances into local water sources and contribute to air pollution, affecting both ecosystem health and human well-being in surrounding communities.
Innovations in Sustainable Production
Despite these challenges, the industry is progressing towards more sustainable practices. Researchers and companies are exploring ways to reduce the environmental impact of permanent magnet production. One promising approach is developing alternative materials that could potentially replace or reduce the need for rare earth elements in magnets.
For example, scientists at the University of Leeds are advancing hybrid magnets that combine cobalt with carbon. This innovation could boost magnet strength while reducing reliance on rare earth elements. As noted in their research, these hybrid magnets show potential for use in applications such as electric vehicles and wind turbines, offering a more sustainable alternative to traditional rare earth magnets.
The Role of Recycling
Recycling is becoming a crucial strategy for mitigating the environmental impact of permanent magnet production. Unlike many other materials, permanent magnets can be recycled indefinitely without losing their magnetic properties. This characteristic opens up significant opportunities for creating a more circular economy in the magnet industry.
However, current recycling rates for rare earth elements used in magnets remain low, estimated at only about 3% globally. Challenges include extracting these elements from complex end-of-life products and the lack of standardized recycling methods. Despite these hurdles, initiatives are underway to improve recycling processes and increase recovery rates.
Sustainable Practices in Manufacturing
Beyond recycling, manufacturers are implementing more sustainable practices in their production processes, including optimizing energy use, reducing waste generation, and improving water management. Some companies are also exploring renewable energy sources to power their manufacturing facilities, further reducing the carbon footprint of magnet production.
Additionally, there’s a growing focus on developing magnets that require fewer critical rare earth elements. For instance, some manufacturers are working on techniques to reduce the amount of dysprosium used in neodymium magnets while maintaining their high-temperature performance. These efforts conserve resources and contribute to more sustainable supply chains.
As demand for permanent magnets grows, driven by technologies like wind turbines and electric vehicles, the importance of sustainable production practices becomes ever more critical. While challenges remain, ongoing innovations in materials science, recycling technologies, and manufacturing processes offer hope for a more environmentally friendly future in permanent magnet production.
Mine Location | Environmental Impact | Key Issues |
---|---|---|
Bayan Obo, China | High pollution levels | Heavy metals, fluorine, arsenic contamination, soil and water pollution |
Kachin State, Myanmar | Severe ecological damage | Illegal mining, human rights violations, ecosystem destruction |
Ampasindava Peninsula, Madagascar | Biodiversity threat | Impact on last remaining forests, endangered species |
Norra Kärr, Sweden | Potential impacts | Concerns over water quality and local ecosystems |
Conclusion: The Future of Permanent Magnets in Industry
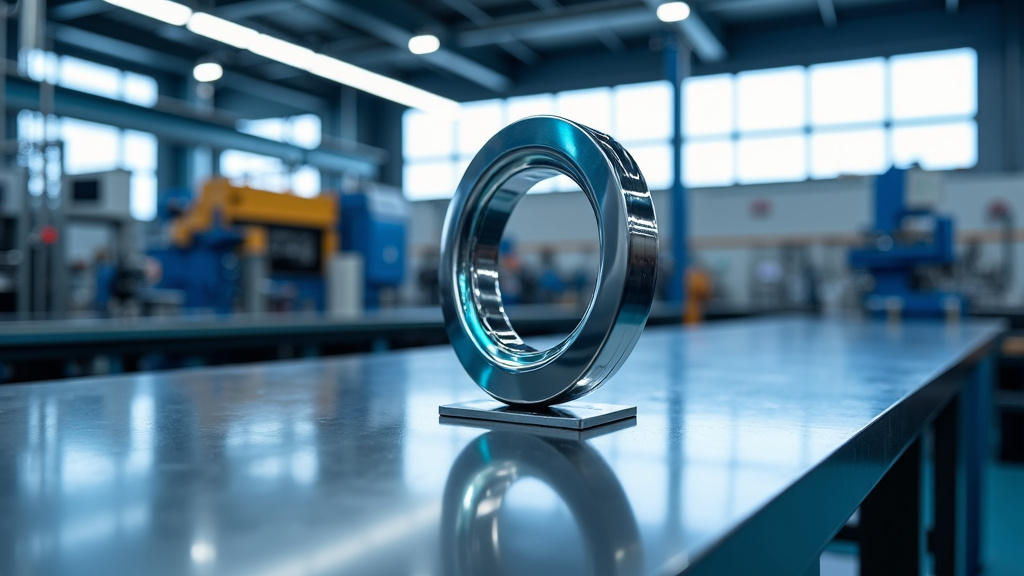
The future of permanent magnets in industry is promising, as these components become increasingly essential for technological advancement and sustainability.
Innovation in permanent magnet technology is advancing swiftly. Researchers and engineers are exploring new materials and designs that could transform industries like electric vehicles and renewable energy systems. The aim is to enhance magnetic properties while reducing reliance on rare earth elements.
One significant development is the breakthrough in sustainable permanent magnets, which aims to deliver high-performance magnets with a reduced environmental impact.
Optimizing production processes is also crucial. Industry leaders are investing in advanced manufacturing techniques to improve magnet quality and reduce waste and energy consumption, fostering a sustainable supply chain.
Recycling permanent magnets is becoming a key aspect of the circular economy. Companies are developing methods to recover and reuse magnetic materials from end-of-life products, ensuring these resources are not wasted.
The future of permanent magnets will balance performance with sustainability, aligning with global sustainability goals. The industry is set for transformation to meet growing demand responsibly.
Companies like Okon Recycling are pivotal in this evolution. Their expertise in metal recycling and commitment to sustainable practices position them as leaders in shaping a responsible future for the permanent magnet industry. By collaborating with such organizations, businesses can keep pace with innovation and contribute to a sustainable world.
Contact Okon Recycling at 214-717-4083 to learn more about shaping the future of permanent magnets and sustainable manufacturing.