5901 Botham Jean Blvd, Dallas, TX 75215
What are Non-Metallic Contaminants in Metal Recycling
March 27, 2025In metal recycling, these are unwanted materials that compromise the purity and quality of recycled metals. From plastics and rubber to paint and chemicals, non-metallic contaminants present significant challenges, affecting both operational efficiency and product quality.
These impurities can cause numerous issues. When metal is melted down for recycling, non-metallic materials can release toxic fumes or create slag, a byproduct that requires separate disposal. This complicates the recycling process and increases energy consumption and costs.
Understanding these contaminants is crucial for effective metal recycling and sustainable waste management. As the demand for recycled metals grows, so does the need for advanced methods to identify and remove these unwanted materials.
Imagine trying to bake a perfect loaf of bread, only to find your flour mixed with sand. That’s essentially what happens when non-metallic contaminants infiltrate the metal recycling stream. They’re the uninvited guests at the recycling party, causing havoc and reducing the quality of the final product.
But why should we care? Proper sorting and disposal of non-metallic contaminants are vital to maintaining the efficiency and sustainability of metal recycling. It’s not just about producing high-quality recycled metals; it’s about conserving natural resources, reducing environmental impact, and creating a more sustainable future for all of us.
Common Types of Non-Metallic Contaminants
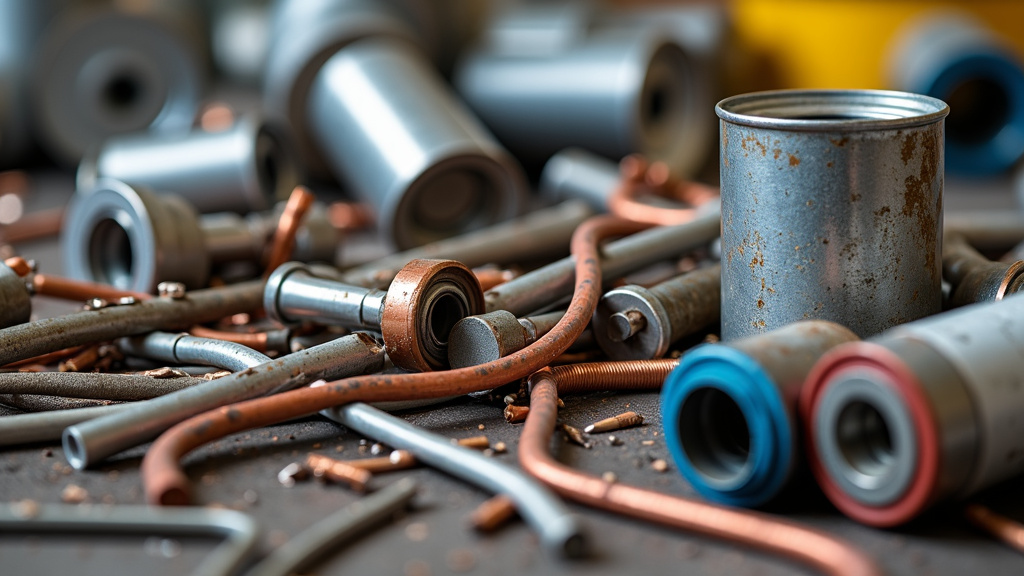
In metal recycling, non-metallic contaminants present a significant challenge. These substances can compromise the quality and value of recycled metals, making their identification and removal essential for efficient recycling. Let’s explore common non-metallic contaminants recyclers encounter:
- Plastics: Found in insulation on wires and electronic components, plastics are prevalent in many scrap metal items.
- Rubber: Often present in automotive parts, appliances, and machinery, rubber contamination can be particularly tricky to remove.
- Wood: Wooden components or packaging materials frequently accompany metal scraps, especially from construction or furniture disposal.
- Paint: This common surface contaminant can affect the purity of recycled metals and may contain harmful substances.
- Oils and Lubricants: Machinery and automotive scrap often come coated with various oils that require thorough cleaning.
These contaminants usually come from coatings, attachments, or residues on scrap metal items. For instance, an old refrigerator might contain plastic shelving, rubber seals, and layers of paint—all needing removal before the metal can be effectively recycled.
Identifying and categorizing these non-metallic materials is crucial for developing effective removal strategies. Each type of contaminant may require a different approach, from manual separation to chemical treatments.
The challenge of dealing with these contaminants has spurred innovation in the recycling industry. Advanced sorting technologies, like sensor-based systems, are now employed to detect and separate non-metallic materials more efficiently. This not only improves the quality of recycled metals but also increases the overall efficiency of the recycling process.
For those in the scrap metal business, understanding these common contaminants is key to maximizing the value of their materials. Proper preparation of scrap, including the removal of non-metallic components, can significantly increase its worth at the recycling center. It’s beneficial for both the environment and the bottom line.
Impact of Non-Metallic Contaminants on Recycling Process
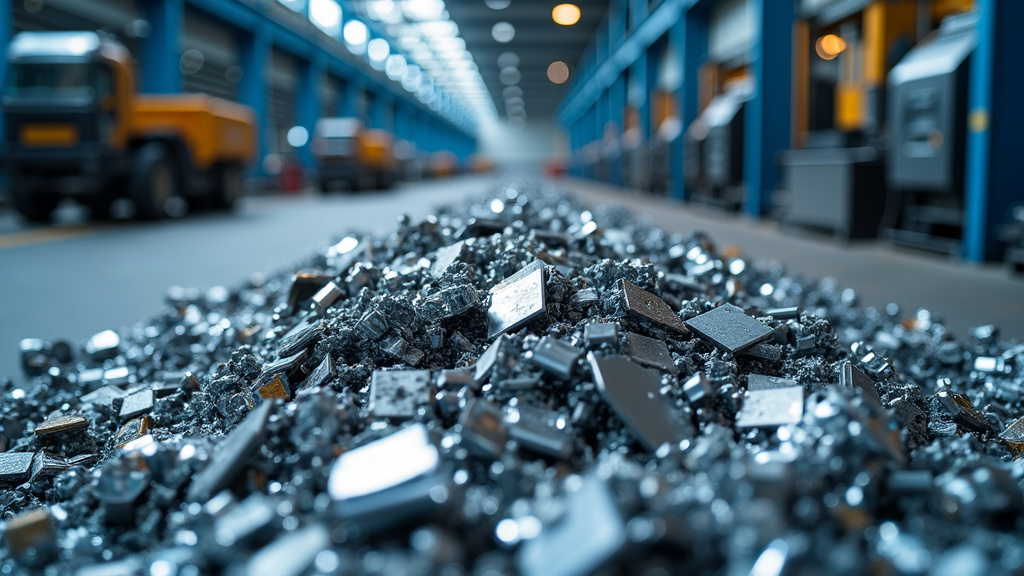
The metal recycling industry faces a significant challenge: non-metallic contaminants. These unwanted materials can disrupt the recycling process, lowering the quality of recycled metals and increasing costs. Let us explore the consequences of these impurities.
Non-metallic contaminants notably reduce the purity of recycled metals. When materials like plastics, rubber, or coatings enter the recycling stream, they result in an inferior final product. These contaminants can release toxic fumes or create slag during melting, a byproduct that requires separate disposal.
These contaminants also increase energy consumption during processing. Melting a batch of metal filled with impurities is akin to baking a cake with eggshells mixed in. The additional effort to separate and process these contaminants means more energy usage, higher costs, and a larger carbon footprint.
Equipment Damage: A Costly Consequence
The most alarming impact of non-metallic contaminants is potential equipment damage. Recycling facilities invest heavily in specialized machinery for sorting, crushing, and processing metal scrap. When non-metallic materials slip through, they can damage this expensive equipment.
Imagine a plastic-coated wire entering a metal shredder. The plastic melts, causing malfunctions and potentially leading to costly downtime for repairs. Similarly, a chunk of concrete mixed with metal scrap could chip or dull cutting blades, reducing efficiency and increasing maintenance costs.
These issues are not hypothetical. Recycling facilities globally face these challenges daily. One plant in the Midwest reported a 20% increase in equipment maintenance costs due to contamination-related damage over a year, significantly impacting the bottom line.
The Ripple Effect on Recycling Economics
The impact of non-metallic contaminants extends beyond the recycling plant. When recycled metal quality declines, so does its market value. Manufacturers relying on recycled materials may have to seek higher-grade, more expensive alternatives, potentially slowing the adoption of recycled metals.
Moreover, increased costs from contamination—energy usage to equipment repairs—can make metal recycling less economically viable, potentially reducing overall recycling rates and undermining efforts to create a circular economy for metals.
Strategies for Mitigating Contamination
Fortunately, the recycling industry is addressing this challenge. Innovative solutions are emerging to tackle contamination. Advanced sorting technologies, like optical and X-ray fluorescence scanners, can identify and remove non-metallic materials with impressive accuracy.
Education is also crucial. By teaching consumers and businesses about proper metal recycling practices, we can reduce contamination at the source. Some communities have even implemented “clean scrap” programs, offering incentives for contaminant-free metal recycling.
The battle against non-metallic contaminants in metal recycling is ongoing, but the stakes are high. By understanding and addressing this challenge, we can ensure a more efficient, cost-effective, and sustainable recycling process for future generations.
Methods for Identifying and Removing Non-Metallic Contaminants
In scrap metal recycling, removing non-metallic contaminants is crucial for producing high-quality recycled materials. Let’s explore some effective techniques used in the industry today.
Visual Inspection
The first line of defense against contaminants is often the human eye. Trained workers can quickly spot and remove obvious non-metallic materials like plastic, rubber, or wood. While labor-intensive, this method is particularly effective for large or easily identifiable contaminants.
Visual inspection serves as an essential preliminary step, catching obvious impurities before more advanced sorting begins. However, it’s limited by human error and fatigue, making it less suitable for detecting smaller or well-hidden contaminants.
For instance, at facilities processing mixed household scrap, visual sorting might catch items like plastic utensils mixed in with metal cookware. This initial screening improves the efficiency of subsequent automated processes.
Magnetic Separation
Magnetic separation is a powerhouse in the metal recycling industry, effortlessly separating ferrous from non-ferrous materials. Strong magnets attract iron-containing metals, leaving behind non-magnetic contaminants and other metal types.
This method shines in its simplicity and effectiveness. It’s widely used in recycling facilities to quickly sort large volumes of mixed scrap. Magnetic separation is particularly valuable when dealing with shredded materials where visual inspection becomes challenging.
For example, advanced magnetic separation systems can process tons of shredded automotive scrap per hour, efficiently removing ferrous metals from a mix of plastics, rubber, and other non-ferrous materials.
Air Classification
Air classification leverages differences in material density to separate lighter contaminants from heavier metals. This process uses controlled air streams to lift and carry away lighter non-metallic materials while heavier metal pieces fall.
The beauty of air classification lies in its ability to handle a wide range of particle sizes and its effectiveness in removing low-density contaminants like dust, paper, and light plastics. It’s particularly useful in processing electronic waste or automotive shredder residue.
Many recycling plants employ air classification as a crucial step after shredding and before more precise sorting methods. It significantly reduces the volume of material that needs further processing, improving overall efficiency.
Advanced Sorting Technologies
The cutting edge of contaminant removal lies in advanced sorting technologies. These systems often combine multiple sensors and artificial intelligence to achieve unparalleled accuracy in identifying and separating materials.
One such technology is X-ray fluorescence (XRF), which can detect the elemental composition of materials. This allows for precise identification of different metal alloys and non-metallic contaminants. Another innovative approach is the use of optical sorters that employ cameras and lasers to identify materials based on color, shape, and size.
Modern recycling facilities often use a combination of these technologies. For instance, a system might first use magnetic separation, followed by air classification, and finally, an XRF sorter to achieve the highest purity levels in recycled metal streams.
Sorting Technology | Purity Level (%) | Efficiency |
---|---|---|
Optical Sorting | 95-98% | High |
Automated Separation | Up to 95% | Significantly reduces contamination rates |
Purity Mode (Cell Sorting) | High purity critical for application | Excludes non-target events |
Yield/Recovery Mode (Cell Sorting) | Lower purity | 100% efficiency in recovering cells |
Combining Methods for Optimal Results
While each method has its strengths, the most effective contaminant removal strategies typically involve a combination of techniques. This multi-step approach ensures that a wide range of contaminants can be identified and removed, regardless of their properties.
For example, a typical process flow might start with visual inspection to remove large contaminants, followed by magnetic separation to extract ferrous metals. The remaining material could then undergo air classification to remove light contaminants before finally passing through an advanced optical or XRF sorter for final purification.
By leveraging the strengths of each method, recyclers can achieve remarkably high purity levels in their output, meeting the stringent quality requirements of modern manufacturing processes and contributing to a more sustainable, circular economy for metals.
The Future of Non-Metallic Contaminant Management in Recycling
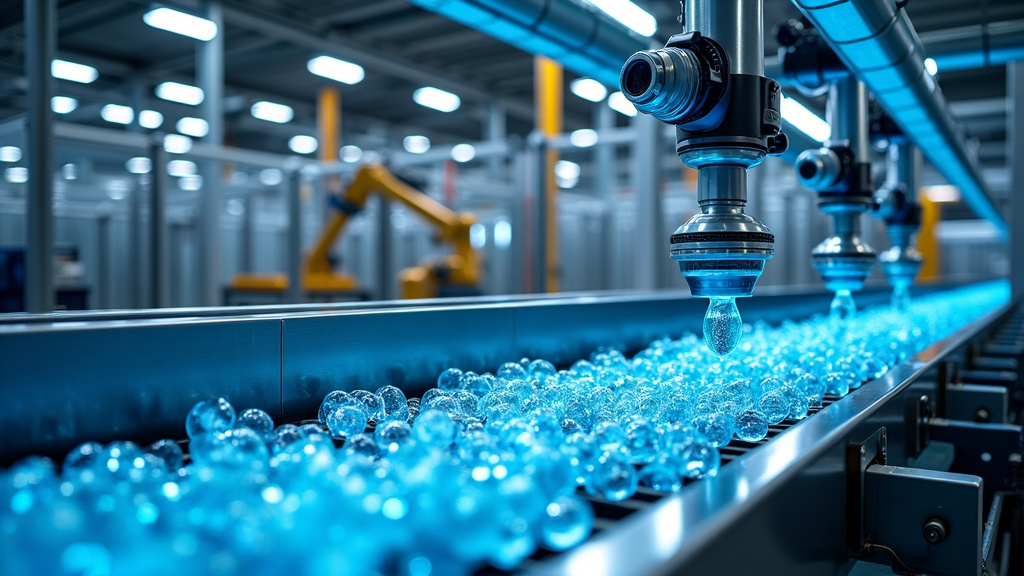
The recycling industry is on the verge of a technological transformation, with emerging solutions ready to address one of its most persistent challenges: non-metallic contaminant management. AI-powered sorting systems and advanced chemical treatments are now tangible tools reshaping recycling efficiency.
Artificial intelligence is proving transformative. AI-based solutions help detect non-recyclable materials early, guiding better disposal practices and significantly reducing contamination in the recycling stream. This technology’s ability to learn and adapt means it is constantly improving how we sort and process recyclables.
For businesses and individuals, staying informed about these developments is essential. The long-term benefits of proper contaminant management go beyond immediate cost savings, contributing to a more sustainable economy. As these technologies mature, early adopters will gain significant advantages.
To learn more about leveraging these advancements in non-metallic contaminant management, contact Okon Recycling at 214-717-4083.