5901 Botham Jean Blvd, Dallas, TX 75215
How to Recycle Steel Scrap: A Quick Guide
February 5, 2025Imagine a world where the towering skyscrapers and sturdy bridges we rely on daily aren’t just marvels of engineering, but also champions of environmental stewardship. This isn’t a far-off dream. It’s the reality that steel scrap recycling is helping to create right now.
What’s more, Okon Recycling is at the forefront of this transformation, ensuring that valuable materials are efficiently repurposed for a greener future. But what exactly makes this process so critical for our planet and economy?
Steel scrap recycling is a powerful tool in the fight against climate change and resource depletion. Every ton of recycled steel saves a staggering 1.4 tons of iron ore, 0.8 tons of coal, and 0.3 tons of limestone from being extracted from the Earth.
That’s not just good news for our landscapes – it’s a massive win for our atmosphere too. But the environmental benefits don’t stop there.
According to the U.S. Environmental Protection Agency, recycling steel conserves between 60% and 74% of the energy used in producing steel from virgin materials. This dramatic reduction in energy use translates directly to lower greenhouse gas emissions, helping us take a significant step towards a more sustainable future.
So, how does a discarded steel beam or an old car transform into the building blocks of tomorrow? The journey from scrap to new product is a fascinating one, filled with cutting-edge technology and precise processes.
Shredding and Separation of Steel Scrap
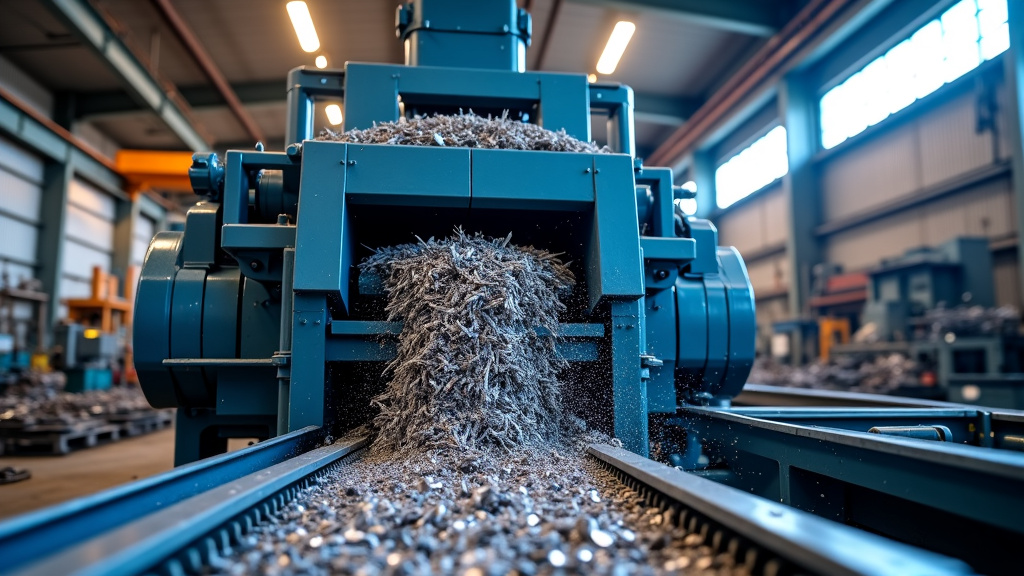
The recycling of steel scrap has seen remarkable technological advancements in recent years, particularly in the crucial stages of shredding and separation. These innovations are revolutionizing the industry, making the process more efficient, cost-effective, and environmentally friendly.
After the initial sorting, steel scrap undergoes a size reduction process known as shredding. This step is critical as it makes the material easier to handle, transport, and melt in furnaces. Two primary types of shredders dominate the industry: hydraulic power systems and electric power shredders.
Hydraulic shredders, favored for heavy-duty applications, excel at managing batch-feeding overloads. Their robust design allows them to process large volumes of scrap efficiently, making them ideal for high-volume recycling operations.
Advancements in Shredding Technology
Electric power shredders, on the other hand, are gaining popularity for their compact design and optimal performance in spaces where room is at a premium. These systems offer precise control over the shredding process, resulting in more consistent output sizes.
One of the most exciting developments in shredding technology is the introduction of the Shredder Drive Assistant. This innovative system optimizes energy consumption by adjusting the shredder’s operation based on the input material, significantly reducing overall energy usage and operational costs.
Another breakthrough is the Variable Frequency Drive, which allows for real-time adjustments to the shredder’s rotor speed. This technology enhances efficiency by adapting to different types and densities of scrap metal, ensuring optimal performance across various materials.
Advanced Separation Techniques
Post-shredding, the focus shifts to separating the steel from impurities. Magnetic separation remains a cornerstone of this process, but recent advancements have greatly improved its effectiveness. High-performance magnetic separation components are now capable of achieving material yields and purity levels that were previously unattainable.
The introduction of eddy current separation has enhanced the removal of non-ferrous metals from the shredded material. This technique uses powerful magnets to create repulsive forces against non-ferrous metals, effectively separating them from the steel scrap.
Sensor-based sorting technologies have also made significant strides. X-ray fluorescence (XRF) and laser-induced breakdown spectroscopy (LIBS) can now rapidly analyze the chemical composition of scrap, ensuring higher purity levels in the recycled steel.
Efficiency and Environmental Impact
These technological advancements are not just improving efficiency; they’re also contributing to a more sustainable recycling process. By optimizing energy use and increasing the purity of recycled steel, these innovations are reducing the industry’s carbon footprint and conserving valuable resources.
The steel recycling industry continues to evolve, with ongoing research and development promising even more exciting innovations in the future. As we move towards a more circular economy, these advancements in shredding and separation technology will play a crucial role in meeting the growing demand for high-quality recycled steel.
Shredder Type | Security Level | Efficiency | Cost |
---|---|---|---|
Strip-Cut | Low | High | Low |
Cross-Cut | Medium | Medium | Medium |
Micro-Cut | High | Low | High |
Melting and Refining of Steel Scrap
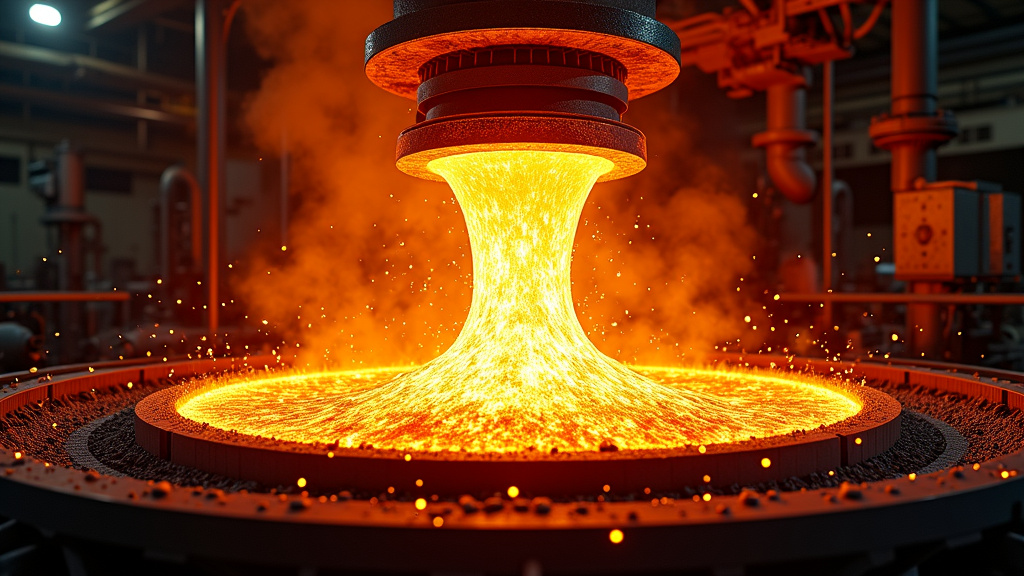
The process of turning scrap metal into high-quality steel is both a feat of engineering and a fascinating dance of chemistry. At the heart of this transformation lies the electric arc furnace (EAF), a modern-day alchemist’s cauldron where temperatures soar to a staggering 3,500°C – hot enough to turn solid steel into a bubbling, molten brew.
Imagine the EAF as a giant pressure cooker, where intense heat and carefully controlled chemical reactions work together to purify the steel. As the scrap melts, impurities rise to the surface like foam on a boiling pot. This is where slag formers come into play. These additives, typically including lime and fluorspar, create a protective blanket on top of the molten steel, trapping unwanted elements and preventing them from re-entering the metal below.
Oxygen plays a crucial role in this refining process, acting like a microscopic scrubbing brush. When injected into the furnace, oxygen eagerly combines with impurities like carbon, silicon, and manganese, helping to remove them from the steel. It’s akin to using soap to lift dirt from your hands – the oxygen ‘lifts’ the impurities out of the steel matrix.
The Art of Proportions
Creating high-quality steel is all about balance. Steelmakers must carefully control the proportions of additives and oxygen to achieve the desired result. Too much oxygen can lead to an overly ‘clean’ steel that lacks necessary alloying elements. Too little, and impurities may remain. It’s a delicate balancing act, not unlike perfecting a gourmet recipe.
During the refining stage, special attention is paid to removing stubborn impurities like sulfur and phosphorus. These elements can make steel brittle or prone to cracking if left unchecked. To combat this, steelmakers employ techniques such as inert gas sparging, where bubbles of argon or nitrogen are pumped through the molten steel, effectively ‘stirring’ the bath and helping impurities float to the surface.
The Chemical Arsenal
Steelmakers have an array of chemical weapons at their disposal to tackle specific impurities:
- Calcium carbide acts like a magnet for sulfur, forming compounds that can be easily removed.
- Ferrosilicon serves as a powerful deoxidizer, helping to fine-tune the steel’s oxygen content.
- Aluminum can be added to ‘kill’ the steel, removing excess oxygen and nitrogen.
Each additive plays a specific role in the refining process, working in concert to produce steel with precise properties and composition. It’s a complex symphony of chemical reactions, all conducted within the fiery confines of the electric arc furnace.
From Scrap to High-Performance Steel
The journey from a heap of scrap metal to gleaming, high-quality steel is a testament to human ingenuity and our understanding of materials science. Through careful control of temperature, chemistry, and timing, steelmakers can transform recycled metal into products that meet the exacting standards of modern engineering and construction.
As our need for sustainable materials grows, the electric arc furnace process stands as a shining example of how we can recycle and refine metals to create products that are not just as good as those made from virgin materials, but often superior in quality and performance.
Additive | Role |
---|---|
Calcium Oxide | Slag conditioner |
Aluminum | Deoxidizer |
Ferrosilicon | Deoxidizer |
Calcium Carbide | Sulfur removal |
Magnesium | Alloying element |
Casting and Rolling the Recycled Steel
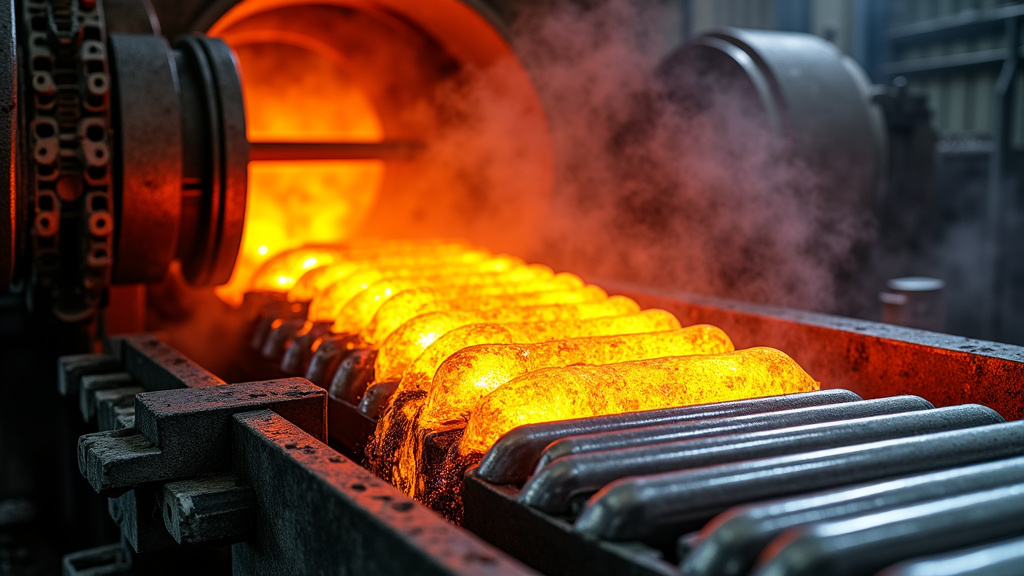
As recycled steel emerges from the refining process, it enters a critical phase: casting and rolling. This stage transforms the molten metal into usable forms, setting the foundation for countless industrial applications.
The Art of Continuous Casting
Gone are the days of inefficient batch casting. Today’s steel industry relies heavily on continuous casting, a method that’s revolutionized production efficiency. But what exactly does this entail?
Imagine a non-stop stream of molten steel being carefully guided into a mold, emerging as a solid, semi-finished product. That’s the essence of continuous casting. It’s like a steel waterfall, frozen in time and shaped for purpose.
This process offers significant advantages over traditional methods. For one, it dramatically increases throughput, allowing for round-the-clock production. Moreover, it yields higher quality steel with fewer defects, as the consistent cooling process reduces issues like segregation and porosity.
From Billets to Finished Products: The Rolling Process
Once the steel solidifies into billets—those rectangular or square semi-finished products—it’s time for the rolling mills to work their magic. This is where the real transformation happens, shaping our steel into the myriad forms we use daily.
Rolling mills are the muscle of steel production, applying immense pressure to reshape the metal. They’re like giant pasta makers, squeezing and stretching steel into sheets, bars, and coils. Each pass through the rollers brings the steel closer to its final form.
Criteria | Continuous Casting | Traditional Casting |
---|---|---|
Process Type | Continuous | Batch |
Cross-Sectional Products | Smaller, uniform | Larger, varied |
Efficiency | Higher, reduced labor costs | Lower, higher labor intensity |
Product Quality | Improved, fewer defects | More defects possible |
Material Versatility | Limited to standard shapes | Can accommodate complex shapes |
Suitability | High-volume production | Small production runs |
But it’s not just about brute force. Modern rolling processes are a delicate dance of precision and power. Computer-controlled systems ensure exact dimensions and optimal material properties, tailoring the steel to specific industrial needs.
The End Products: Versatility in Steel
The beauty of steel lies in its versatility, and nowhere is this more evident than in the variety of end products emerging from the rolling process. From the sheets that form car bodies to the reinforcing bars strengthening our buildings, each product serves a unique purpose.
Some common end products include:
- Steel sheets and coils for automotive and appliance industries
- Structural beams for construction
- Rails for transportation infrastructure
- Bars and rods for various manufacturing processes
Each of these products starts its journey as a humble billet, transformed through the marvels of modern metallurgy. It’s a testament to human ingenuity, turning recycled metal into the backbone of our industrial world.
As we reflect on this process, from molten metal to finished product, it’s clear that steel recycling is more than just environmental stewardship. It’s a crucial link in the chain of modern industry, turning yesterday’s scrap into tomorrow’s infrastructure.
Conclusion on Recycling Steel Scrap
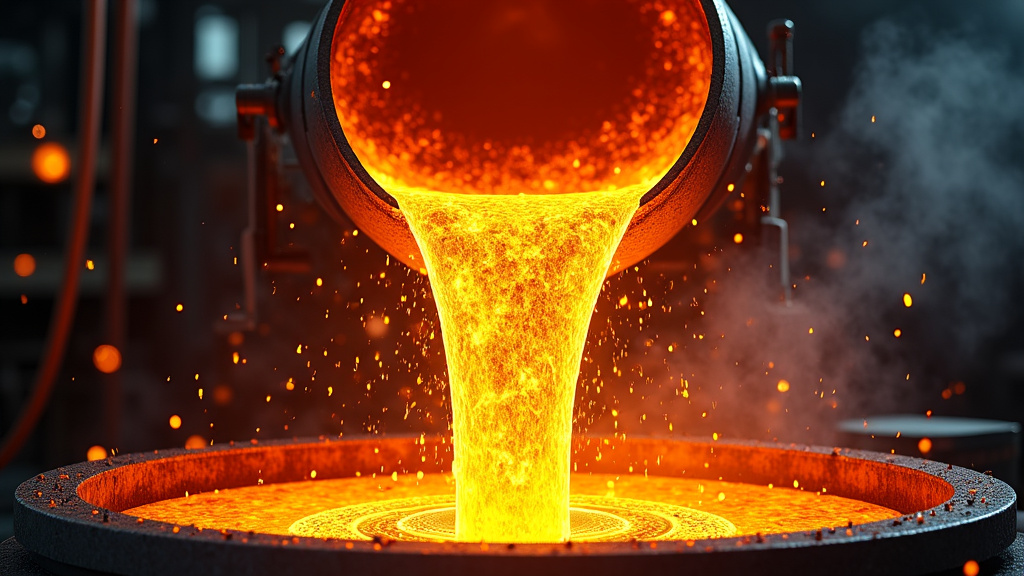
As we’ve explored the intricate journey of steel scrap recycling, it’s clear that this process is far more than just an environmental nicety. It’s a cornerstone of sustainable industrial development.
From the initial collection of discarded steel to the final rolling of new, robust products, each step in this recycling odyssey plays a crucial role in forging a more sustainable future.
The quality of recycled steel is nothing short of remarkable. Thanks to advanced purification techniques and rigorous quality control, the steel emerging from this process often rivals or even surpasses its virgin counterparts in strength and durability. This high-caliber output is a testament to technological prowess. More importantly, it’s a powerful argument for the viability of a circular economy in heavy industry.
Partnerships between industries and recycling experts like Okon Recycling are proving to be catalysts for change. These collaborations are not merely transactional; they’re transformational, pushing the boundaries of what’s possible in sustainable steel production.
By leveraging Okon’s century-long expertise and state-of-the-art facilities, businesses are finding that environmental responsibility and economic success can go hand in hand.
Ready to make a difference? Reach out to Okon Recycling at 214-426-6566 to learn about their innovative recycling solutions and join the movement towards a cleaner, greener world.