5901 Botham Jean Blvd, Dallas, TX 75215
Specialty Metal Recycling Best Practices Guide
March 12, 2025Recycling just one ton of rare earth elements can save over 2,000 pounds of carbon dioxide emissions. Specialty metal recycling practices are not only environmentally crucial but also economically vital.
As demand for high-tech devices and clean energy technologies increases, specialty metals like titanium, tungsten, and rare earth elements have become essential to modern industry. Yet their extraction carries a significant environmental cost. This article explores how innovative recycling approaches are transforming the specialty metals industry, maximizing both sustainability and economic value.
From aerospace alloys to smartphone components, specialty metals enable the advanced technologies we rely on daily. However, mining these critical materials often involves energy-intensive processes and toxic byproducts. As supplies dwindle and environmental concerns grow, efficient recycling has emerged as an essential solution.
By implementing best practices in specialty metal recovery and reprocessing, the industry is pioneering circular economy models that conserve resources, reduce emissions, and drive technological progress.
Identifying and Sorting Specialty Metals
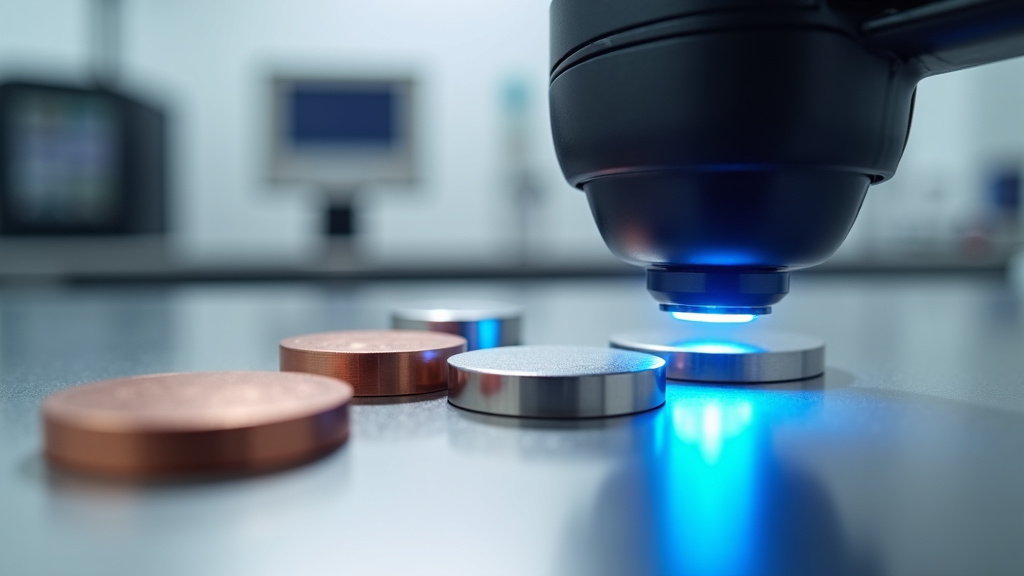
Proper identification and sorting of specialty metals are critical in recycling, ensuring maximum value recovery and environmental benefits. This complex task requires expertise, precision, and the right tools to distinguish between various metal types and prevent contamination. Explore the key techniques and technologies used in this intricate process.
Metal Identification Techniques
Accurate identification of different specialty metals is the foundation of effective recycling. Several methods determine the composition and purity of metal scrap:
Visual Inspection: Experienced recyclers can often make initial assessments based on color, texture, and weight. For instance, copper has a distinct reddish-brown hue, while titanium is typically light gray.
Magnet Test: This simple yet effective method quickly separates ferrous from non-ferrous metals. Ferrous metals like steel are attracted to magnets, while non-ferrous metals such as aluminum and copper are not.
Advanced Sorting Technologies
To ensure precise identification and sorting, recycling facilities use sophisticated technologies:
X-Ray Fluorescence (XRF) Spectroscopy: This non-destructive technique analyzes the elemental composition of metals by measuring the characteristic X-rays emitted when a sample is excited by an X-ray source. XRF is highly effective for identifying and sorting various metal alloys, providing rapid and accurate results.
Optical Emission Spectrometry (OES): OES technology uses an electrical spark to vaporize a small portion of the metal sample. The emitted light is then analyzed to determine the metal’s composition, allowing for precise identification of alloys and contaminants.
Preventing Contamination
Contamination can significantly reduce the value and recyclability of specialty metals. Key strategies to minimize this issue include:
Proper Segregation: Maintain separate collection bins for different metal types to prevent mixing. Clear labeling and staff training are essential for effective segregation.
Cleaning and Preparation: Remove non-metal components, such as plastic or rubber attachments, before the sorting process. Ensure metal pieces are free from oils, paints, or other coatings that could interfere with recycling.
Checklist of Common Specialty Metals and Characteristics
- Titanium: Light gray, extremely strong, and corrosion-resistant
- Nickel: Silver-white, magnetic, and highly resistant to corrosion
- Tungsten: Dark gray, extremely dense and hard
- Molybdenum: Silver-white, high melting point, and excellent strength at high temperatures
- Cobalt: Bluish-gray, magnetic, and often used in high-temperature alloys
By implementing these identification techniques, utilizing advanced sorting technologies, and following strict contamination prevention protocols, recycling facilities can effectively process specialty metals. This not only maximizes resource recovery but also contributes to a more sustainable and circular economy for these valuable materials.
Advanced Processing Techniques for Specialty Metals
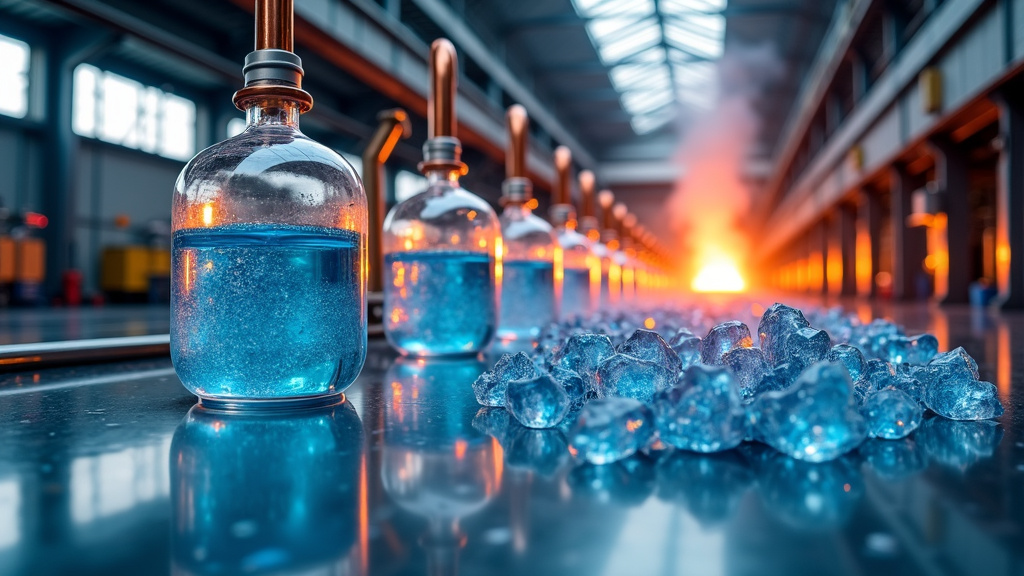
As the demand for specialty metals rises, innovative recycling methods become crucial. This section explores cutting-edge techniques transforming the recovery and purification of these valuable materials from electronic waste and other sources.
Hydrometallurgy, pyrometallurgy, and electrorefining each offer unique advantages in processing different types of specialty metals. We will explore their applications and compare their effectiveness for various materials:
Hydrometallurgy: Precision Through Aqueous Solutions
Hydrometallurgy uses aqueous solutions to extract and recover metals. This method is particularly effective for precious and rare earth metals due to its selectivity and lower energy requirements compared to other techniques.
Key advantages of hydrometallurgy include:
- High selectivity for specific metals
- Lower energy consumption
- Ability to process low-grade ores
For example, in recycling lithium-ion batteries, hydrometallurgical processes can achieve recovery rates of up to 99% for cobalt and lithium. A study in the Journal of Power Sources highlights the effectiveness of leaching with sulfuric acid and hydrogen peroxide for extracting valuable metals from spent batteries.
Pyrometallurgy: High-Temperature Metal Extraction
Pyrometallurgy utilizes high temperatures to extract and purify metals, particularly suitable for processing large volumes of mixed metal scrap.
Key features of pyrometallurgical processes include:
- Ability to process large volumes quickly
- Effective for mixed metal streams
- Can handle materials with organic contaminants
In recycling electronic waste, pyrometallurgical smelting is often used to recover copper, precious metals, and other valuable elements. However, this method may result in some volatile metal loss and requires sophisticated off-gas treatment systems to minimize environmental impact.
Electrorefining: Achieving Ultra-High Purity
Electrorefining is an electrochemical process that produces extremely pure metals, valuable for refining copper and precious metals to meet the electronics industry’s strict purity requirements.
Advantages of electrorefining include:
- Ability to achieve very high metal purity (>99.99%)
- Selective separation of metals
- Lower energy consumption compared to pyrometallurgy
For instance, copper recovered from electronic scrap through initial pyrometallurgical or hydrometallurgical processes can be further refined to 99.99% purity using electrorefining, making it suitable for high-end applications in the electronics sector.
Comparing Techniques for Different Specialty Metals
We can compare the suitability of these techniques for various specialty metals:
1. Rare Earth Elements (e.g., Neodymium, Dysprosium):
– Best suited for hydrometallurgy due to its selectivity and ability to separate individual rare earth elements.
– Pyrometallurgy is less effective due to similar chemical properties among rare earths.
2. Precious Metals (Gold, Silver, Platinum Group Metals):
– All three methods can be effective, often used in combination.
– Hydrometallurgy excels in selective leaching.
– Pyrometallurgy is useful for initial concentration.
– Electrorefining achieves ultra-high purity.
3. Specialty Battery Metals (Lithium, Cobalt, Nickel):
– Hydrometallurgy is preferred for its high recovery rates and lower environmental impact.
– Pyrometallurgy can be used for initial processing but may result in lithium loss.
4. Refractory Metals (Tungsten, Molybdenum):
– Pyrometallurgy is often favored due to high melting points.
– Hydrometallurgy can be effective for certain compounds.
The choice of processing technique depends on factors such as the specific metals involved, the composition of the feed material, environmental considerations, and desired product purity. As technology advances, we are likely to see even more innovative approaches to specialty metal recovery, further improving efficiency and sustainability in this critical industry.
Environmental Considerations in Specialty Metal Recycling
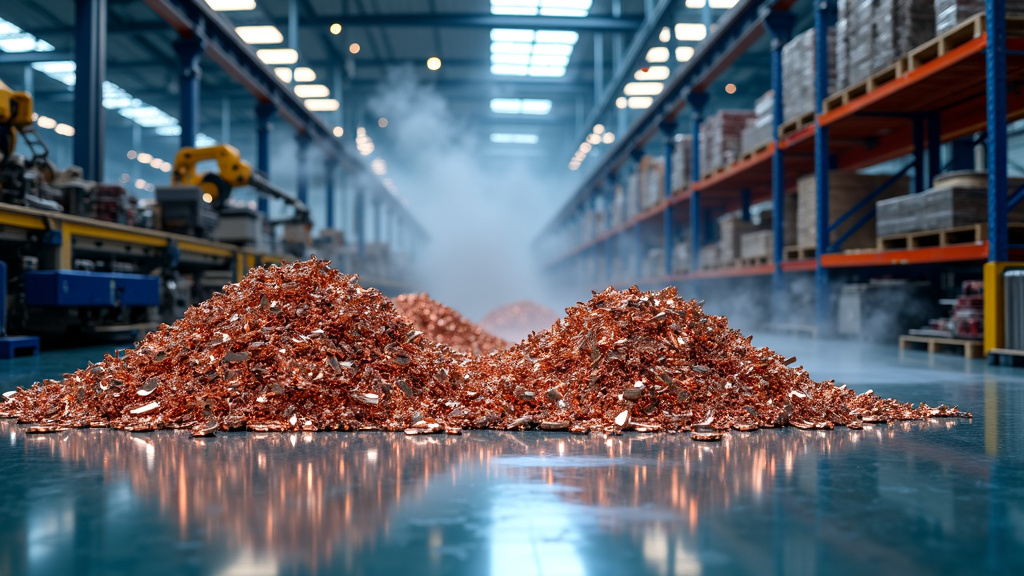
Specialty metal recycling plays a crucial role in reducing the environmental impacts associated with metal production. By reclaiming and reprocessing materials like rare earth elements, precious metals, and high-performance alloys, we can significantly decrease the need for environmentally harmful mining practices while conserving valuable natural resources.
One of the most compelling benefits of specialty metal recycling is the substantial reduction in energy consumption and greenhouse gas emissions. For instance, recycling aluminum requires up to 95% less energy than producing it from raw bauxite ore. This translates to a dramatic decrease in carbon dioxide emissions – for every ton of aluminum recycled, nearly 9 tons of CO2 emissions are prevented.
Beyond energy savings, recycling specialty metals helps preserve biodiversity and ecosystems that would otherwise be disrupted by mining activities. Open-pit mines and ore processing facilities can devastate local habitats, contaminate water sources, and release toxic chemicals into the environment. By meeting demand through recycled materials, we can minimize the expansion of these harmful extraction operations.
Best Practices for Sustainable Specialty Metal Recycling
While recycling offers clear environmental advantages, the process itself must be carefully managed to maximize benefits and avoid unintended consequences. Industry leaders are adopting several key practices to ensure specialty metal recycling remains a net positive for sustainability:
Advanced sorting technologies have revolutionized the ability to efficiently separate and purify different metal types from complex scrap sources. Techniques like X-ray fluorescence, eddy current separation, and laser-induced breakdown spectroscopy allow for precise identification and segregation of valuable specialty metals.
Closed-loop water recycling systems dramatically reduce freshwater consumption and prevent contaminated wastewater from polluting local ecosystems. By treating and reusing process water, specialty metal recyclers can operate with minimal impact on water resources.
Overcoming Challenges in Specialty Metal Recycling
Despite its promise, specialty metal recycling faces obstacles that must be addressed to reach its full potential. One major challenge is the complex, multi-material nature of many products containing specialty metals. For example, smartphones may contain over 60 different elements, making complete separation and recovery difficult.
To tackle this issue, manufacturers are increasingly embracing design for recyclability principles. By considering end-of-life disassembly and material recovery during the product development phase, companies can create goods that are easier to recycle efficiently.
Another hurdle is the lack of standardized processes for handling certain specialty metals, particularly those used in emerging technologies. As demand for materials like lithium, cobalt, and rare earth elements grows, developing cost-effective and environmentally sound recycling methods for these metals is becoming increasingly urgent.
Collaboration between industry, academia, and policymakers will be essential to drive innovation in specialty metal recycling. By investing in research and development, sharing best practices, and implementing supportive regulations, we can unlock the full environmental and economic potential of this critical sustainability strategy.
Specialty metal recycling represents a powerful tool for reducing the environmental footprint of our technology-driven society. As we continue to refine and expand recycling capabilities, we move closer to a truly circular economy for these invaluable materials – one that meets our needs while respecting planetary boundaries.
Market Trends and Economic Factors in Specialty Metal Recycling
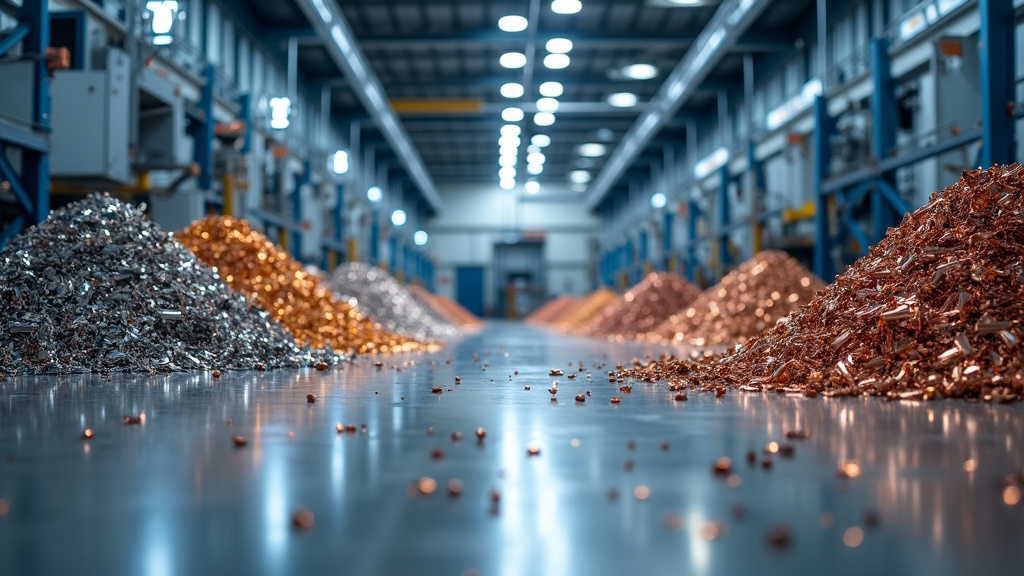
The specialty metal recycling industry operates in a dynamic economic landscape, where market trends and global factors significantly influence pricing and demand. Understanding these forces is crucial for industry stakeholders to navigate the complexities of this sector successfully.
Current Market Trends
The global metal recycling market is experiencing robust growth, with projections indicating an expansion from USD 915.44 billion in 2024 to USD 1291.73 billion by 2033, growing at a compound annual growth rate (CAGR) of 3.9%. This upward trajectory is driven by several key factors shaping the industry’s future.
One prominent trend is the increasing emphasis on sustainability and circular economy principles. As industries worldwide strive to reduce their environmental footprint, the demand for recycled specialty metals has surged. This shift is not just environmentally motivated; it’s economically savvy too. Recycling metals typically requires significantly less energy than primary production—sometimes 10 to 20 times less—making it an attractive option for cost-conscious manufacturers.
Another notable trend is the technological advancements in recycling processes. Innovations such as X-ray transmission (XRT) technology are revolutionizing the industry, enabling more efficient separation of aluminum from heavy metals in a single process. These technological leaps are enhancing the quality and purity of recycled metals, making them increasingly competitive with virgin materials.
Pricing Factors in Specialty Metal Recycling
The pricing of recycled specialty metals is influenced by a complex interplay of factors. Supply and demand dynamics play a pivotal role, with prices fluctuating based on the availability of scrap metal and the needs of end-use industries such as automotive, construction, and electronics manufacturing.
Global economic conditions significantly impact pricing. During periods of economic expansion, industries ramp up production, increasing demand for both raw and recycled materials. Conversely, economic downturns can lead to reduced demand and lower prices. The recent global economic uncertainties have introduced volatility into the market, making price forecasting challenging.
Currency fluctuations and international trade policies also exert considerable influence on pricing. As specialty metals are often traded globally, changes in exchange rates can affect their competitiveness in different markets. Trade tariffs and regulations can create additional complexities, potentially altering established supply chains and pricing structures.
Global Demand for Recycled Specialty Metals
The demand for recycled specialty metals is growing across various sectors. The automotive industry, in particular, is a significant driver, with an increasing focus on lightweight materials for electric vehicles. The construction sector, too, is boosting demand as it embraces sustainable building practices.
Geographically, Asia-Pacific leads the global metal recycling market, accounting for the largest share. The rapid industrialization and urbanization in countries like China and India are fueling this demand. North America follows as the second-largest market, with stringent environmental regulations promoting recycling practices.
An interesting trend is the growing importance of urban mining—extracting valuable metals from e-waste and other urban waste streams. As the volume of electronic waste continues to rise globally, this practice is becoming increasingly significant in meeting the demand for specialty metals.
Economic Challenges and Opportunities
While the outlook for specialty metal recycling is generally positive, the industry faces several economic challenges. Price volatility remains a concern, with factors like fluctuating oil prices and geopolitical tensions capable of disrupting market stability.
The industry also grapples with the need for substantial investments in advanced recycling technologies. While these investments can yield long-term benefits, they present short-term financial hurdles for many recyclers.
However, these challenges also present opportunities. Companies investing in innovative recycling technologies and sustainable practices are likely to gain a competitive edge. Moreover, as governments worldwide implement stricter environmental regulations, recyclers adhering to high standards are poised to benefit from increased demand and potential policy incentives.
In conclusion, the specialty metal recycling industry stands at a pivotal juncture. By staying attuned to market trends, understanding pricing dynamics, and adapting to evolving global demand, stakeholders can position themselves for success in this vital and growing sector. As the world increasingly recognizes the importance of sustainable resource management, the role of specialty metal recycling in the global economy is set to become even more significant in the years to come.
Embracing Innovation in Specialty Metal Recycling
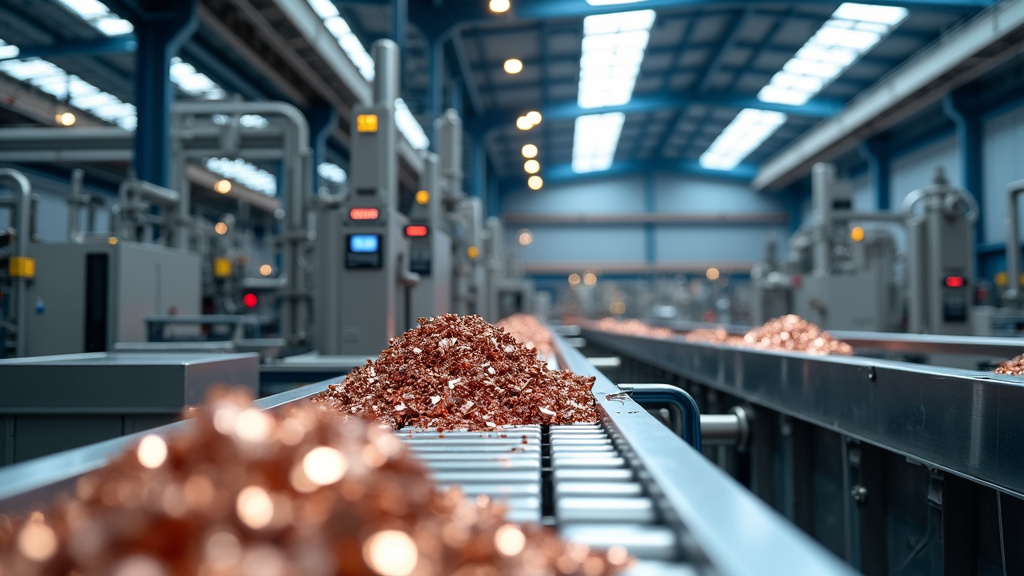
The future of specialty metal recycling is closely linked to continuous innovation and adaptation. The rapidly changing landscape of recycling technologies and practices requires businesses to stay informed and proactive in their approach to metal waste management.
By adopting cutting-edge solutions, companies can greatly enhance their recycling efficiency, reduce environmental impact, and potentially discover new revenue streams. From advanced sorting techniques to innovative extraction methods, the possibilities for improvement are vast and promising.
Navigating this complex field requires expertise and experience. Partnering with seasoned professionals like Okon Recycling is invaluable. With their knowledge of industry trends and best practices, such partnerships can position your business at the forefront of sustainable and efficient specialty metal recycling.
Consider the potential benefits of collaborating with recycling experts. How might it enhance your sustainability efforts? Could it positively impact your bottom line? The answers to these questions could reshape your approach to metal waste management and contribute to a more circular economy.
The path to optimal specialty metal recycling is paved with innovation, collaboration, and a commitment to sustainability. By staying open to new ideas and fostering strategic partnerships, businesses can turn metal waste challenges into opportunities for growth and environmental stewardship. To explore how Okon Recycling can help elevate your recycling practices, contact them at 214-717-4083.