5901 Botham Jean Blvd, Dallas, TX 75215
Precipitation Hardening: A Key Process in Metal Strengthening
March 30, 2025Precipitation hardening, or age hardening, is a heat treatment technique that significantly enhances the strength and hardness of certain metal alloys. This process involves forming extremely small, uniformly dispersed particles within the metal’s microstructure, which act as microscopic barriers to impede the movement of dislocations and improve the material’s mechanical properties.
The true value of precipitation hardening lies in its ability to transform relatively soft and malleable alloys into high-strength materials suitable for demanding applications. From aerospace components to high-performance automotive parts, precipitation-hardened alloys are essential in industries where strength-to-weight ratio is crucial.
As we explore this fascinating process further, we’ll uncover the science behind this metallurgical transformation and examine how it’s influencing modern engineering materials.
Optimizing Precipitation Hardening: Key Factors for Success
To truly harness the benefits of precipitation hardening, engineers and metallurgists must carefully control various factors throughout the process. By fine-tuning these elements, industries can maximize the strength, durability, and performance of precipitation-hardened alloys. Let’s explore the critical considerations for optimizing precipitation hardening.
Precise Control of Heat Treatment Cycles
The effectiveness of precipitation hardening hinges significantly on precise heat treatment cycles. These involve carefully controlled temperatures and times for solutionizing, quenching, and aging the alloys. For instance, aluminum alloys commonly undergo solutionizing at temperatures around 500-550°C, followed by rapid quenching to trap alloying elements in solution.
Optimizing these heat treatment parameters—such as aging temperature, duration, and cooling rates—is crucial. Even minor deviations can significantly alter the size, distribution, and coherence of precipitates, dramatically influencing the material’s final properties. Accurate temperature control systems and stringent process monitoring ensure repeatable and predictable outcomes.
Alloy Composition and Selection
The choice of alloy composition directly impacts the efficiency and effectiveness of precipitation hardening. Different elements influence precipitation kinetics and precipitate characteristics in unique ways. For example, copper additions in aluminum alloys (such as the 2000 series) promote the formation of finely dispersed, strengthening precipitates upon aging.
Selecting the right alloying elements and precise elemental ratios is critical. This selection determines the potential peak strength, ductility, corrosion resistance, and heat-treatment response of the material. Industry-specific alloy formulations, like Al-Zn-Mg-Cu alloys (7000 series), are optimized to achieve superior mechanical properties tailored for aerospace and automotive applications.
Advanced Microstructural Analysis Techniques
To ensure optimal precipitation hardening outcomes, comprehensive microstructural analysis is essential. Advanced techniques such as scanning electron microscopy (SEM), transmission electron microscopy (TEM), and atom probe tomography (APT) enable scientists to examine precipitate formation at nanoscale resolutions.
Utilizing these analytical methods helps identify precipitate phases, measure particle sizes, and evaluate dispersion uniformity. This detailed insight guides adjustments in heat treatment and alloy composition, ensuring materials achieve their maximum performance potential.
Computational Modeling for Enhanced Predictability
The integration of computational modeling and simulation techniques has revolutionized precipitation hardening optimization. Software tools such as CALPHAD (Calculation of Phase Diagrams) and finite element modeling (FEM) allow engineers to predict precipitation kinetics and microstructure evolution with remarkable accuracy.
Computational methods reduce trial-and-error experimentation by enabling virtual optimization of processing parameters and alloy compositions. Industries leveraging computational modeling can rapidly prototype new alloys, predict long-term stability, and efficiently optimize existing materials for enhanced performance and cost-effectiveness.
Sustainability in Precipitation Hardening Processes
While precipitation hardening delivers exceptional material performance, the environmental impact of energy-intensive heat treatments raises sustainability concerns. Addressing this challenge involves exploring eco-friendly alternatives, such as shorter aging cycles or innovative processing techniques like thermomechanical treatments (TMT).
Researchers are actively investigating methods to reduce energy consumption and carbon emissions during precipitation hardening. These efforts align with global sustainability goals and help industries balance performance demands with environmental responsibility.
By mastering these key factors, industries can fully leverage the potential of precipitation hardening, developing advanced materials that meet the stringent requirements of modern engineering while maintaining a commitment to sustainability and efficiency.
Applications of Precipitation Hardening in Industry
Precipitation hardening is a fundamental technique in materials engineering, significantly impacting the aerospace, automotive, and structural engineering sectors. This metallurgical process enables manufacturers to create materials with an exceptional balance of strength, ductility, and toughness—qualities essential for high-performance components in demanding applications.
In aerospace, precipitation hardening has been transformative since the early days of flight. The Wright brothers’ historic 1903 flight benefited from an aluminum-copper alloy used in their engine’s crankcase, marking the beginning of aerospace aluminum alloys. Today, this technique is crucial in developing lightweight yet robust materials for aircraft structures and engines.
Modern aerospace applications extensively use precipitation-hardened alloys. For example, 15-5PH and 17-4PH stainless steels, known for their strength and corrosion resistance, are widely used in aircraft components. These alloys undergo specific heat treatments to achieve optimal mechanical properties, ensuring safety and performance in the challenging conditions of flight.
Automotive Industry Advancements
The automotive sector utilizes precipitation hardening to meet increasing demands for fuel efficiency and safety. Aluminum alloys, particularly those in the 6000 and 7000 series, have become essential in vehicle manufacturing due to their excellent strength-to-weight ratio achieved through precipitation hardening.
For instance, the 6061-T6 aluminum alloy, commonly used in car frames and body panels, gains its strength through a carefully controlled precipitation hardening process. This allows automakers to reduce vehicle weight without compromising structural integrity, leading to improved fuel economy and performance.
Additionally, precipitation-hardened nickel alloys are used in high-performance engine components such as turbocharger wheels and exhaust valves. These parts must withstand extreme temperatures and mechanical stresses, showcasing the versatility of precipitation hardening in automotive engineering.
Structural Engineering Innovations
In structural engineering, precipitation hardening has enabled the creation of stronger, more durable buildings and infrastructure. High-strength, low-alloy (HSLA) steels, often incorporating precipitation hardening, are used in bridges, skyscrapers, and other large-scale structures.
The process allows engineers to design structures with thinner, lighter components without sacrificing strength or safety. For example, precipitation-hardened steel beams can support greater loads while using less material, reducing construction costs and environmental impact.
Moreover, aluminum alloys treated through precipitation hardening are increasingly used in modern architecture. Their corrosion resistance and high strength-to-weight ratio make them ideal for facades, window frames, and structural supports in buildings where aesthetics and performance are crucial.
Advancements in Alloy Development
Ongoing research in precipitation hardening continues to advance material science. Scientists are exploring new alloy compositions and heat treatment processes to further enhance material properties. For example, recent studies focus on improving the corrosion resistance of precipitation-hardened stainless steels for aerospace applications.
One significant advancement is the development of custom alloys like Custom450 and AM350, which exhibit superior corrosion resistance in acidic environments. These alloys demonstrate the potential for creating materials tailored to specific industry needs through precise control of the precipitation hardening process.
Furthermore, the automotive industry is investing in research to develop aluminum alloys with enhanced formability and strength. These efforts aim to create materials that can be easily shaped into complex forms while maintaining the high strength required for safety-critical components.
Future Prospects and Challenges
As industries continue to demand materials with improved properties, precipitation hardening remains at the forefront of materials engineering. The future may see the integration of computational modeling and artificial intelligence to optimize alloy compositions and heat treatment processes, potentially leading to materials with unprecedented performance characteristics.
However, challenges remain in scaling up production of advanced precipitation-hardened alloys while maintaining cost-effectiveness. Additionally, the environmental impact of heat treatment processes used in precipitation hardening is a concern, driving research into more energy-efficient and sustainable manufacturing methods.
In summary, precipitation hardening continues to be a vital technique in creating high-performance materials across various industries. Its ability to enhance material properties significantly while allowing for precise control makes it an indispensable tool in the ongoing quest for stronger, lighter, and more durable materials in aerospace, automotive, and structural engineering applications.
The Future of Precipitation Hardening and Sustainable Manufacturing
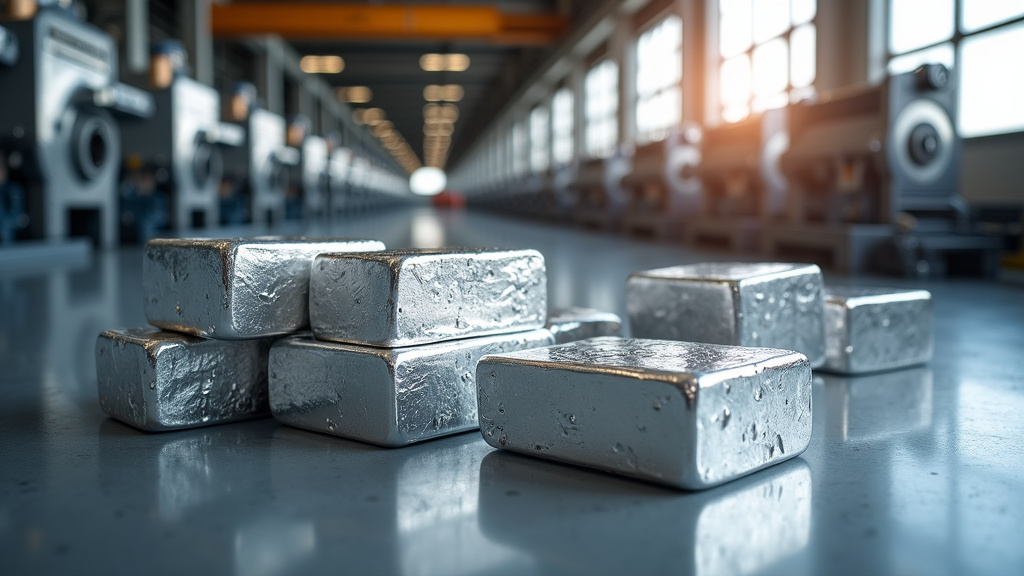
Looking ahead in materials science and manufacturing, precipitation hardening’s role in creating stronger, lighter alloys is undeniable. The industry is shifting towards sustainability, balancing performance with environmental responsibility.
This shift emphasizes efficient recycling processes for specialized alloys. Reclaiming and repurposing these high-value materials is vital for supporting a circular economy in metal manufacturing.
Companies like Okon Recycling are key players in sustainable manufacturing. Their expertise in handling complex alloys ensures that precipitation hardened materials, once difficult to recycle, can now be effectively reintegrated into production.
This approach reduces waste and conserves resources and energy. Recycling metals typically requires much less energy than primary production; for example, recycling aluminum uses only about 5% of the energy needed for primary production, significantly reducing carbon emissions.
As industries prioritize sustainability, specialized recycling services will grow in importance. By facilitating the efficient reuse of high-performance alloys, these services bridge the gap between advanced materials science and environmental stewardship.
To learn more about Okon Recycling’s contribution to a sustainable future in metal manufacturing, contact Okon Recycling at 214-717-4083.