5901 Botham Jean Blvd, Dallas, TX 75215
What Is a Super Alloy: Understanding High-Performance Metals
March 27, 2025Imagine a metal that withstands the scorching heat of a jet engine, resists corrosion in harsh environments, and maintains its strength under extreme pressure. This is the remarkable world of superalloys—advanced materials engineered to push the boundaries of modern manufacturing and technology.
Superalloys are the unsung heroes of industries ranging from aerospace to energy production, quietly enabling many technological marvels we rely on daily. These high-performance metals, primarily composed of nickel, cobalt, or iron-based materials, exhibit exceptional mechanical strength, resistance to oxidation, and thermal stability in conditions that would cause conventional metals to fail.
What sets superalloys apart from their more common metallic counterparts is their unique ability to maintain—and sometimes even increase—their strength at temperatures exceeding 540°C (1000°F). This extraordinary property makes them indispensable in applications where extreme heat and corrosive environments are the norm.
Composition and Properties of Super Alloys
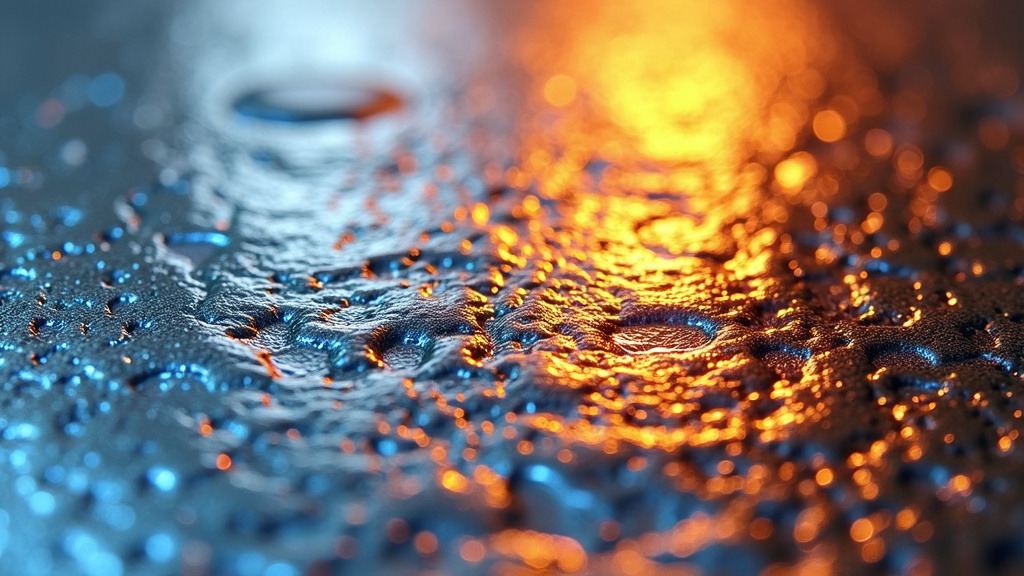
Super alloys are a remarkable class of materials designed to endure extreme conditions. These high-performance metals typically contain a carefully balanced mix of elements, with nickel, cobalt, and chromium forming the foundation of many formulations. The unique composition of super alloys grants them an exceptional array of properties that make them invaluable in demanding industrial applications.
At the heart of super alloy performance is their impressive high-temperature strength. Unlike conventional metals that weaken significantly at elevated temperatures, super alloys maintain their mechanical integrity even when pushed to their limits. This extraordinary thermal stability results from the complex interplay between alloying elements and the formation of strengthening precipitates within the metal matrix.
One of the standout characteristics of super alloys is their excellent surface stability. When exposed to harsh environments, these materials form protective oxide layers that shield the underlying metal from further degradation. This self-healing property is crucial in applications where component longevity is essential, such as in jet engines or industrial furnaces.
Resistance to Creep and Corrosion
Super alloys exhibit remarkable resistance to creep, the tendency of materials to deform slowly under constant stress at high temperatures. This property is essential in applications like gas turbines, where components must maintain dimensional stability over extended periods. The creep resistance of super alloys is attributed to their unique microstructure, which effectively impedes the movement of dislocations within the crystal lattice.
Corrosion resistance is another hallmark of super alloys, making them indispensable in chemical processing industries. The presence of elements like chromium and molybdenum contributes to the formation of passive oxide layers that protect against aggressive chemical environments. This corrosion resistance, combined with their mechanical strength, allows super alloys to perform reliably where other materials would rapidly deteriorate.
Applications Across Industries
The exceptional properties of super alloys have led to their widespread adoption in various high-stakes industries. In aerospace, these materials are crucial for manufacturing turbine blades, combustion chambers, and other critical components that must withstand extreme temperatures and stresses. Power generation plants rely on super alloys for turbine components, where efficiency and longevity are directly tied to material performance.
In the chemical processing sector, super alloys find applications in reactors, heat exchangers, and piping systems exposed to corrosive substances and high temperatures. Their ability to maintain structural integrity in these harsh conditions makes them invaluable for ensuring safety and operational efficiency.
Tailoring Properties for Specific Needs
The versatility of super alloys lies in the ability to fine-tune their composition to meet specific application requirements. By adjusting the proportions of alloying elements or introducing new ones, metallurgists can enhance particular properties such as oxidation resistance, creep strength, or thermal stability. This tailoring process has led to the development of numerous super alloy variants, each optimized for different operational environments.
As technology advances and industrial demands evolve, the field of super alloy development continues to push boundaries. Researchers are exploring new compositions and processing techniques to create materials with even greater temperature capabilities, improved corrosion resistance, and enhanced mechanical properties. These ongoing innovations promise to expand the horizons of what’s possible in high-performance engineering applications.
In summary, the unique composition and extraordinary properties of super alloys make them indispensable materials in today’s most challenging industrial environments. From the extreme heat of jet engines to the corrosive atmosphere of chemical plants, these remarkable metals continue to enable technological advancements and push the limits of material performance.
Super Alloy Type | Primary Alloying Element | Key Properties | Common Applications |
---|---|---|---|
Nickel-Based | Nickel | Exceptional strength, corrosion resistance, thermal stability | Aerospace components, gas turbine engines, chemical processing equipment |
Cobalt-Based | Cobalt | High-temperature oxidation resistance, thermal fatigue resistance | Gas turbine blades, industrial furnaces, medical implants |
Iron-Based | Iron | Cost-effective, good oxidation resistance, mechanical strength | Nuclear power generation, automotive engineering |
Applications of Super Alloys in Modern Industry
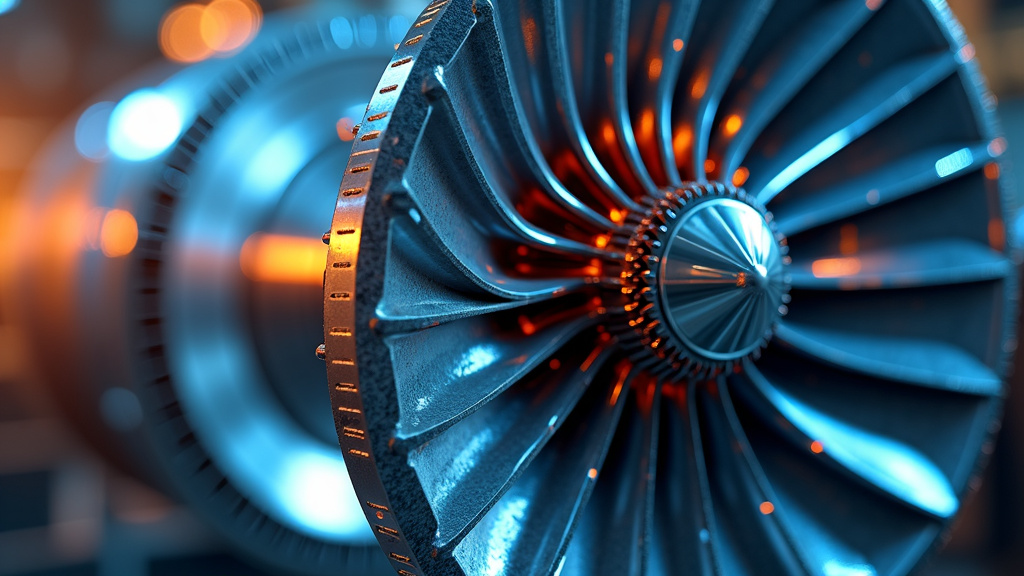
Super alloys are pivotal in today’s high-tech sectors, offering exceptional properties that make them indispensable. These materials excel in environments where ordinary metals would fail, maintaining strength and integrity under extreme conditions.
In the aerospace industry, super alloys are crucial for aircraft engine technology. Jet engines rely on these materials for components such as turbine blades, combustors, and exhaust systems. Their ability to withstand high temperatures while resisting corrosion and maintaining structural stability is remarkable.
Beyond aerospace, super alloys are vital in power generation. Gas turbines in power plants and industrial settings benefit from their high-temperature strength and corrosion resistance, leading to more reliable and cost-effective energy production.
Aerospace: Pushing Flight Boundaries
In aerospace, super alloys excel. Turbine blades, the crown jewels of aircraft engines, must endure near-melting temperatures and resist oxidation.
Nickel-based super alloys like Inconel 718 are industry standards for these roles. Their unique microstructure, reinforced by engineered precipitates, allows them to maintain strength at high temperatures, enabling modern jet engines to achieve greater thrust and fuel efficiency.
Beyond turbine blades, super alloys are used in combustion chambers, afterburners, and spacecraft structures. Their resistance to thermal fatigue makes them ideal for parts exposed to extreme conditions during rocket launches and re-entry.
Power Generation: Fueling the Future
The power generation sector has embraced super alloys. In gas turbines, they enable higher operating temperatures, improving thermal efficiency and reducing costs and environmental impact.
Inconel super alloys are workhorses in power plant turbines, resisting corrosive effects of high-temperature steam and gases. Their stability allows for longer maintenance intervals, increasing plant reliability.
In nuclear power, super alloys ensure safety and longevity. Components in reactors must withstand high temperatures and intense radiation. Alloys like Inconel 690 offer excellent resistance to stress corrosion cracking in reactor vessel components.
Emerging Frontiers: Pushing Technological Limits
As technology advances, super alloys find new applications. In hypersonic flight, where vehicles exceed Mach 5, they manage extreme heat from atmospheric friction.
The pursuit of cleaner energy has opened new avenues for super alloys. In concentrated solar power systems, they enable receivers to withstand intense heat. In advanced nuclear reactors, super alloys are explored for their potential to endure extreme conditions.
From offshore drilling equipment to satellite components, super alloys push the boundaries of materials science. Their unique properties – strength, corrosion resistance, and stability at high temperatures – make them irreplaceable where failure is not an option.
The Environmental Impact of Super Alloy Production and Use
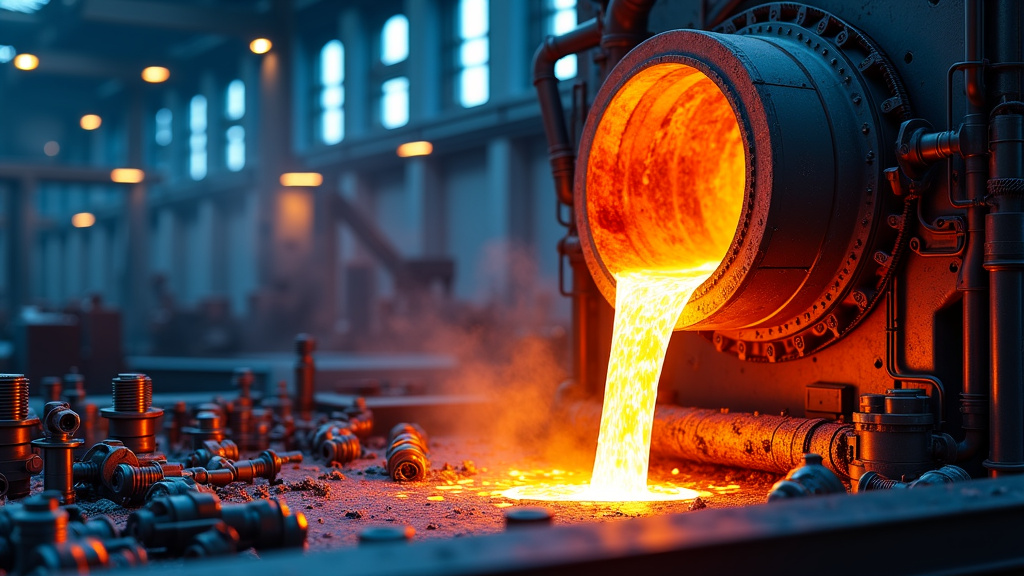
Super alloys, known for their exceptional strength and heat resistance, are crucial in advancing technology across industries. However, their production and use involve significant environmental considerations.
Let’s explore the complex relationship between super alloys and their ecological footprint.
Environmental Challenges in Super Alloy Manufacturing
The journey of super alloys begins with resource extraction, a process that can leave lasting impacts on landscapes. Mining operations for elements like nickel, cobalt, and rare earth metals often cause extensive land disturbance, potentially leading to habitat destruction and biodiversity loss.
Once extracted, these raw materials undergo energy-intensive refining processes. Producing super alloys requires extremely high temperatures, sometimes exceeding 1200°C, leading to substantial energy consumption and associated greenhouse gas emissions. Pyrometallurgical methods, such as electric arc remelting, are commonly used in super alloy manufacturing and recycling, contributing to their considerable carbon footprint.
Water pollution is another concern in super alloy production. The manufacturing process can generate wastewater containing heavy metals and other contaminants, potentially affecting local water sources if not properly managed. Additionally, the release of volatile organic compounds (VOCs) and particulate matter during production can impact air quality in surrounding areas.
Durability and Efficiency: The Environmental Benefits
While the production of super alloys poses environmental challenges, their unique properties offer significant benefits for sustainability. The exceptional durability of these materials extends the lifespan of components, reducing the frequency of replacement and, consequently, the demand for new production.
In aerospace applications, for instance, super alloys enable the development of more efficient engines. Their ability to withstand extreme temperatures allows for higher operating temperatures in turbines, translating to improved fuel efficiency and reduced emissions over the lifetime of an aircraft.
Similarly, in power generation, super alloys contribute to the efficiency of gas turbines. By allowing higher operating temperatures, these materials help increase the overall efficiency of power plants, potentially offsetting some of the environmental costs associated with their production.
Recycling: A Key to Sustainable Super Alloy Use
The recyclability of super alloys presents a significant opportunity for reducing their environmental impact. These materials contain valuable elements, many of which are considered critical raw materials due to supply risks. Effective recycling not only conserves these resources but also reduces the need for environmentally taxing primary production.
Innovative recycling techniques are constantly evolving. Hydrometallurgical methods, for example, show promise in selectively extracting individual elements from super alloy waste with lower energy consumption compared to traditional methods. According to the Quest Metals report, a two-stage leaching process using HCl solutions has been studied for recovering nickel and rhenium from nickel superalloys.
However, recycling super alloys is not without its challenges. The complex composition of these materials can make element separation difficult, and high-temperature processes used in recycling can lead to the loss of some valuable components. Overcoming these hurdles remains a focus of ongoing research and development in the field.
The Future of Super Alloys: Innovations and Sustainability
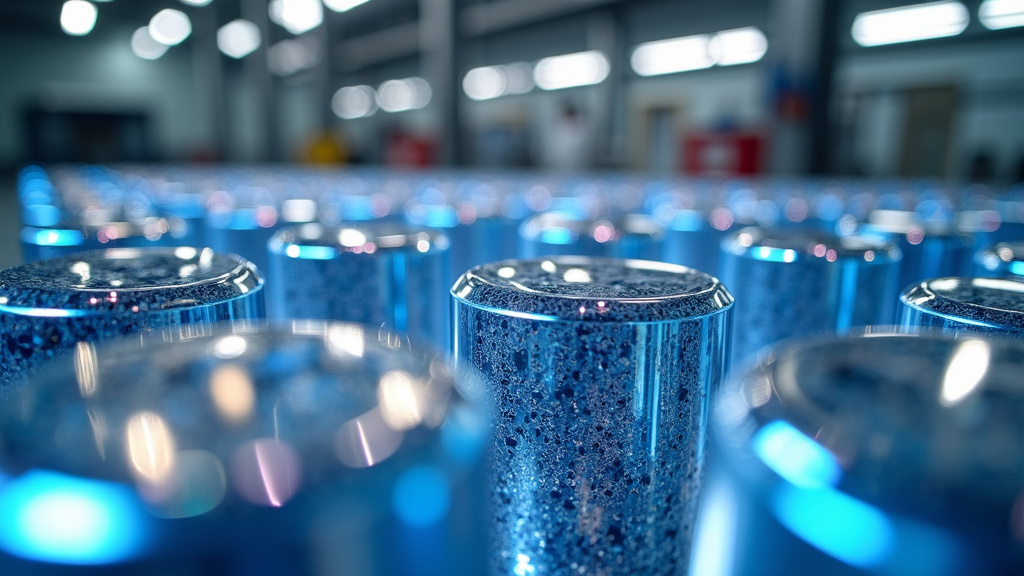
Looking ahead, the super alloys of tomorrow will likely be designed with recyclability in mind from the start. This may involve developing new alloy compositions optimized for material recovery, as well as improved recycling technologies to separate and purify individual elements. Such a holistic approach will be essential to meeting growing demand while minimizing environmental impact.
The future of super alloys is bright, with continuous innovation driving both performance and sustainability. As this field advances, recycling will play an increasingly important role in conserving resources and reducing emissions.
Companies like Okon Recycling are helping to make this vision a reality through their solutions and commitment to the circular economy. By embracing recycling and sustainable practices, the super alloy industry can look forward to a future of innovation, high performance, and environmental responsibility.
To learn more about Okon Recycling’s advanced super alloy recycling capabilities, contact them at 214-717-4083.