5901 Botham Jean Blvd, Dallas, TX 75215
What Are Alloys: Understanding Metal Mixtures and Their Recycling Potential
March 25, 2025What are alloys? In metallurgy, alloys exemplify human ingenuity and scientific progress. These materials are engineered combinations of two or more metals, crafted to enhance properties like strength, durability, or corrosion resistance. Alloys have shaped human civilization for millennia, from the bronze tools of ancient societies to today’s advanced aerospace components.
The concept of alloying metals is simple yet impactful. By blending different metallic elements, metallurgists create materials that outperform their components. This synergy allows for the development of materials tailored to meet the demands of various industries, from construction to electronics. For instance, steel, perhaps the most ubiquitous alloy, combines iron with carbon to achieve a level of strength and versatility that has built our modern world.
Understanding alloys is not just scientific curiosity; it’s crucial for a sustainable future. As we face resource scarcity and environmental impact, alloys play a significant role in recycling and resource management. The complex nature of these metal mixtures presents both challenges and opportunities in material recovery and reuse, making them central to the drive towards a circular economy.
Common Types of Alloys and Their Compositions
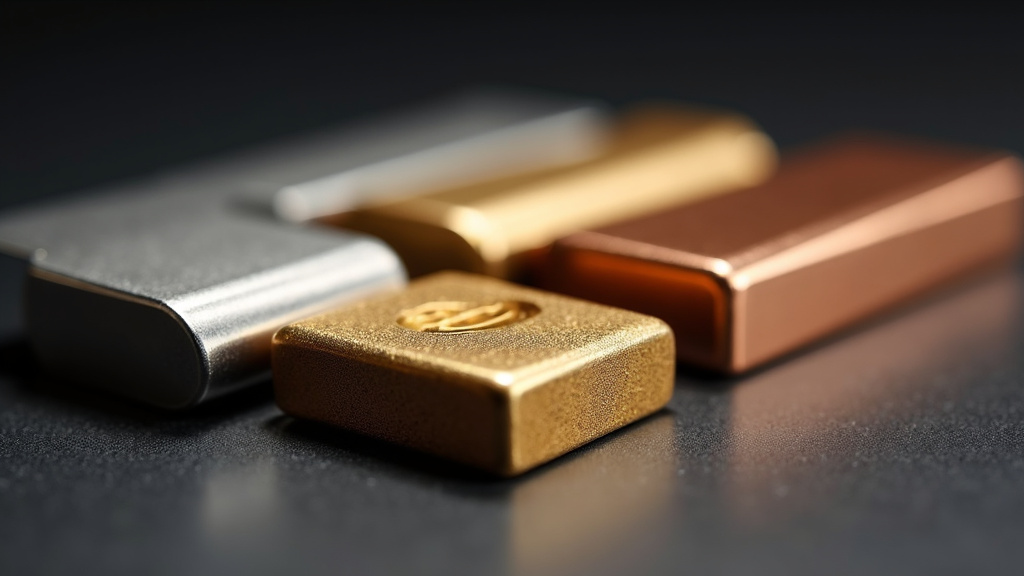
Alloys are materials formed by combining two or more metallic elements to create substances with enhanced properties. Understanding the composition of common alloys is crucial for effective recycling and reuse in manufacturing. Let’s explore some widely used alloy types and their main components.
Steel: The Iron and Carbon Powerhouse
Steel, the backbone of modern construction and manufacturing, is primarily an alloy of iron and carbon. The carbon content typically ranges from 0.03% to 1.5%, significantly influencing the steel’s properties. Low-carbon steel (0.03-0.3% carbon) offers excellent formability, while high-carbon steel (0.6-1.5% carbon) provides superior hardness and strength.
Beyond iron and carbon, steel often contains elements like chromium to enhance specific characteristics, such as corrosion resistance in stainless steel. According to the World Steel Association, over 1.8 billion tonnes of steel were produced globally in 2020, highlighting its immense importance in various industries.
Steel Type | Carbon Content (%) | Key Alloying Elements | Main Characteristics |
---|---|---|---|
Low-carbon steel | 0.03-0.30 | Iron, Carbon | High ductility, good formability |
Medium-carbon steel | 0.30-0.60 | Iron, Carbon, Manganese | Balanced strength and ductility |
High-carbon steel | 0.60-1.25 | Iron, Carbon, Chromium | High hardness, wear resistance |
Stainless steel | 0.03-0.08 | Iron, Chromium, Nickel | Excellent corrosion resistance |
Brass: The Copper and Zinc Alloy
Brass is an alloy primarily composed of copper and zinc, with copper typically making up 55-95% of the mixture. This versatile alloy is prized for its attractive gold-like appearance and excellent acoustic properties. The specific copper-to-zinc ratio varies, resulting in different types of brass with unique characteristics.
For example, yellow brass, commonly used in decorative applications, contains about 67% copper and 33% zinc. Red brass, with a higher copper content of around 85%, offers better corrosion resistance and is often used in plumbing fixtures. The malleability and conductivity of brass make it an excellent choice for musical instruments and electrical components.
Bronze: The Ancient Copper and Tin Blend
Bronze, one of the oldest known alloys, is primarily composed of copper and tin. The typical composition ranges from 88% copper and 12% tin to 97% copper and 3% tin. This alloy is renowned for its durability, resistance to corrosion, and ease of casting.
Different types of bronze exist, each with unique properties. For instance, phosphor bronze, which includes a small amount of phosphorus, exhibits improved spring qualities and fatigue resistance. Silicon bronze, incorporating silicon instead of tin, offers excellent corrosion resistance and is often used in marine applications.
The Importance of Alloy Composition in Recycling
Understanding alloy composition is crucial for effective recycling and reuse in manufacturing. Each alloy type requires specific recycling processes to maintain its valuable properties. For example, separating different grades of steel is essential to preserve the unique characteristics of each type during recycling.
Recycling metals can save up to 95% of the energy required to produce metals from raw materials. This significant energy saving underscores the importance of proper alloy identification and recycling practices.
Ultimately, the diverse world of alloys offers a wide range of materials with unique properties suited for various applications. By understanding the composition of common alloys like steel, brass, and bronze, we can ensure more efficient recycling processes and contribute to a more sustainable manufacturing industry.
The Importance of Alloy Recycling in Sustainable Manufacturing
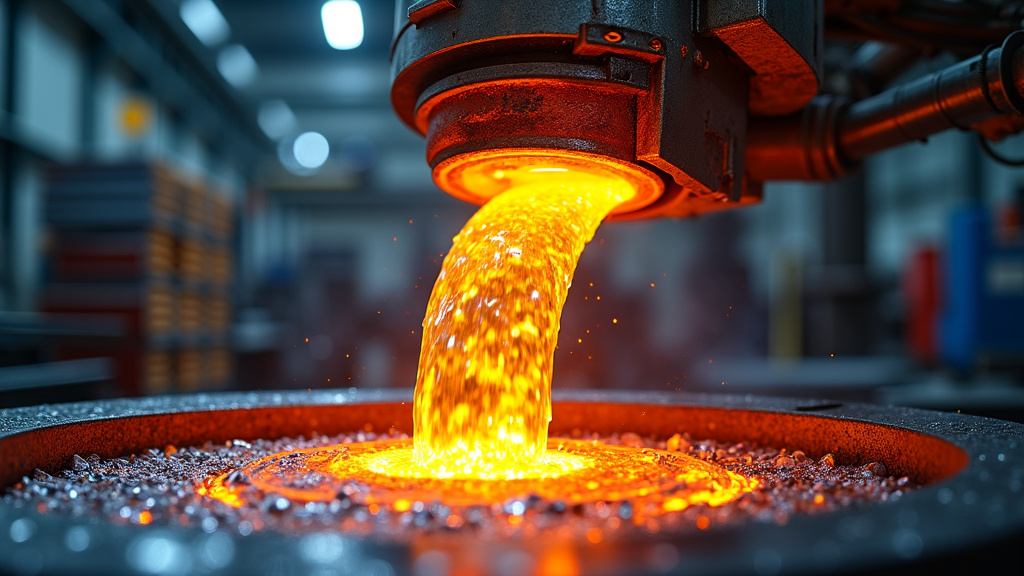
Alloy recycling is a key component of eco-friendly manufacturing, conserving raw materials and reducing energy use and environmental impact. As industries face resource depletion and climate change, alloy recycling’s role in a circular economy is vital.
Recycling alloys saves significant energy compared to producing new metals. Industry experts note that recycling requires less energy, leading to lower carbon emissions and environmental impact, making it essential in combating climate change.
Reusing metals through alloy recycling conserves raw materials and reduces environmentally harmful mining. This approach not only protects natural habitats but also extends the lifespan of metal resources for future use.
Driving the Circular Economy
Alloy recycling is crucial in promoting a circular economy, which aims to eliminate waste and maximize resource efficiency. In alloy manufacturing, this involves designing products for easy recycling, closing the loop on material use.
Recycling reduces reliance on primary materials, minimizes landfill waste, and creates new economic opportunities. These align with sustainable manufacturing principles, aiming for minimal environmental impact.
Furthermore, alloy recycling enhances resource security. As global metal demand grows, recycling ensures a stable supply, crucial for industries like aerospace and automotive manufacturing that depend on specialty alloys.
Environmental Benefits and Sustainability
Beyond energy savings and resource conservation, alloy recycling preserves biodiversity and ecosystems by reducing mining and primary metal production. It also lowers water use and pollution from metal extraction and processing.
Alloy recycling supports the United Nations’ Sustainable Development Goals, particularly those on responsible consumption, climate action, and industry innovation. It shows how industrial processes can become more eco-friendly without sacrificing growth or quality.
Alloy recycling’s importance in sustainable manufacturing is highlighted by its potential to create a resilient and efficient industrial sector. By adopting recycling technologies and circular economy principles, manufacturers can mitigate raw material price fluctuations and supply chain disruptions, leading to stable and sustainable business models.
Challenges in Alloy Recycling: Sorting and Separation
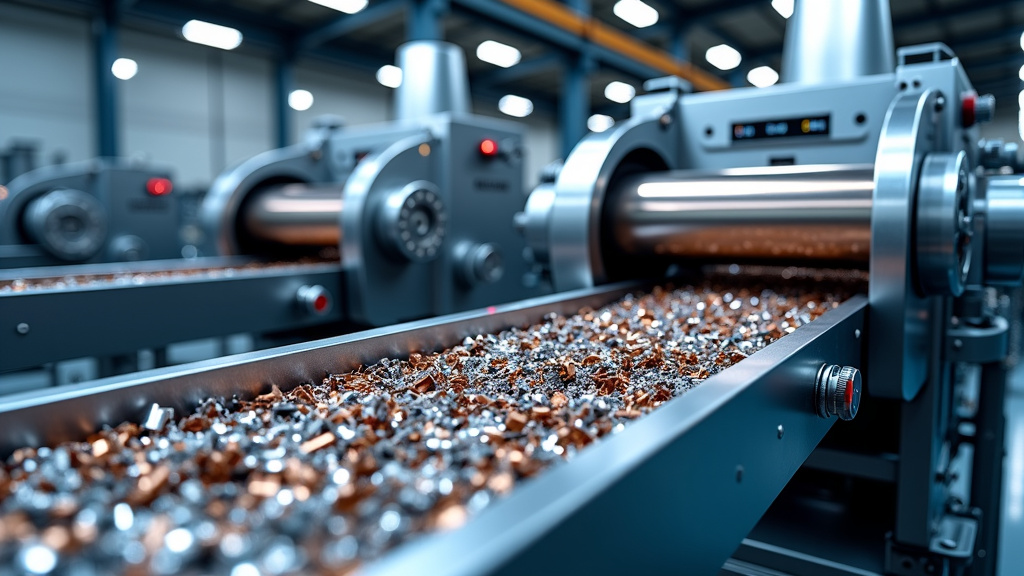
Alloy recycling presents unique challenges, especially in sorting and separating various metals. As demand for recycled materials grows, advanced techniques are essential for maximizing recovery and ensuring high-quality outputs. Here are some cutting-edge methods transforming the alloy recycling industry.
Magnetic Separation: Sorting Ferrous from Non-Ferrous
Magnetic separation is a foundational technique in metal recycling. It uses the magnetic properties of ferrous metals like iron and steel to efficiently sort them from non-ferrous materials. Advanced magnetic separators and drum magnets play a crucial role in this process, attracting ferrous metals while allowing non-magnetic materials to pass through unaffected.
Modern magnetic separation systems have become increasingly sophisticated, with some capable of detecting and sorting even weakly magnetic materials. This advancement has significantly improved the efficiency of the initial sorting stage in alloy recycling, reducing contamination and enhancing the overall quality of recovered metals.
However, magnetic separation alone is not sufficient for handling the complex mix of alloys in modern scrap. This limitation has led to the development of complementary technologies to address non-ferrous metals and more intricate alloy compositions.
Eddy Current Separation: Tackling Non-Ferrous Alloys
For non-ferrous metals like aluminum, copper, and brass, eddy current separation has emerged as a transformative technology. This method creates a magnetic field that induces electrical currents in non-ferrous metals, causing them to be repelled and separated from non-metallic materials.
Eddy current separators are particularly effective in recovering valuable non-ferrous metals from mixed waste streams. Modern systems can sort materials at high speeds and with greater precision, improving recovery rates and the purity of sorted materials, making them more valuable for reuse in manufacturing.
Spectroscopic Analysis: Precision Sorting for Complex Alloys
As alloys become more complex, traditional sorting methods often fall short. Spectroscopic analysis, a cutting-edge technique, uses the unique spectral signatures of different metals to identify and sort alloys with unprecedented accuracy.
X-ray fluorescence (XRF) and laser-induced breakdown spectroscopy (LIBS) are two spectroscopic methods gaining traction in the recycling industry. These technologies can rapidly analyze the elemental composition of alloys, allowing for precise sorting based on specific alloy grades rather than just broad metal categories.
The adoption of spectroscopic analysis has been transformative for recycling facilities dealing with high-value alloys used in aerospace, automotive, and electronics industries. It enables the recovery of rare and precious metals that might otherwise be lost, significantly enhancing the economic viability of advanced alloy recycling.
Overcoming Challenges with Integrated Systems
While each of these technologies offers significant benefits, their true power lies in integration. Modern recycling facilities are increasingly adopting multi-stage sorting systems that combine magnetic separation, eddy current separation, and spectroscopic analysis. This integrated approach allows for a more comprehensive and efficient sorting process, capable of handling the diverse and complex mix of alloys found in today’s scrap metal streams.
Moreover, integrating artificial intelligence and machine learning into these systems further enhances their capabilities. AI-powered sorting systems can adapt to variations in input materials and optimize sorting parameters in real-time, continually improving efficiency and accuracy.
Technology | Benefits |
---|---|
Energy Conservation | Recycling alloys demands less energy than manufacturing new metals, reducing carbon emissions and environmental impact. |
Resource Conservation | Recycling conserves natural resources and reduces the need for mining, preserving habitats and extending the lifespan of metal resources. |
Circular Economy | Recycling supports a circular economy by keeping materials in use longer, reducing landfill waste, and creating economic opportunities. |
Pollution Reduction | Recycling lowers water and air pollution by eliminating the need for chemical-intensive mining processes. |
Looking to the future, the challenges of alloy recycling are being met with increasingly sophisticated technological solutions. These advancements not only improve the efficiency and profitability of recycling operations but also contribute significantly to the circular economy, ensuring that valuable metals are recovered and reused rather than lost to landfills.
How Okon Recycling Can Help with Alloy Recycling
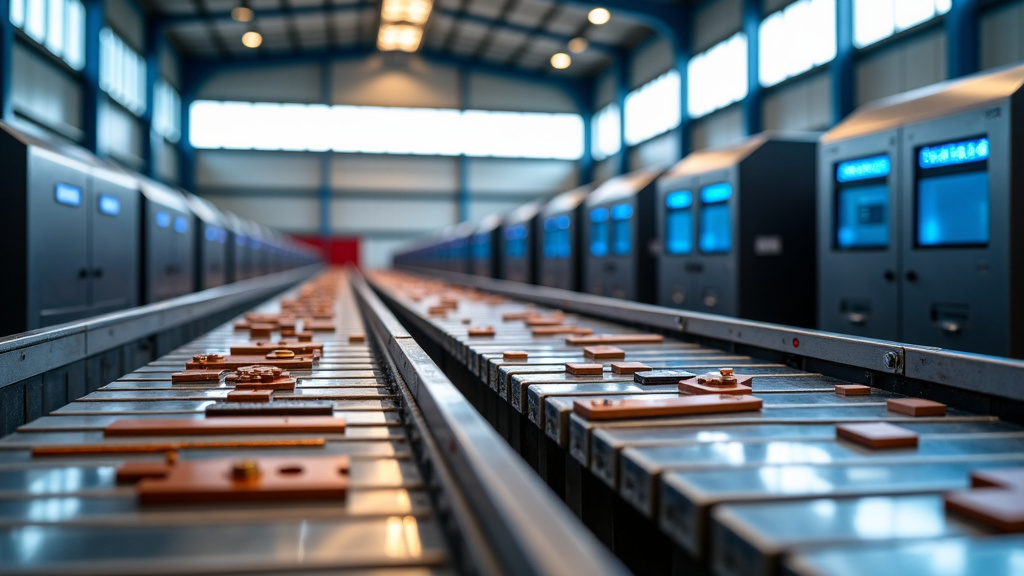
In metal recycling, Okon Recycling stands out for its innovation and sustainability. With over a century of experience, this Dallas-based company excels in alloy recycling. What distinguishes Okon in this vital field?
Okon’s alloy recycling success is driven by its commitment to advanced technology. The company uses cutting-edge sorting techniques beyond traditional methods. For example, Okon’s metal recycling services employ state-of-the-art spectrometers and XRF analyzers to accurately identify and categorize various alloys, ensuring maximum recovery and purity.
This technological edge is about more than just efficiency; it’s about responsibility. In an era where sustainability is crucial, Okon’s approach to alloy recycling significantly reduces the environmental impact of metal production. By recycling alloys, the company conserves natural resources and minimizes the energy-intensive process of primary metal extraction.
Tailored Solutions for Diverse Needs
In alloy recycling, one size doesn’t fit all, and Okon Recycling understands this well. The company offers customized recycling solutions for businesses and individuals. Whether you’re a large manufacturing plant with industrial scrap or an individual with metal items, Okon has a plan for you.
For businesses, Okon provides comprehensive scrap management services, including on-site collection, secure transportation, and detailed reporting on recycled materials. The company’s expertise covers a wide range of alloys, from common aluminum and steel to specialized materials used in aerospace and automotive industries.
Individuals looking to dispose of alloy-containing items responsibly are also accommodated. Okon’s public recycling center welcomes walk-ins and offers competitive rates for various metals and alloys. This dedication to serving both large-scale industrial clients and individual consumers underscores Okon’s holistic recycling approach.
A Century of Expertise Driving Innovation
Okon Recycling’s longevity in the industry is a testament to its resilience and a driver of its innovative practices. With over 100 years of experience, the company has adapted and improved its methods amid numerous changes in the recycling landscape.
This extensive experience translates into unmatched expertise in handling complex alloy recycling challenges. Okon’s specialists address issues like contamination in alloy scrap, a common problem that can affect recycling efficiency. Their knowledge enables them to implement sophisticated purification processes, ensuring recycled alloys meet stringent quality standards.
Moreover, Okon’s long-standing industry relationships keep them at the forefront of recycling technology. The company regularly invests in upgrading its facilities and training its staff, ensuring they lead in sustainable alloy recycling practices.
Contributing to a Sustainable Future
Choosing Okon Recycling for alloy recycling contributes to a more sustainable future. The company’s efficient recycling processes significantly reduce the carbon footprint associated with metal production. For context, recycling aluminum – a common alloy component – uses only about 5% of the energy required for primary production, according to industry data.
Metal | Energy Savings in Recycling | Energy Savings Description |
---|---|---|
Aluminum | 95% | Recycling aluminum uses 95% less energy than producing it from bauxite ore. |
General Metals | – | Recycling saves 5MWH of primary energy per ton of material, around 70% of the footprint of primary production. |
Steel | 58% | Using steel scrap reduces CO2 emissions by up to 58%. |
Okon’s commitment to sustainability extends beyond its recycling processes. The company actively participates in community outreach programs, educating the public about the importance of metal recycling and its environmental impact. This holistic approach to sustainability distinguishes Okon as not just a recycling company, but a steward of environmental responsibility.
As resource conservation and sustainable practices become increasingly crucial, Okon Recycling is ready to lead the way in alloy recycling. Their blend of century-old experience, cutting-edge technology, and unwavering commitment to sustainability makes them an ideal partner for anyone looking to responsibly recycle alloys and contribute to a greener world.
The Future of Alloy Recycling: Innovations and Opportunities
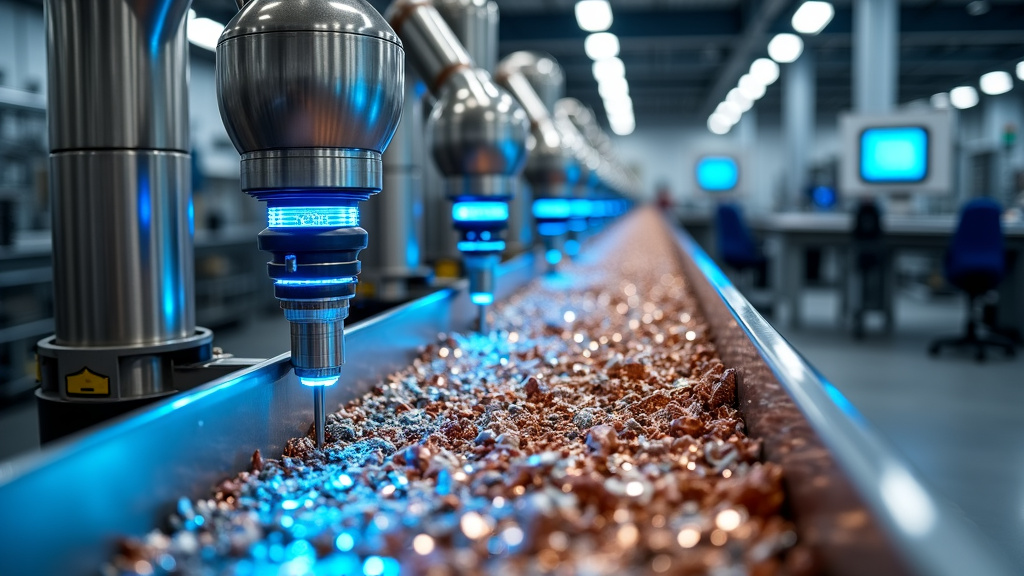
Advancements in metallurgical processes are opening new possibilities in alloy recycling. Techniques such as hydrometallurgical and electrochemical recycling are enabling the recovery of precious metals from complex electronic waste, addressing a significant challenge in modern recycling.
Looking to the future, the potential for these technologies to foster a more circular economy for metals is immense. By adopting these innovations, we can significantly reduce the need for primary metal extraction, conserving natural resources and minimizing environmental impact. The recycling industry is not just adapting to change – it’s driving it, creating new jobs and economic opportunities in the green technology sector.
We encourage all stakeholders in the metal industry to explore how they can engage with and benefit from these exciting developments. Whether you’re a manufacturer looking to increase your use of recycled alloys, or a consumer wondering how to responsibly dispose of metal products, there’s a role for everyone in this sustainable revolution. For cutting-edge recycling solutions that leverage these innovations, contact Okon Recycling at 214-717-4083.