5901 Botham Jean Blvd, Dallas, TX 75215
Sustainable Practices in Alloy Production and Recycling
February 6, 2025Did you know that recycling aluminum uses only 5% of the energy required for primary production? This isn’t just a fun fact—it’s a game-changer for the alloy production industry.
As the world pushes for lower carbon emissions, sustainable metallurgy is becoming essential, not optional.
The future of alloy production hinges on recycling. By repurposing post-consumer scrap, companies conserve resources, reduce emissions, and cut energy costs. Recycling aluminum alone reduces CO₂ emissions by up to 95% compared to primary production. This shift extends beyond aluminum—metals like copper and steel are now being reimagined through sustainable processes, reshaping global supply chains.
Leading this charge is Okon Recycling, a company committed to maximizing material recovery while minimizing environmental impact. By refining and repurposing industrial scrap, Okon ensures that valuable alloys stay in circulation, powering industries without depleting natural resources.
The momentum is undeniable. Advances in sorting, purification, and renewable-powered smelting are accelerating the transition to a circular economy for metals. Companies embracing sustainable practices aren’t just reducing waste—they’re gaining a competitive edge in a carbon-conscious market.
As we dive into the world of sustainable alloy production, we’ll explore the technologies and innovations driving this transformation. The question isn’t if a fully circular metals industry is possible—it’s how fast we can make it happen.
Advantages of Recycling in Alloy Production
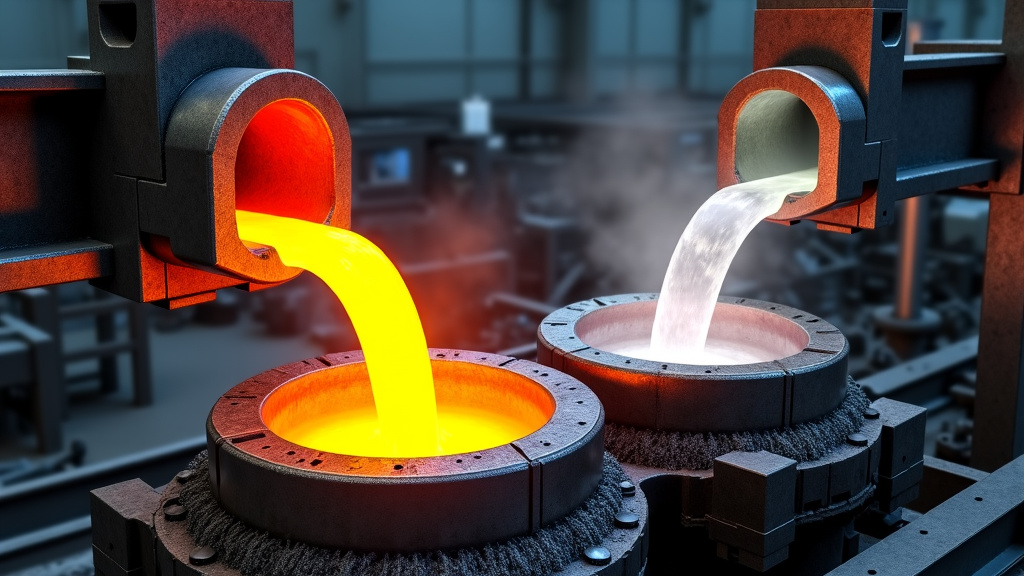
In metal production, recycling has become a transformative force, offering benefits that go beyond simple waste reduction. The advantages of recycling in alloy production are extensive, impacting energy conservation, economic growth, and environmental stewardship.
Significant Energy Savings
Recycling in alloy production offers substantial energy savings. When comparing the energy requirements of recycling to those of primary production, the contrast is significant.
For example, recycling aluminum saves 95% of the energy needed for primary aluminum production. This represents a major shift in energy use for metal production.
To illustrate, imagine the energy needed to power a small city for a year. That’s roughly the amount saved by recycling aluminum instead of producing it from raw materials. This energy-efficient process benefits other metals as well.
Steel recycling uses 56% less energy than producing steel from raw materials. These energy savings reduce greenhouse gas emissions, making recycling a key tool in combating climate change.
Metal | Energy Savings (%) |
---|---|
Aluminum | 95% |
Copper | 85% |
Steel | 60% |
Gold | 90% |
Economic Benefits: Boosting Industry and Communities
The benefits of recycling in alloy production extend beyond environmental aspects. There are significant economic advantages for industries and communities.
Recycling scrap metal reduces alloy production costs significantly, as recycled materials are often cheaper than raw materials. This cost reduction can lead to more competitive market pricing, potentially boosting sales and driving economic growth.
The recycling industry also creates jobs in collection, sorting, processing, and manufacturing, supporting local economies by providing stable employment worldwide.
Promoting the Circular Economy
Recycling in alloy production is key to the circular economy, a model aimed at eliminating waste and maximizing resource use. By keeping materials in use longer, we reduce the need for raw material extraction and minimize landfill waste.
This approach conserves finite resources like bauxite ore (used in aluminum production) and reduces the environmental impact associated with mining and processing. It’s a win-win: obtaining necessary metals while reducing environmental impact.
Reducing Landfill Waste: An Overlooked Advantage
The role of recycling in reducing landfill waste is crucial. Metals that would otherwise end up in landfills are reused through recycling, saving valuable landfill space and preventing potential soil and water contamination from metal leaching.
By diverting metals from landfills, we preserve their value. Unlike many materials, metals can be recycled indefinitely without losing properties, turning what was once considered ‘waste’ into a valuable resource.
Challenges in Implementing Sustainable Recycling
The journey towards sustainable metal recycling is fraught with obstacles that demand innovative solutions. As the industry handles increasing volumes of scrap, three primary challenges stand out:
- Contamination from mixed sources
- Degradation of metal properties
- Need for precise sorting and processing
Contamination poses a significant hurdle in recycling efforts. When scrap metal arrives from various sources, it often contains a mix of different alloys and non-metallic materials. This heterogeneity can compromise the quality of the recycled product if not properly addressed. For instance, advanced sorting systems are now being employed to combat this issue, using software intelligence to effectively process zorba, e-waste, and other mixed metal streams.
The degradation of metal properties presents another formidable challenge. Repeated recycling cycles can lead to the accumulation of tramp elements, potentially altering the mechanical and chemical properties of the recycled metal. This degradation can limit the applications for which the recycled material is suitable, potentially reducing its value and sustainability impact.
Advanced Sorting Technologies: A Game-Changer
To address these challenges, the industry is turning to cutting-edge sorting technologies. These systems are transforming the way scrap metal is processed, ensuring higher purity levels and more consistent quality in recycled products. For example, REDWAVE’s XRF sorting system integrates spectral analysis for precise alloy separation, opening up new possibilities in aluminum recycling.
The integration of artificial intelligence and machine learning into sorting systems has dramatically improved the accuracy and speed of material identification. These smart systems can quickly distinguish between different types of metals and alloys, significantly reducing contamination and improving the overall quality of recycled materials.
Robotic sorting systems are also advancing the industry. Equipped with advanced sensors and gripping technologies, these robots can efficiently pick and sort materials from conveyor belts, reducing human error and increasing processing speeds. This level of precision is crucial for maintaining the integrity of recycled metals and ensuring their suitability for high-end applications.
Creative Alloy Compositions: Turning Challenges into Opportunities
While sorting technologies address many issues, the industry is also exploring creative alloy compositions to combat quality degradation. By designing alloys that are more tolerant to impurities or that can be more easily separated during recycling, manufacturers are finding ways to maintain material properties even after multiple recycling cycles.
These innovations not only improve the quality of recycled metals but also expand their potential applications. For instance, new aluminum alloys are being developed that can withstand higher levels of impurities without compromising strength or corrosion resistance, making them ideal for use in automotive and aerospace industries.
Future Directions for Sustainable Alloy Production
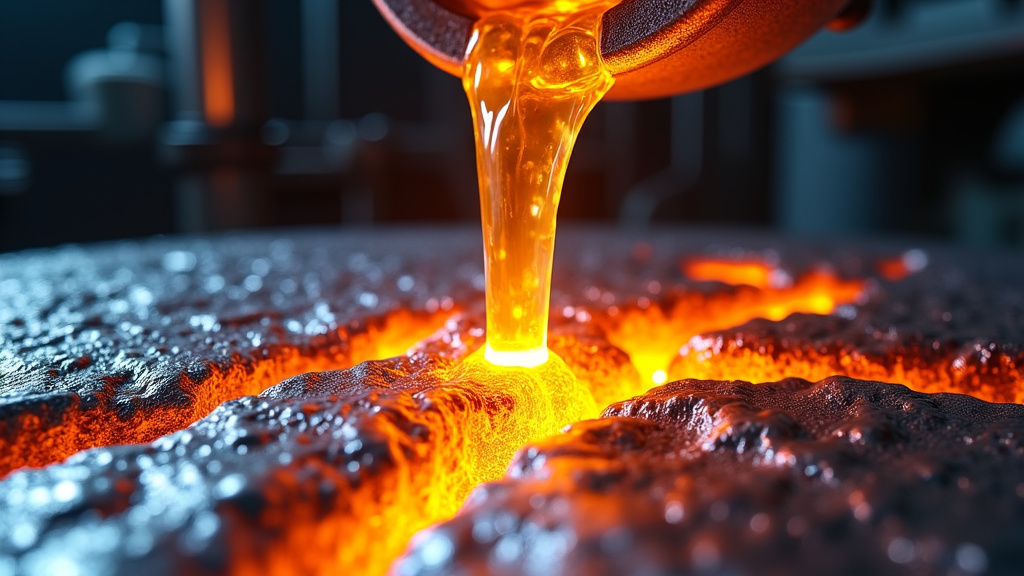
The recycling industry is on the brink of a technological transformation. Innovations in artificial intelligence, impurity-tolerant alloys, and advanced recycling technologies promise to significantly enhance the efficiency and sustainability of alloy production.
Artificial intelligence is transforming scrap metal sorting. AI-powered systems now analyze and categorize metals with remarkable accuracy and speed. According to industry experts, AI sorting technology processes materials up to 60% faster than manual methods while achieving 99% accuracy, ensuring higher quality recycled materials and reducing contamination.
AI’s potential goes beyond sorting. Machine learning algorithms are being developed to predict market trends, optimize supply chains, and identify new recycling opportunities. Imagine AI systems anticipating the exact composition of incoming scrap loads, allowing recyclers to fine-tune their processes in real-time.
The Rise of Impurity-Tolerant Alloys
An exciting development in sustainable metallurgy is the creation of new alloys designed to tolerate impurities. Traditional recycling processes often struggle with trace elements that accumulate over multiple cycles, degrading the quality of recycled metals.
Enter a new generation of ‘recycling-friendly’ alloys. Materials scientists are developing innovative compositions that maintain desirable properties even in the presence of common contaminants. Research into these impurity-tolerant alloys opens up possibilities for increasing the use of scrap metal in high-performance applications.
Imagine aluminum alloys retaining their strength and corrosion resistance despite higher levels of iron contamination, or steel remaining ductile with increased copper content. These advancements could significantly boost the proportion of recycled content in new metal products, reducing the need for energy-intensive primary production.
Enhancing Recycling Technologies
The future of metal recycling involves more than sorting and alloy design – it also includes revolutionizing the recycling process itself. Advanced technologies are being developed to recover metals more efficiently and with less environmental impact.
Innovations in pyrometallurgy and hydrometallurgy allow for more precise separation of metal components. New chemical processes can extract valuable elements from complex e-waste streams previously considered too difficult to recycle. Plasma arc technology is being explored to break down materials at the atomic level, potentially unlocking new recycling pathways for challenging materials.
These technological leaps represent a fundamental shift in how we approach metal recycling. By maximizing material recovery rates and minimizing energy consumption, these innovations are key to creating a truly circular economy for metals.
A Vision for the Future
As these technologies mature and converge, we can envision a future where ‘waste’ becomes an outdated concept in the metals industry. AI-powered sorting systems will seamlessly feed impurity-tolerant alloys into highly efficient recycling processes. The result? A closed-loop system where metals are endlessly recirculated with minimal loss of quality or value.
This is not just an environmental win – it’s an economic one too. By reducing reliance on primary ore extraction, the metals industry can significantly lower its carbon footprint and energy costs. The circular economy for metals could create new jobs, drive innovation, and ensure a stable supply of critical materials for generations to come.
The future of sustainable alloy production is promising, powered by the convergence of artificial intelligence, materials science, and advanced recycling technologies. As these innovations continue to develop and synergize, they promise to reshape the very foundations of how we produce and use metals in our society.
Benefit | Description |
---|---|
Increased Efficiency | AI-powered systems can process materials up to 60% faster than manual methods while achieving 99% accuracy. |
Improved Sorting | AI and robotics significantly enhance the sorting process, identifying metals quickly and efficiently. |
Reduced Labor Costs | AI-driven automation reduces the need for manual sorting, leading to labor savings of up to 50-70%. |
Higher Recycling Rates | AI ensures higher quality recycled materials by minimizing contamination and improving sorting accuracy. |
Safety Enhancements | AI reduces risks associated with handling hazardous materials and decreases the need for extensive safety training. |
Conclusion: The Impact of Sustainable Practices on Alloy Production
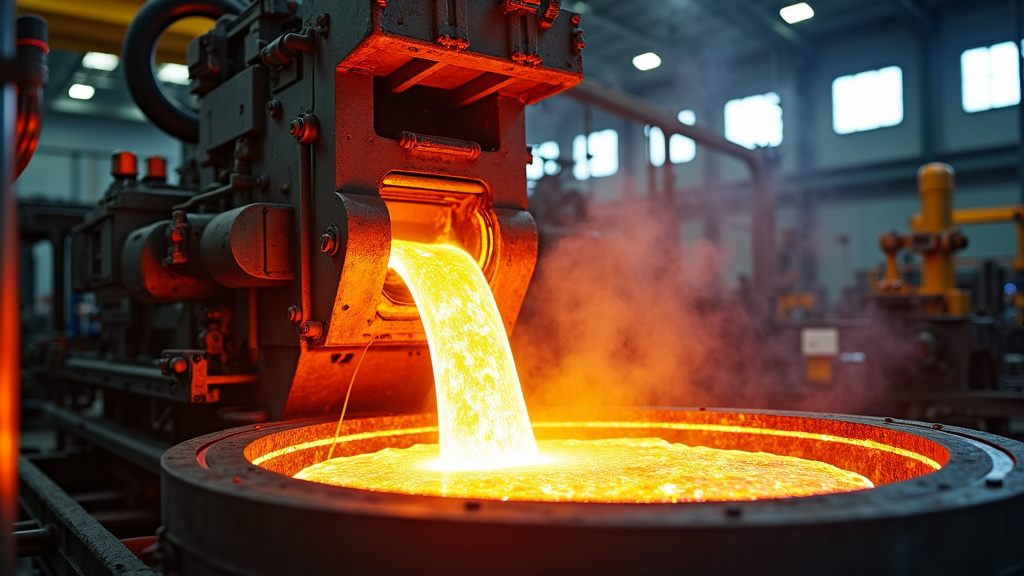
The shift toward sustainable alloy production and recycling is transforming the metals industry, offering both environmental and economic benefits. By adopting advanced technologies, manufacturers are reducing waste, cutting emissions, and optimizing resource use, paving the way for a truly circular economy.
Breakthroughs like X-ray transmission (XRT) and laser-induced breakdown spectroscopy (LIBS) have revolutionized alloy sorting and separation, ensuring higher-quality recycled materials with minimal energy use. Meanwhile, AI-driven manufacturing is streamlining production, reducing waste, and enhancing material performance. Even more exciting, solid-phase recycling methods like friction extrusion now enable direct upcycling of aluminum scrap without energy-intensive melting—drastically lowering emissions.
But technology alone isn’t enough. Achieving true sustainability requires a fundamental shift in how we design, use, and recycle metals. Waste must be seen as a valuable resource, and industries must prioritize recyclability from the start.
At Okon Recycling, we are leading this charge. With decades of expertise in industrial metal recycling, we help businesses recover, repurpose, and reintegrate valuable alloys into the supply chain. Our state-of-the-art facilities in Dallas-Fort Worth process millions of pounds of scrap, ensuring a cleaner, greener future for the metals industry.
The future of alloy production is sustainable, efficient, and circular—and now is the time to act. Join us in building a low-carbon metals industry. Contact Okon Recycling at 214-426-6566 to learn how we can help you turn scrap into opportunity.