5901 Botham Jean Blvd, Dallas, TX 75215
Recycling Alloys: A Sustainable Approach to Metal Management
March 27, 2025Recycling alloys can save up to 95% of the energy required for primary metal production. This fact underscores the significant potential of alloy recycling in conserving our planet’s resources. As industries worldwide encounter challenges in sustainable development, recycling alloys has become a vital strategy in metal management.
Alloy recycling involves collecting, processing, and reusing various metal combinations to create new products. This process not only conserves natural resources but also significantly reduces energy consumption and minimizes environmental impact. By adopting this approach, we move towards a more circular economy in the metal industry.
Consider aluminum, one of the most widely recycled alloys. Recycling aluminum saves 95% of the energy needed for primary aluminum production. This energy saving directly reduces carbon emissions, making alloy recycling an effective tool in combating climate change.
Understanding Alloys and Their Recyclability
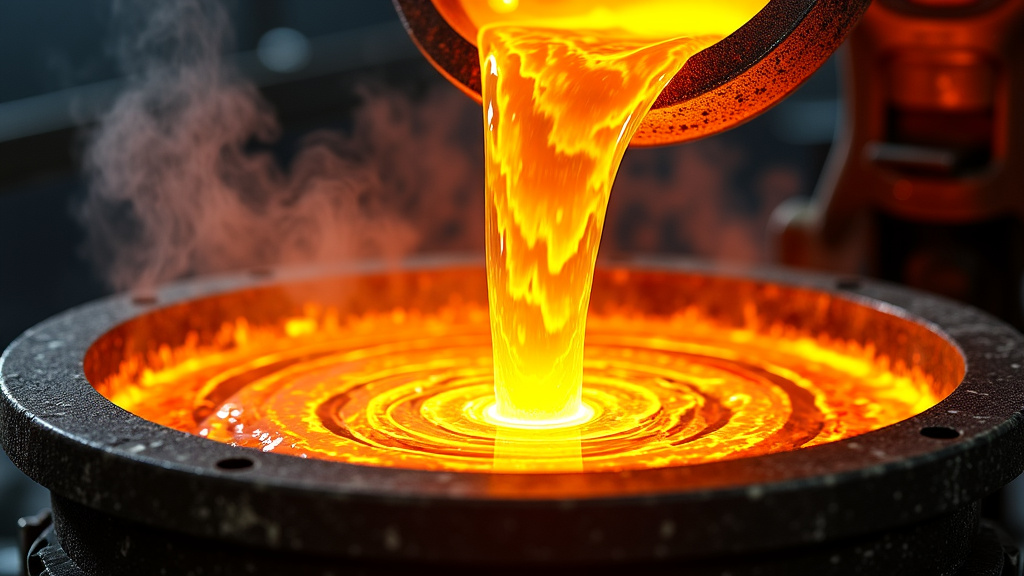
Alloys, often overlooked yet vital to modern life, are more than just metal mixtures. They are engineered to combine the strengths of different elements, creating materials with distinct properties. From the steel in skyscrapers to the aluminum in smartphones, alloys are essential, and their recyclability is key to a sustainable future.
Steel: The Recycling Champion
Steel, primarily composed of iron and carbon, is North America’s most recycled material. Its magnetic properties simplify separation from other waste, achieving an impressive recycling rate of over 60% annually since 1970.
The steel recycling process involves several key steps. After collection, steel scrap is sorted and sent to mills or foundries. Here, it is melted in furnaces reaching nearly 3,000 degrees Fahrenheit, purified to remove contaminants, and then solidified into sheets ready for reuse.
This process conserves natural resources and saves significant energy. Recycling steel uses about 75% less energy than producing it from raw materials, benefiting both the environment and the economy.
Aluminum Alloys: Lightweight Champions of Sustainability
Aluminum alloys, known for their lightweight and corrosion-resistant properties, are another recycling success. These alloys are widely used in beverage cans, foil, siding, and window frames, making them common in household recycling bins.
The recycling process for aluminum alloys is particularly efficient. Unlike steel, aluminum can be recycled indefinitely without losing its properties. The process involves melting down the aluminum, removing impurities, and then reshaping it into new products.
Recycling aluminum uses only about 5% of the energy required to produce new aluminum from bauxite ore. This energy efficiency and aluminum’s infinite recyclability make it a true champion of sustainable materials.
Brass and Bronze: Ancient Alloys, Modern Recycling
Brass, an alloy of copper and zinc, and bronze, typically made of copper and tin, have been used for millennia. Today, these alloys are found in musical instruments, plumbing fixtures, and decorative items, and they are highly recyclable.
The recycling process for brass and bronze is similar to other metals. They are collected, sorted, melted down, and purified before being recast into new products. These alloys are particularly valuable in the recycling stream due to their copper content, which is always in high demand.
Recycling brass and bronze conserves the metal and significantly reduces energy consumption and CO2 emissions compared to mining and processing new ore.
The Importance of Proper Sorting
While all these alloys are recyclable, effective recycling relies on proper sorting. Different alloys often require different recycling processes, and mixing them can reduce the quality of the recycled product.
As consumers, we can contribute to more efficient alloy recycling by learning to identify different metals and sorting them correctly. For instance, using a magnet can help separate ferrous metals like steel from non-ferrous ones like aluminum or brass.
By understanding the composition and recyclability of common alloys, we can all promote a more circular economy. So next time you are about to toss out that old brass doorknob or aluminum can, remember it is not just trash; it is a valuable resource waiting to be transformed into something new.
Metal | Energy Savings (%) |
---|---|
Aluminum | 95% |
Copper | 85% |
Steel | 60% |
Gold | 90% |
Benefits of Recycling Alloys
Recycling alloys is more than a trend—it’s transformative for both the environment and the economy. By giving these valuable materials a second life, we unlock benefits that extend beyond the recycling bin.
Consider the numbers: recycling aluminum, a common alloy, saves 95% of the energy required for primary production. This isn’t just a minor saving—it’s equivalent to powering millions of homes. But the benefits extend further.
Reducing Energy Consumption and Emissions
Recycling alloys significantly reduces energy-intensive processes. Industry experts report that steel recycling uses 56% less energy than producing steel from raw materials, leading to a substantial reduction in greenhouse gas emissions—a key step in combating climate change.
It’s not just steel. Copper recycling saves up to 85% of the energy needed for primary production, while recycled gold reduces energy use by 90%. These figures highlight the push for a more sustainable future.
For every ton of aluminum recycled, we prevent the emission of about 9 tons of CO2 equivalents, akin to taking two cars off the road for a year!
Preserving Natural Resources
Recycling alloys conserves our planet’s finite resources. Each piece of recycled metal means less ore extraction from the Earth.
Take copper, for instance. As accessible deposits dwindle, new mining operations become more invasive and environmentally harmful. Recycling copper alloys helps meet demand without damaging new landscapes or ecosystems.
Beyond preserving wilderness, recycling conserves water. Primary metal production requires significant water—recycling can reduce water usage by up to 40% compared to mining and refining virgin ores.
Reducing Landfill Waste
Alloy recycling is crucial in addressing our waste problem. Metals can be recycled indefinitely without losing properties, making them ideal for a circular economy.
By diverting alloys from landfills, we save space and prevent potential soil and groundwater contamination from metal leaching. Recycling one ton of steel prevents 1.5 tons of CO2 emissions and saves 1.4 tons of iron ore.
Moreover, recycling creates jobs. The U.S. recycling industry employs over 500,000 people, contributing billions to the economy while reducing our environmental footprint.
Economic Benefits
The advantages of alloy recycling extend beyond environmental concerns to significant economic benefits. Recycled materials are often cheaper than new ones, stabilizing prices and reducing production costs.
For businesses, this translates into improved competitiveness and profitability. A 2024 aerospace industry study found that a mid-sized manufacturer processing 500 tons of specialized alloys annually saved about $3.8 million through recycling initiatives.
As we aim for a sustainable future, the importance of recycling alloys is clear. It’s not just about being environmentally friendly—it’s about building a resilient, efficient, and prosperous economy for future generations. So next time you recycle a soda can, remember: you’re not just saving metal; you’re helping forge a better world.
The Alloy Recycling Process: From Scrap to New Products
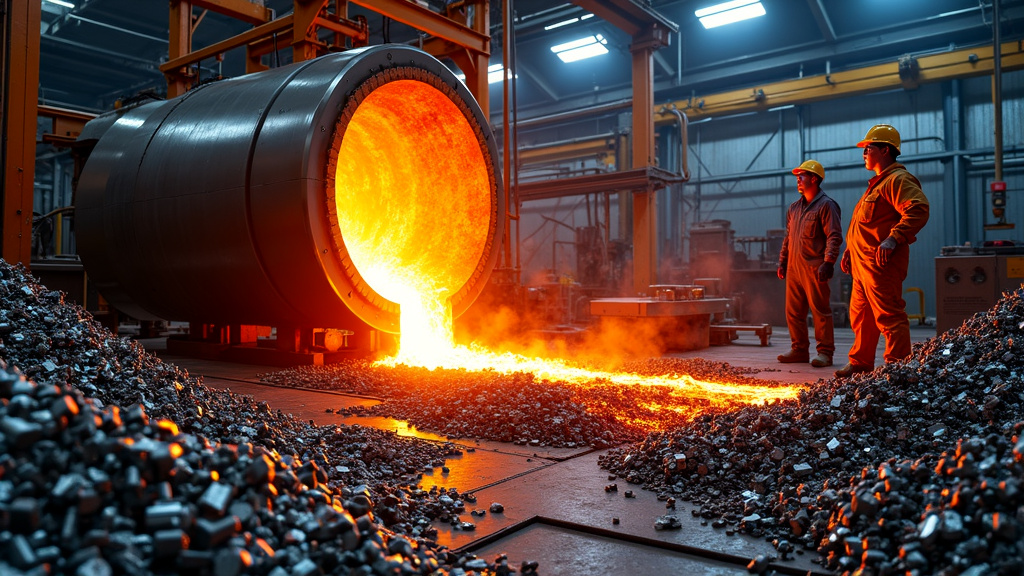
Recycling alloys is a crucial process that transforms discarded metal into valuable new materials. This journey involves several key stages, each playing a vital role in ensuring the final product meets strict quality standards. Here’s a breakdown of the alloy recycling process:
Collection: The First Step
The process begins with collecting metal scrap from various sources, including industrial byproducts and consumer goods at the end of their lifecycle. Efficient collection systems are essential for a steady supply of recyclable materials.
Many recycling facilities partner with businesses and municipalities to set up collection points, making it easier for people to dispose of their metal waste responsibly. Some even offer incentives to encourage participation in recycling programs.
The collected scrap often arrives mixed, containing different types of alloys and potentially other materials. This heterogeneity sets the stage for the crucial next step: sorting.
Sorting: Essential Separation
Proper sorting is perhaps the most critical stage in the alloy recycling process. Different types of metals and alloys are separated to maintain their unique properties and value. Advanced technologies play a key role in this step.
One such technology is X-ray fluorescence (XRF) analysis. This non-destructive technique allows recyclers to quickly identify the composition of different metal pieces. Specialized facilities often use XRF analyzers to sort alloys with precision, ensuring that high-value materials like titanium or nickel-based superalloys are properly identified and separated.
Magnetic separators quickly sort ferrous metals from non-ferrous ones. For more complex alloys, eddy current separators can distinguish between different non-ferrous metals based on their electrical conductivity.
Technology | Applications |
---|---|
Electrostatic Separation | Used in electronics recycling to separate conductive and non-conductive particles. |
Optical Sorting | Used in recycling to sort materials by color, shape, and composition; applied in food processing for sorting fruits and vegetables. |
Mechanical Separation | Includes screening, magnetic separation, and air classification to separate materials based on size, density, and magnetic properties. |
Eddy Current Separation | Used to recover non-ferrous metals like aluminum and copper by generating magnetic fields. |
Density Separation | Utilizes float-sink separation and hydrocyclones to separate materials based on density differences. |
Processing: Preparing for Melting
Once sorted, the alloys undergo various processing steps to prepare them for melting. This may involve shredding larger pieces into smaller, more manageable sizes or removing any non-metallic contaminants that could affect the final product’s quality.
Chemical treatments are sometimes used to remove surface coatings or oils that might interfere with the melting process. In some cases, alloys may undergo a preheating stage to remove moisture and reduce energy consumption during the actual melting.
The goal is to create a clean, uniform feedstock that can be efficiently melted and reformed into new products.
Melting: From Solid to Liquid
During the melting stage, the processed scrap is transformed back into a liquid state, typically in large furnaces designed for specific types of alloys. The choice of furnace and melting technique depends on the alloy being recycled and the desired properties of the final product.
For example, aluminum alloys might be melted in reverberatory furnaces, while more specialized alloys could require vacuum induction melting to maintain purity. During this stage, the molten metal’s composition is carefully monitored and adjusted to meet specific alloy standards.
Additives may be introduced to achieve the desired chemical composition, ensuring that the recycled alloy will have properties comparable to those made from virgin materials.
Reforming: Shaping New Products
The final stage in the alloy recycling process is reforming the molten metal into new products or shapes. This can involve casting the metal into ingots for further processing or directly shaping it into final products through techniques like extrusion or rolling.
Quality control is paramount at this stage. Samples of the recycled alloy are typically tested to ensure they meet industry standards for composition, strength, and other key properties. Organizations like ASTM International provide guidelines and standards for recycled alloys, helping to ensure consistency and reliability in the final products.
By adhering to these rigorous processes and quality standards, the alloy recycling industry produces high-quality materials for a wide range of applications, from aerospace components to everyday consumer goods. This not only conserves valuable resources but also significantly reduces the environmental impact of metal production.
Challenges in Alloy Recycling
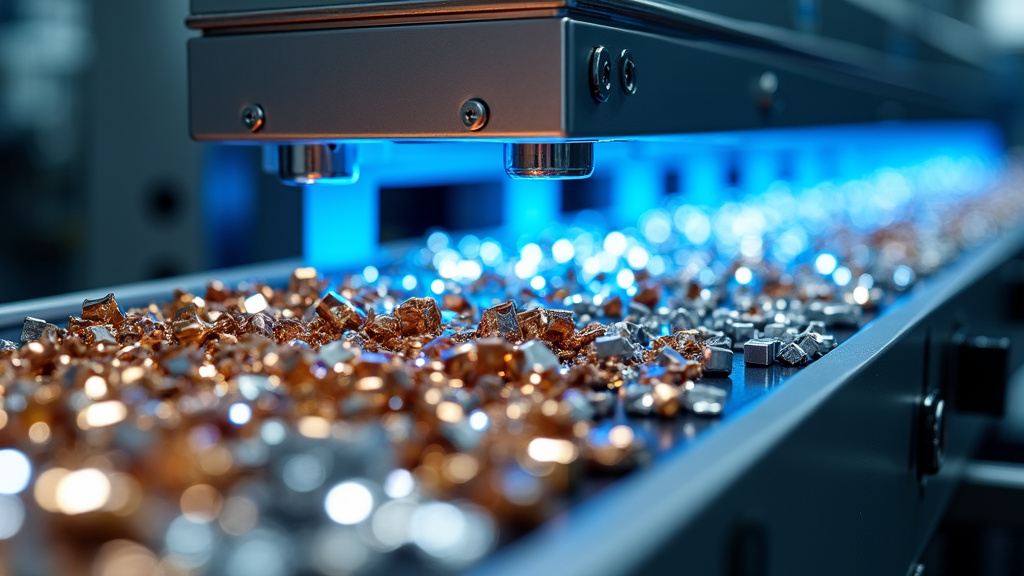
While alloy recycling offers many benefits, it faces several hurdles. The complexities of modern alloys present unique challenges that require innovative solutions and cutting-edge technologies to address. Let’s examine some key obstacles facing the alloy recycling industry today.
Contamination: The Nemesis of Quality Recycling
One of the most significant challenges in alloy recycling is contamination. Even trace amounts of foreign materials can compromise the integrity and performance of recycled alloys, potentially making them unsuitable for high-precision applications.
Common contaminants include other metals, coatings, paints, and oxides formed through chemical reactions. These impurities can alter the composition and properties of the recycled alloy, leading to subpar performance in its intended application.
To combat this issue, recycling facilities employ advanced cleaning and preprocessing methods. Techniques like mechanical grinding, chemical treatments, and thermal processes effectively remove surface contaminants and prepare alloys for high-quality recycling.
Separating Mixed Alloys: A Complex Puzzle
Another major challenge is separating mixed alloys, especially when dealing with scrap metal from various sources. Different alloys often have similar appearances, making visual sorting ineffective and increasing the risk of cross-contamination during the recycling process.
Fortunately, technological advancements are providing solutions to this complex puzzle. Specialized recycling facilities now utilize sophisticated equipment like spectrometers and X-ray fluorescence (XRF) analyzers to accurately identify and sort alloys based on their elemental composition.
These high-tech tools enable precise separation of alloys, ensuring that each type can be recycled appropriately and maintain its unique properties. As these technologies continue to evolve, the efficiency and accuracy of alloy separation are likely to improve further.
Maintaining Material Quality Through Multiple Recycling Cycles
Preserving the quality and performance of alloys through repeated recycling cycles presents another challenge. Each time an alloy is recycled, there’s a risk of degradation in its properties due to the accumulation of impurities or changes in its microstructure.
To address this, the industry is turning to advanced refining processes. Techniques such as vacuum induction melting (VIM) and electroslag remelting (ESR) are employed to purify alloys and maintain their high-performance characteristics even after multiple recycling cycles.
These methods not only help preserve the quality of recycled alloys but also contribute to the sustainability of the recycling process by extending the usable life of valuable materials.
The Role of Advanced Technologies in Overcoming Challenges
Advanced technologies play a crucial role in addressing the challenges of alloy recycling. From sophisticated sorting equipment to innovative refining processes, these technological solutions ensure that recycled alloys meet the stringent quality standards required for reuse in high-performance applications.
For instance, laser-induced breakdown spectroscopy (LIBS) is emerging as a powerful tool for rapid and accurate alloy identification. This technology allows for real-time analysis of metal composition, enabling more efficient sorting and processing of mixed alloy scrap.
Moreover, artificial intelligence and machine learning are being integrated into recycling systems to optimize processes and improve decision-making. These smart systems can analyze vast amounts of data to predict alloy compositions, identify potential contaminants, and fine-tune recycling parameters for maximum efficiency and quality.
The Future of Alloy Recycling: Challenges as Opportunities
While the challenges in alloy recycling are significant, they also present opportunities for innovation and growth in the industry. As demand for high-quality recycled alloys continues to rise, driven by sustainability initiatives and resource conservation efforts, there’s a strong incentive to develop even more advanced recycling technologies.
Research into new separation techniques, more efficient refining processes, and enhanced quality control methods is ongoing. These advancements promise to improve the quality and consistency of recycled alloys and make the recycling process more economically viable and environmentally friendly.
By viewing these challenges as opportunities for innovation, the alloy recycling industry is poised to play an increasingly vital role in the circular economy, conserving valuable resources and reducing the environmental impact of metal production.
How Okon Recycling Can Help with Recycling Alloys
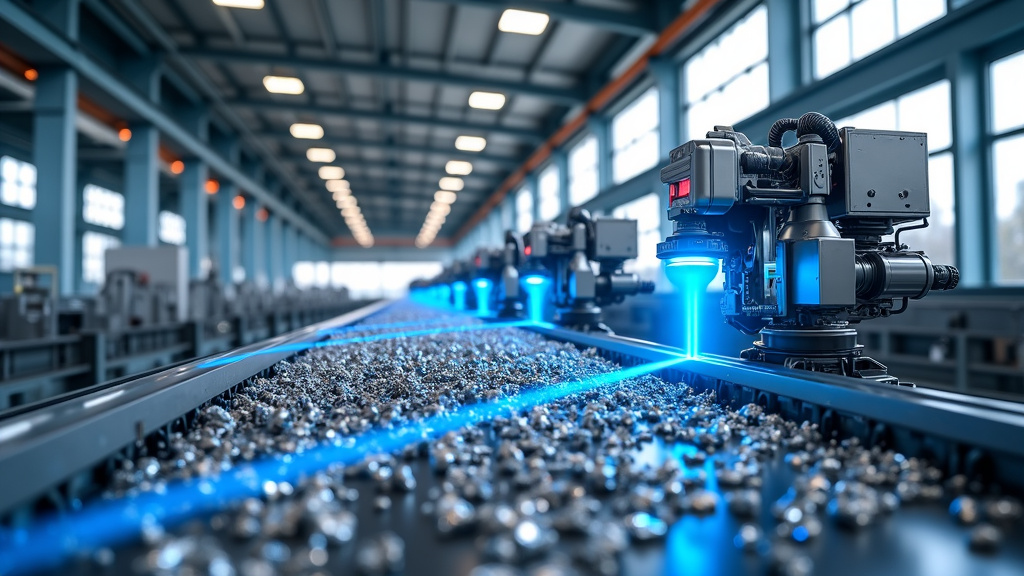
Okon Recycling is a leader in sustainable metallurgy, with over a century of experience in metal recycling. Based in Dallas, the company excels in tackling one of the industry’s most pressing challenges: efficient and sustainable alloy recycling.
Alloys, complex mixtures of metals designed for specific performance characteristics, present unique recycling challenges. Their varied compositions and the need for precise sorting make the recycling process complex. However, Okon Recycling’s state-of-the-art facilities and expert team have risen to meet these challenges head-on.
Advanced Technology for Precise Alloy Sorting
Okon Recycling’s alloy recycling process relies on advanced sorting technology. The company uses systems like X-ray transmission (XRT) and laser-induced breakdown spectroscopy (LIBS) to ensure accurate identification and separation of different alloy types.
This precision in sorting is crucial for maintaining the integrity and value of recycled alloys. By minimizing contamination and ensuring proper categorization, Okon Recycling can produce high-quality recycled materials that meet stringent industry standards.
The company’s investment in these technologies reflects its commitment to maximizing resource recovery while minimizing environmental impact. This approach benefits the environment and ensures that businesses partnering with Okon receive the highest value for their alloy waste.
Tailored Solutions for Business and Industry
Recognizing that each industry has unique alloy waste management needs, Okon Recycling offers customized recycling solutions. Whether in aerospace, automotive, or manufacturing, their team works closely with clients to develop a recycling program that fits specific requirements.
These tailored solutions might include on-site collection systems, specialized containers for different alloy types, or even on-site processing for large-scale operations. By adapting services to each client’s needs, Okon ensures efficient waste management and maximizes resource recovery potential.
Moreover, Okon’s expertise extends beyond collection and sorting. They provide valuable insights into optimizing processes to reduce alloy waste at the source, further enhancing sustainability efforts.
Sustainable Practices for a Greener Future
Okon Recycling’s commitment to sustainability goes beyond recycling. The company continually invests in research and development to improve processes and reduce its environmental footprint. This includes exploring new recycling technologies, optimizing energy use in facilities, and finding innovative ways to repurpose materials that might otherwise end up in landfills.
By choosing Okon for alloy recycling, businesses are not just managing their waste—they’re actively contributing to a more sustainable future. The company’s efforts help conserve valuable resources, reduce energy consumption associated with primary alloy production, and minimize the environmental impact of industrial operations.
Quality Control and Certification
Quality is paramount in alloy recycling, and Okon Recycling maintains rigorous quality control processes throughout operations. Their team of metallurgists and quality assurance specialists ensures that all recycled alloys meet or exceed industry standards.
Furthermore, Okon’s commitment to quality and sustainability is backed by relevant certifications. While specific certifications aren’t mentioned, leading recycling companies commonly hold certifications such as ISO 9001 for quality management and ISO 14001 for environmental management.
These certifications assure clients that Okon’s processes are effective and compliant with international standards for quality and environmental responsibility.
A Partner in Sustainable Alloy Management
Okon Recycling offers more than alloy recycling services—they provide a comprehensive solution for sustainable alloy waste management. With their century-long expertise, cutting-edge technology, and commitment to tailored solutions, Okon stands ready to help businesses transform their alloy waste into valuable resources.
By partnering with Okon Recycling, companies can ensure responsible management of their alloy waste and contribute to a more sustainable and circular economy in the metals industry. As we move towards a greener future, Okon Recycling is leading the way in turning the challenges of alloy recycling into opportunities for innovation and environmental stewardship.
The Future of Alloy Recycling: Innovations and Trends
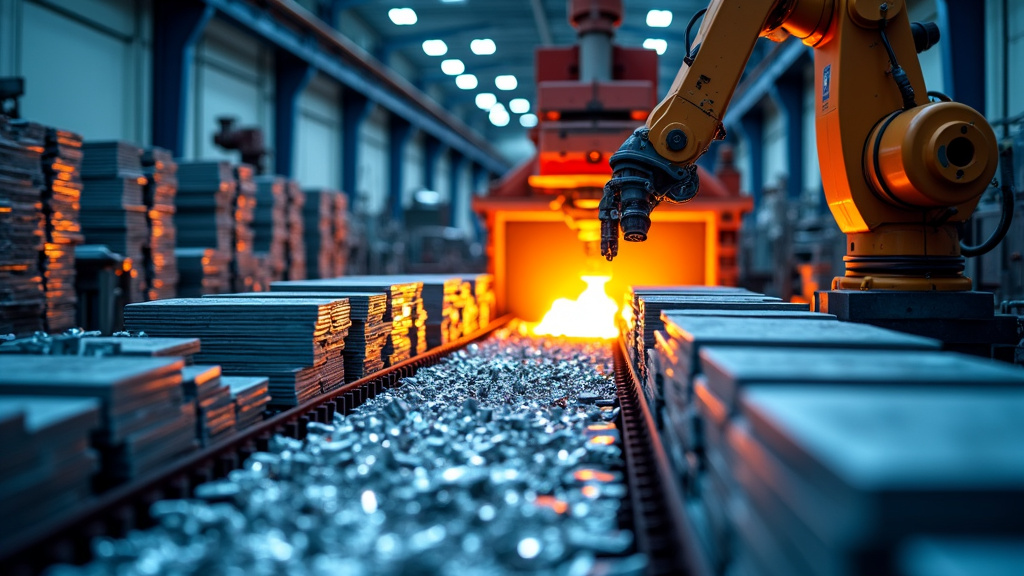
The latest developments in alloy recycling reveal an industry on the brink of transformation. Advanced sorting techniques, improved melting processes, and innovative alloy designs are paving the way for a more sustainable future in metal management. These solutions enhance recycling efficiency and reshape our approach to resource conservation and circular economy principles.
Staying informed about recycling innovations is crucial. As consumers and businesses, we all play a role in supporting sustainable practices. By choosing products made from recycled alloys or ensuring proper disposal of metal waste, we contribute to sustainable alloy management. Every action counts toward creating a more environmentally responsible industry.
Leading these trends is Okon Recycling, consistently adapting to and implementing the latest recycling technologies. Their commitment to innovation ensures they offer the most advanced and environmentally friendly recycling solutions available. Whether through state-of-the-art sorting systems or cutting-edge melting processes, Okon Recycling is dedicated to maximizing the potential of every piece of scrap metal.
If you’re interested in contributing to sustainable alloy management or have recycling needs, contact Okon Recycling at 214-717-4083. Their team of experts is ready to provide guidance and solutions tailored to your specific requirements.