5901 Botham Jean Blvd, Dallas, TX 75215
Understanding Oxide Dispersion Strengthening in Alloys
March 28, 2025Oxide dispersion strengthening (ODS) is an advanced metallurgical process that enhances the mechanical properties and high-temperature performance of metals. This technique involves dispersing fine oxide particles throughout a metal matrix, resulting in materials with superior strength, creep resistance, and thermal stability. But what makes ODS a significant advancement in metallurgy?
Imagine a metal that maintains its strength even when subjected to extreme temperatures—that’s the power of ODS. This process creates a ‘super metal’ by embedding tiny oxide particles within the metal’s structure. These particles act like microscopic reinforcements, improving the metal’s ability to withstand stress and high temperatures.
The applications of ODS are diverse and impressive. From high-performance turbine blades in jet engines to advanced nuclear reactors, ODS materials are pushing the boundaries of what’s possible in extreme environments.
But how does this process work, and why is it so effective? Let’s explore the fascinating world of oxide dispersion strengthening.
The Science Behind Oxide Dispersion Strengthening
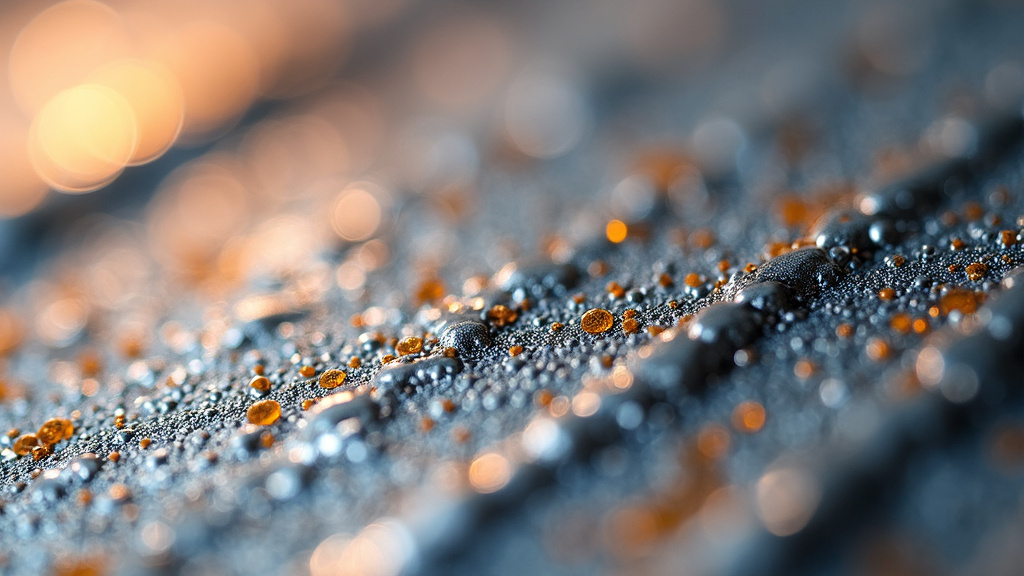
Imagine a bustling city where cars represent dislocations in a metal. Now, picture strategically placed roadblocks throughout this city; these are the oxide particles in oxide dispersion strengthening (ODS). Just as roadblocks impede traffic flow, these tiny oxide particles hinder the movement of dislocations within the metal matrix.
ODS works by introducing incredibly small oxide particles, often just nanometers in size, into the metal. These particles are uniformly dispersed throughout the material, creating a complex obstacle course for dislocations. When a dislocation encounters one of these oxide particles, it must either cut through it or bend around it, both of which require significant energy.
This interaction between dislocations and oxide particles is key to the strengthening effect. By making it harder for dislocations to move, the metal becomes more resistant to deformation and, consequently, stronger. It’s akin to how a gridlocked city with numerous roadblocks would be much harder to navigate than one with clear, open roads.
The benefits of ODS extend beyond room temperature. These oxide particles play a crucial role in maintaining the metal’s grain structure at high temperatures. In conventional metals, grains tend to grow and coarsen when exposed to heat, which can weaken the material. The dispersed oxide particles in ODS alloys act like anchors, pinning grain boundaries in place and resisting this unwanted growth.
This unique combination of strengthening and microstructural stability makes ODS materials particularly valuable for high-temperature applications. From jet engine components to nuclear reactor materials, ODS alloys can maintain their strength and integrity in environments where traditional metals would quickly fail.
The science of ODS showcases how manipulating materials at the nanoscale can lead to remarkable improvements in macroscale properties. By strategically introducing these tiny ‘roadblocks,’ engineers can create metals that are not only stronger but also more resilient in extreme conditions. As we continue to push the boundaries of material performance, ODS stands out as a shining example of how understanding and controlling microstructure can lead to extraordinary advancements in material science.
Property | ODS Alloys | Conventional Metals |
Temperature Capability | Up to 1200°C | Up to 1000°C |
Creep Strength | Comparable at 1000°C | Comparable at 800°C |
Lifespan in Extreme Conditions | 2-3 times longer | Standard |
Radiation Tolerance | Up to 200 dpa | Limited |
Applications of Oxide Dispersion Strengthened Materials
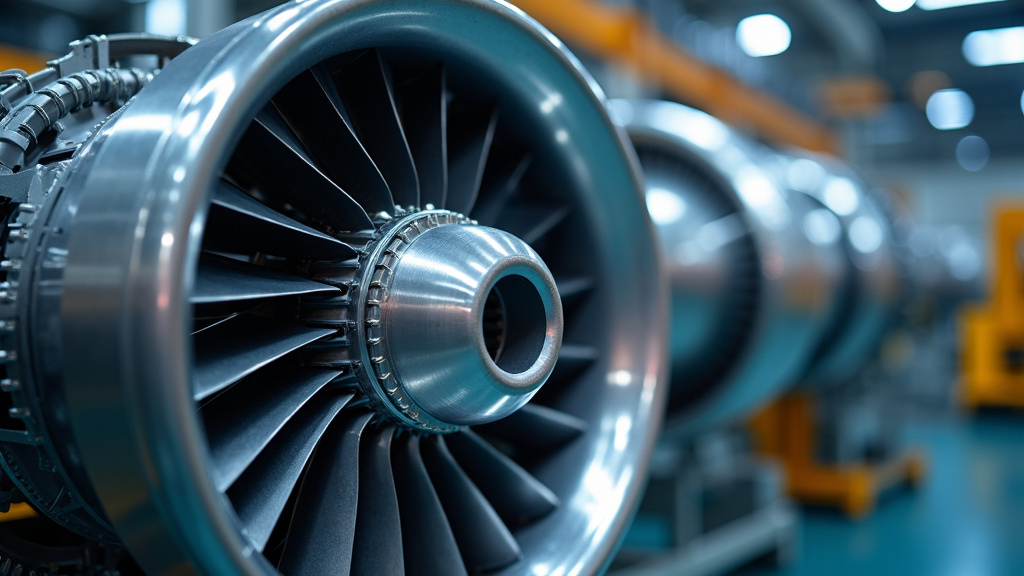
Oxide dispersion strengthened (ODS) materials have become crucial in industries facing extreme temperature challenges. Their ability to maintain strength and resist creep at high temperatures makes them essential in several high-stakes applications.
In aerospace, ODS alloys have transformed jet engine component design. These materials enable engines to operate at higher temperatures, enhancing fuel efficiency and performance. For example, turbine blades made from ODS nickel-based superalloys can withstand temperatures up to 1200°C, surpassing conventional alloys.
Nuclear reactors are another critical application for ODS materials. The harsh conditions inside a reactor, including intense heat and radiation, require materials with exceptional resilience. ODS steels, particularly ferritic and martensitic variants, show great promise as fuel cladding in advanced nuclear reactor designs due to their resistance to radiation-induced swelling and ability to maintain strength at high temperatures.
In power generation, ODS materials are advancing gas turbine technology. The pursuit of higher operating temperatures to improve efficiency has led engineers to adopt these advanced alloys. ODS components in turbine hot sections can endure harsh conditions, allowing for higher combustion temperatures and improved power output.
ODS materials are also being utilized in hypersonic flight, where vehicles must withstand extreme frictional heating, and in concentrated solar power systems, where materials must retain integrity under constant exposure to focused sunlight.
Real-World Impact
The impact of ODS materials goes beyond theoretical benefits. Practically, these materials enable longer component lifespans, reduced maintenance needs, and enhanced overall system performance. For instance, ODS alloy turbine blades in jet engines can operate for thousands of hours without replacement, reducing downtime and maintenance costs for airlines.
In the nuclear sector, ODS fuel cladding materials could allow for higher burnup rates and longer fuel cycles, improving the economics and efficiency of nuclear power plants. This could be crucial for next-generation reactor designs, including those aimed at producing hydrogen or desalinating water alongside electricity generation.
The versatility of ODS materials is also driving innovation in manufacturing techniques. Researchers are exploring advanced fabrication methods, including additive manufacturing, to create complex ODS components with optimized microstructures. This could open new design possibilities and further expand the applications of these remarkable materials.
As we explore the possibilities in high-temperature environments, ODS materials are at the forefront, enabling technologies once deemed impossible. From nuclear reactors to the edge of space, these materials are shaping the future of high-performance engineering.
Application | ODS Material | Benefits |
---|---|---|
Aerospace (Jet Engines) | Nickel-based ODS superalloys | Withstands temperatures up to 1200°C, improves fuel efficiency and performance |
Nuclear Reactors | ODS steels (ferritic and martensitic) | Resists radiation-induced swelling, maintains strength at high temperatures |
Gas Turbines | ODS components | Endures high combustion temperatures, improves power output |
Hypersonic Flight | ODS materials | Withstands extreme frictional heating |
Concentrated Solar Power Systems | ODS materials | Maintains integrity under constant exposure to focused sunlight |
Advantages of Oxide Dispersion Strengthening
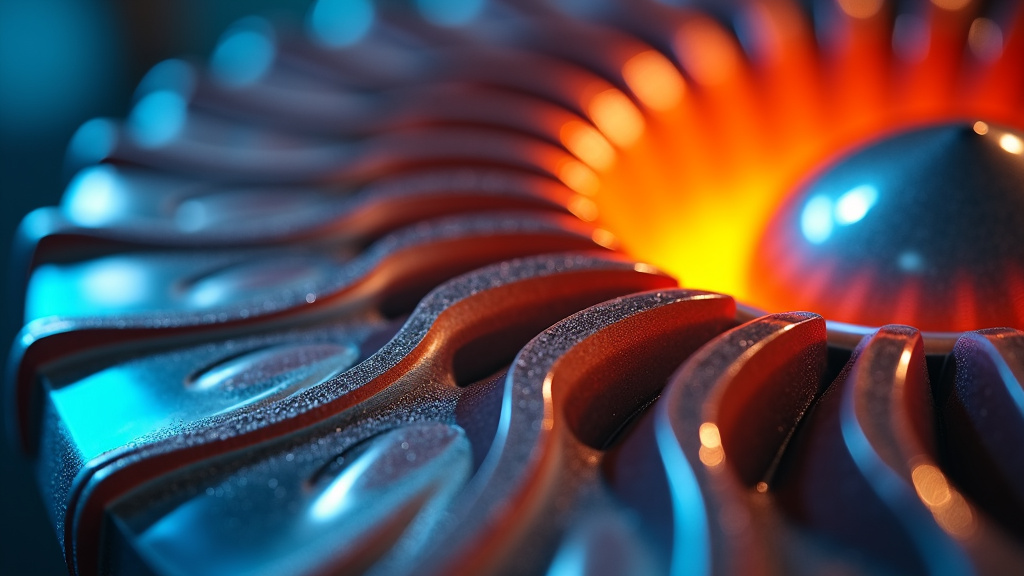
Oxide dispersion strengthened (ODS) alloys represent a major advancement in materials science, offering superior performance in extreme environments compared to conventional alloys. These materials are engineered to withstand harsh conditions that would cause most metals to fail, making them invaluable in industries like aerospace, nuclear power, and advanced energy systems.
The primary benefits of ODS alloys stem from their unique microstructure, which consists of a metal matrix reinforced with nanoscale oxide particles. This combination yields several key advantages:
Enhanced High-Temperature Strength
ODS alloys exhibit remarkable strength retention at elevated temperatures, far surpassing traditional materials. For example, while conventional superalloys may begin to lose structural integrity around 1000°C, some ODS materials can maintain their strength up to 1200°C and beyond. This exceptional high-temperature performance is critical for components in gas turbines, jet engines, and other high-heat applications.
Superior Creep Resistance
One of the most significant advantages of ODS alloys is their outstanding creep resistance. Creep, the tendency of materials to slowly deform under constant stress, is a major concern in high-temperature applications. ODS materials can resist creep deformation for extended periods, even under extreme conditions. For instance, studies have shown that ODS steels can maintain their creep strength at temperatures 100-150°C higher than conventional creep-resistant steels.
Increased Thermal Stability
The dispersed oxide particles in ODS alloys act as powerful stabilizers, preventing grain growth and maintaining the material’s microstructure even at high temperatures. This thermal stability ensures that the alloy’s properties remain consistent over long periods of use, a crucial factor in applications where reliability and longevity are paramount.
Enhanced Radiation Resistance
In nuclear applications, materials must withstand not only high temperatures but also intense radiation exposure. ODS alloys have demonstrated superior radiation resistance compared to conventional materials. The dispersed oxide particles serve as traps for radiation-induced defects, helping to maintain the alloy’s structural integrity in radioactive environments.
To illustrate the advantages of ODS materials over traditional alloys, consider the following comparison:
Property | ODS Alloys | Traditional Alloys |
Temperature Capability | 100-200°C higher | Lower |
Creep Strength at 1000°C | Comparable to conventional alloys at 800°C | Lower |
Lifespan in Extreme Conditions | 2-3 times longer | Shorter |
Radiation Tolerance | Up to 200 dpa | Lower |
- Temperature Capability: ODS alloys can operate at temperatures 100-200°C higher than conventional high-temperature alloys.
- Creep Strength: At 1000°C, some ODS alloys retain creep strength comparable to conventional alloys at 800°C.
- Lifespan in Extreme Conditions: ODS materials can extend component life by 2-3 times in high-temperature, high-stress environments.
- Radiation Tolerance: ODS steels have shown the ability to withstand neutron doses up to 200 displacements per atom (dpa), far exceeding the limits of conventional steels.
These remarkable properties make ODS alloys indispensable in cutting-edge applications where conventional materials simply cannot meet the demanding requirements. As research continues, the potential for ODS materials to enable new technologies and push the boundaries of material performance remains highly promising.
For more detailed information on the performance of specific ODS alloys, interested readers can refer to the comprehensive studies published in journals such as the Journal of Nuclear Materials, which provide in-depth analyses of creep behavior and high-temperature properties of various ODS compositions.
How Okon Recycling Can Help with Oxide Dispersion Strengthening
While Okon Recycling may not directly manufacture oxide dispersion strengthened (ODS) materials, our expertise in metal recycling plays a crucial role in the sustainable lifecycle management of these advanced alloys. Known for their exceptional strength and heat resistance, ODS materials require specialized handling during recycling to maintain their valuable properties.
Okon Recycling’s advanced sorting and processing techniques ensure that ODS materials are properly identified and separated from other metal waste streams. This precision is essential, as the unique composition of ODS alloys—with their dispersed oxide particles—demands careful recycling to preserve their high-performance characteristics.
By partnering with ODS material manufacturers, Okon Recycling contributes to closing the loop in the production cycle of these advanced metals. Our state-of-the-art facilities are equipped to handle the complexities of recycling ODS materials, ensuring that valuable components are recovered and reintegrated into new production processes.
This specialized recycling approach not only reduces the environmental impact associated with ODS material production but also helps conserve the rare and expensive elements often used in these alloys. By reclaiming these materials, we decrease the need for raw resource extraction, aligning with broader sustainability goals in the metals industry.
Okon Recycling’s commitment to sustainable metal management extends beyond just ODS materials. Our comprehensive recycling services cover a wide range of metals, from common alloys to specialized high-performance materials. This holistic approach ensures that all metal waste is handled responsibly, maximizing resource efficiency across the entire metals sector.
Conclusion: Powering the Future with ODS and Sustainable Recycling
Oxide dispersion strengthening represents a breakthrough in materials science, enabling metals to perform reliably in the most extreme environments—whether in jet engines, nuclear reactors, or next-generation power systems. With unmatched strength, creep resistance, and thermal stability, ODS alloys are shaping the future of high-performance engineering.
But innovation must go hand in hand with sustainability. That’s where Okon Recycling plays a crucial role—extending the lifecycle of these advanced materials through precision recycling practices that conserve valuable resources and reduce environmental impact.
Together, ODS technology and responsible recycling create a powerful synergy. As industries demand materials that can withstand more while wasting less, this partnership ensures we not only build a stronger future—but a greener one too.
To learn more about oxide dispersion strengthening, contact Okon Recycling at 214-717-4083.