5901 Botham Jean Blvd, Dallas, TX 75215
Understanding Interstitial and Substitutional Alloys in Metal Recycling
April 5, 2025What are interstitial and substitutional alloys, and how do they differ? Interstitial alloys, such as carbon-infused iron that forms steel, involve smaller atoms fitting into the spaces between larger metal atoms.
Conversely, substitutional alloys, like brass (a mixture of copper and zinc), consist of similar-sized atoms swapping places in the crystal structure. These atomic-level differences result in varied material properties, each with its own recycling challenges and opportunities.
As we explore interstitial and substitutional alloys further, we’ll see how these microscopic arrangements significantly impact metal recycling.
Defining Interstitial and Substitutional Alloys
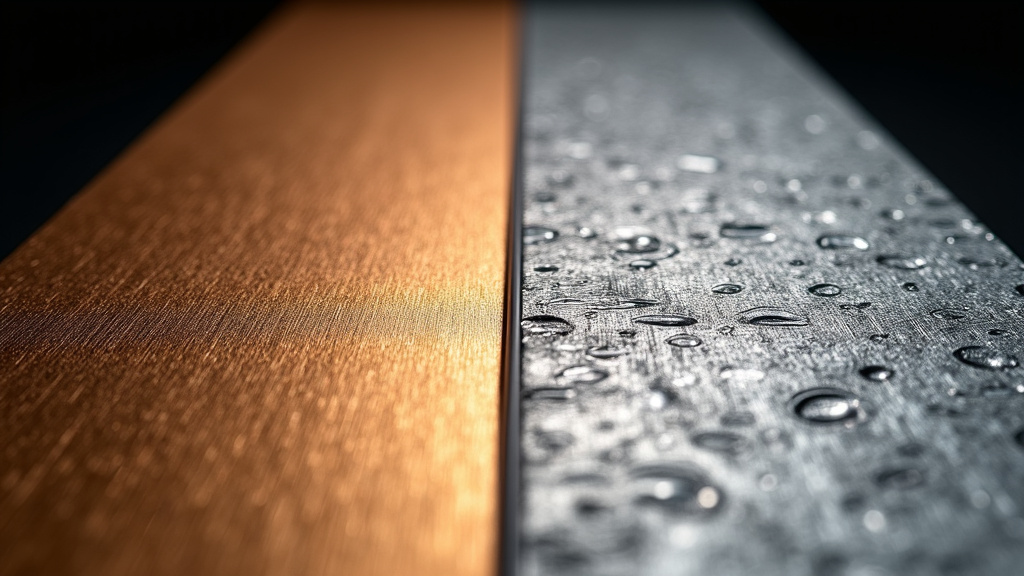
Alloys are essential in metallurgy for creating materials with improved properties. Two main types – interstitial and substitutional – form the basis of many materials we use daily. Here, we explore what differentiates these alloys and how their structures affect their characteristics.
Interstitial Alloys: The Space Fillers
Imagine a basket filled with large oranges and small marbles fitting into the spaces between them. This illustrates interstitial alloys, where smaller atoms fit into the gaps within a metal’s crystal structure.
Steel, a common interstitial alloy, has iron atoms (the oranges) and smaller carbon atoms (the marbles) filling the spaces between them. This arrangement changes the base metal’s properties. Research shows these microscopic arrangements determine the alloy’s physical properties.
Interstitial alloys are typically harder and stronger than pure metals, though they may be less malleable and ductile due to the smaller atoms restricting movement.
Substitutional Alloys: The Atom Swappers
Consider a chessboard where some white pieces are replaced with black ones. This represents substitutional alloys, where atoms of one element replace another in the crystal lattice.
Bronze, a substitutional alloy, forms when tin atoms replace some copper atoms. Tin and copper atoms have similar sizes, allowing easy substitution without greatly distorting the structure.
Substitutional alloys often retain the base metal’s malleability and ductility and can be tailored for properties like corrosion resistance or conductivity.
Impact on Recycling Processes
The structures of interstitial and substitutional alloys affect recycling. Tightly bound atoms in interstitial alloys complicate separation, while similar-sized atoms in substitutional alloys may be easier to separate, though maintaining desired ratios is crucial.
Understanding these structures is vital for developing efficient recycling methods. Researchers are innovating techniques, such as using magnetic fields and temperature gradients, to improve alloy recycling and maintain material quality.
As material science advances, the intricate atomic arrangements in these alloys will continue to be key in creating stronger, versatile, and recyclable materials for the future.
Impact of Alloy Types on Recycling Processes
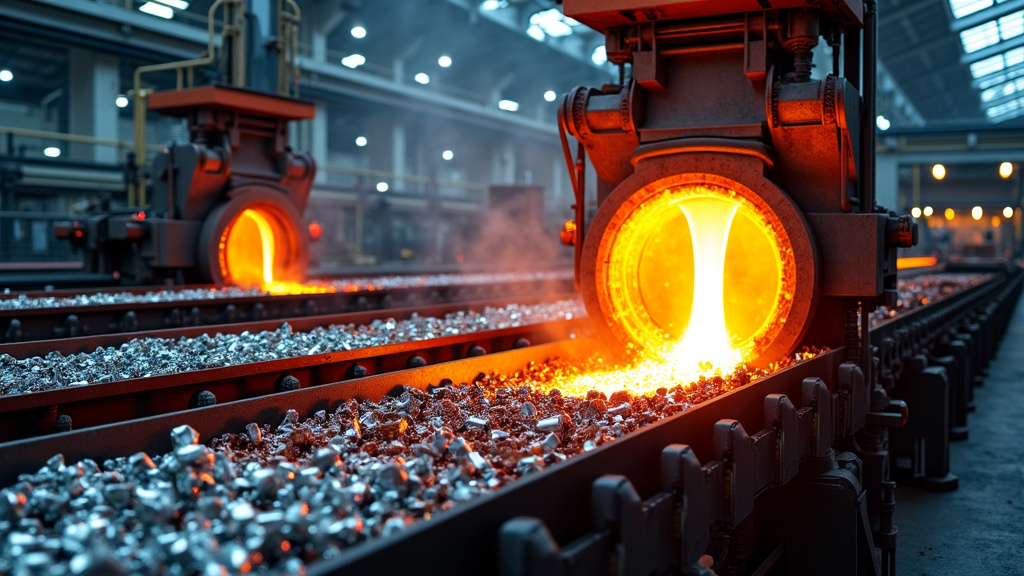
The realm of metal recycling involves more than just melting old cans and casting them into new products. Different alloy compositions significantly influence the most effective recycling methods. Here, we explore how the distinct properties of interstitial and substitutional alloys affect the recycling process, from sorting to purification.
Understanding Alloy Compositions
Alloys are combinations of metals or metals with other elements. We focus on interstitial and substitutional alloys, each with unique characteristics impacting recycling.
Interstitial alloys, like steel, have smaller atoms (often non-metals) positioned between larger metal atoms, affecting the alloy’s strength and melting point. For example, carbon atoms in steel enhance hardness but complicate recycling.
Substitutional alloys, such as brass (copper and zinc), consist of atoms of similar sizes replacing each other in the crystal structure. These alloys often exhibit more predictable properties, simplifying certain recycling aspects.
The compositions of these alloys directly impact their melting points, strength, and chemical reactivity—critical factors in recycling.
Sorting: The First Step in Alloy Recycling
Effective sorting is essential in alloy recycling. Modern facilities use advanced technologies to separate alloy types. X-ray fluorescence (XRF) analyzers quickly identify metal scrap compositions, enabling precise alloy sorting.
Magnetic separation is useful for sorting ferrous (iron-containing) alloys from non-ferrous ones. However, some alloys, like certain stainless steels, may be only weakly magnetic, requiring more sophisticated methods.
Eddy current separators use magnetic fields to separate non-ferrous metals based on conductivity, particularly useful for sorting aluminum alloys from other non-magnetic metals.
Melting: Dealing with Diverse Melting Points
The melting phase highlights differences in alloy compositions. Interstitial alloys, like steel, often have higher melting points due to strong atomic bonds, requiring more energy during recycling.
Substitutional alloys may have lower and varied melting points. For example, some aluminum alloys in beverage cans melt at around 660°C, while high-strength aluminum alloys for aerospace may require over 750°C.
Recycling facilities must carefully control furnace temperatures to ensure complete melting without excessive energy use or potential damage to the alloy’s properties, crucial for maintaining recycled metal quality.
Purification: Removing Impurities and Adjusting Composition
Purification involves specific processes to remove impurities and adjust final compositions. For example, recycling aluminum often uses chlorine gas to remove magnesium, a common alloying element that affects recycled metal properties if not controlled.
In steel recycling, the basic oxygen furnace process removes excess carbon and impurities by blowing oxygen through molten steel, oxidizing unwanted elements that form easily removable slag.
For complex alloys, especially in high-performance applications, advanced refining techniques like vacuum arc remelting may be necessary to achieve required purity levels.
Developing Efficient Recycling Strategies
Understanding different alloy properties is crucial for efficient recycling strategies. Knowing that certain aluminum alloys are more susceptible to contamination has led to developing ‘recycling-friendly’ alloys with broader compositional tolerances.
Innovative approaches, like designing alloys specifically for recycling ease, are gaining traction. These alloys maintain desirable properties while being more amenable to recycling, reducing energy consumption and improving recycled materials’ quality.
The future of alloy recycling lies in continued technological advancements and a deeper understanding of alloy properties. From improved sorting technologies to more efficient melting and purification processes, the goal is to make metal recycling more economical and environmentally friendly.
How Okon Recycling Can Help with Interstitial and Substitutional Alloys
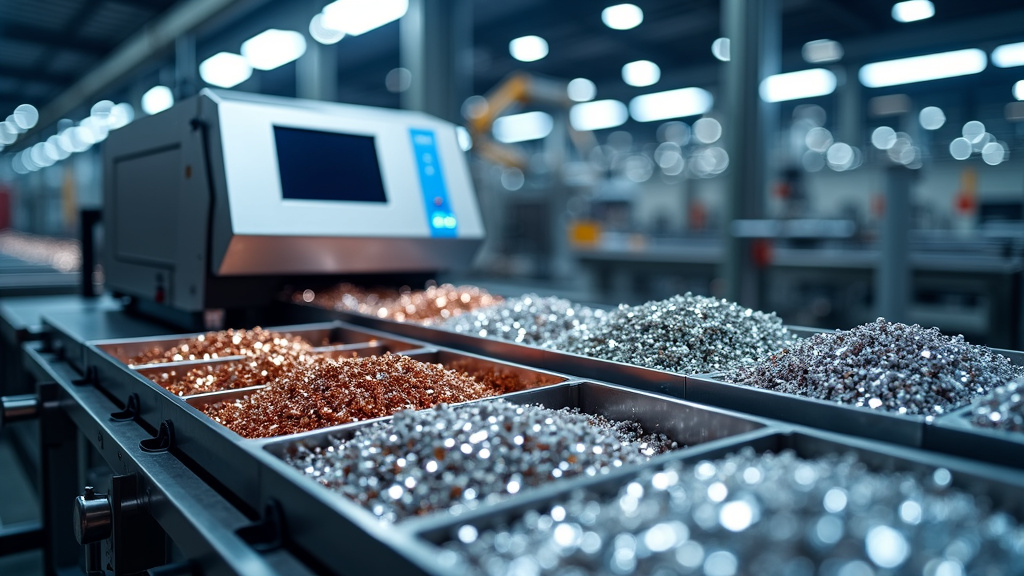
Recycling interstitial and substitutional alloys presents unique challenges that require specialized expertise and cutting-edge technology. Okon Recycling, with its century-long legacy in the industry, leads in addressing these complexities. Our approach combines time-tested knowledge with innovative solutions to tackle the intricate nature of alloy recycling.
Interstitial alloys, characterized by smaller atoms fitting into spaces between larger atoms in the crystal lattice, and substitutional alloys, where atoms of similar size replace each other, need distinct recycling methods. Okon Recycling’s state-of-the-art facilities are equipped with advanced sorting technologies that differentiate between these alloy types with remarkable precision.
One of the key technologies used by Okon is X-ray fluorescence (XRF) spectroscopy, allowing rapid and accurate identification of alloy compositions. This non-destructive technique enables our team to sort various alloys efficiently, ensuring optimal recovery rates while maintaining the integrity of valuable materials.
The Future of Alloy Recycling: Innovations and Opportunities
Looking ahead, the future of alloy recycling is full of potential. As technologies evolve, we can anticipate more sophisticated sorting systems, more efficient chemical processes, and potentially, entirely new methods of alloy recovery.
These innovations will not only improve recycling efficiency but also contribute to the broader goal of creating a circular economy in the metals industry.
The recycling of interstitial and substitutional alloys is entering an exciting new phase, driven by technological innovation and a growing commitment to sustainability. By embracing these advancements and partnering with expert recyclers, businesses can play a crucial role in shaping a more sustainable future for metal management.
To explore how your company can benefit from these advanced recycling solutions and contribute to a circular economy, contact Okon Recycling at 214-717-4083. Together, we can turn today’s alloy waste into tomorrow’s valuable resources.