5901 Botham Jean Blvd, Dallas, TX 75215
How Alloys Revolutionized the Automotive and Aerospace Industries
March 27, 2025Did you know that modern aircraft engines can operate at temperatures exceeding 1,300°C (2,372°F) without losing structural integrity? This achievement is possible due to advanced metal alloys that have transformed the automotive and aerospace industries, ushering in a period of remarkable performance and efficiency.
Alloys, materials formed by combining two or more metallic elements, have fundamentally changed transportation technology. These engineered materials have enabled the creation of lighter, stronger, and more durable components, pushing the limits of what is possible in vehicles and aircraft.
In the automotive sector, high-strength aluminum alloys have reduced vehicle weights by up to 40%, significantly improving fuel efficiency without compromising safety. In aerospace, nickel-based superalloys withstand extreme temperatures in jet engines, allowing for higher thrust and improved fuel economy once thought impossible.
The impact of these innovations goes beyond performance metrics. By enabling more efficient vehicles and aircraft, alloys play a crucial role in reducing carbon emissions and advancing sustainability goals across the transportation industry.
The Evolution of Alloys in Automotive Engineering

The automotive industry has seen significant transformation in recent decades, driven by the pursuit of improved performance, fuel efficiency, and safety. Central to this evolution is the innovative use of advanced alloys, which have revolutionized vehicle design and manufacturing processes. The shift from traditional steel to advanced aluminum and magnesium alloys marks an important chapter in automotive engineering.
Transition to Lightweight Alloys
Throughout much of the 20th century, steel was the dominant material in automotive construction due to its strength, durability, and cost-effectiveness. However, as fuel efficiency standards tightened and consumer demand for high-performing vehicles grew, automakers sought alternatives.
Aluminum alloys became pivotal in the 1990s, offering substantial weight reduction compared to steel while maintaining structural integrity. For example, using aluminum alloys in vehicle bodies can reduce weight by up to 40%, directly enhancing fuel economy and reducing emissions.
The introduction of magnesium alloys expanded possibilities for lightweight vehicle design further. Magnesium, lighter than aluminum, enabled automakers to explore new weight reduction boundaries. With a density about 33% lighter than aluminum and 75% lighter than steel, magnesium alloys quickly found applications in various automotive components.
Boosting Fuel Efficiency and Performance
The use of lightweight alloys has significantly improved vehicle fuel efficiency. Industry studies show that a 10% reduction in vehicle weight can lead to a 6-8% improvement in fuel economy. This relationship has driven automakers to increasingly incorporate aluminum and magnesium alloys into their designs.
For instance, the Ford F-150, America’s best-selling pickup truck, gained attention in 2015 by adopting an aluminum-intensive body. This led to a weight reduction of up to 700 pounds, significantly enhancing fuel efficiency without compromising the truck’s renowned toughness. Similarly, luxury brands like Audi and Jaguar have extensively used aluminum in their vehicle designs to boost performance and efficiency.
Advancements in Vehicle Safety
Contrary to initial concerns, lighter alloys have not compromised safety. In fact, advanced aluminum and magnesium alloys have enabled engineers to design vehicles with superior crash protection capabilities. These materials can absorb more energy during collisions than traditional steel structures, helping to protect occupants.
Modern alloys also facilitate the creation of sophisticated crumple zones and reinforced passenger compartments. The Audi A8, for example, uses a multi-material space frame that combines aluminum, steel, magnesium, and carbon fiber-reinforced polymers to optimize both weight and safety performance.
Impact on Manufacturing Processes
The adoption of advanced alloys has led to significant changes in automotive manufacturing processes. Traditional steel stamping and welding have been supplemented or replaced by techniques tailored to aluminum and magnesium alloys.
Automakers have invested in technologies like self-piercing rivets, flow-drill screws, and advanced adhesives to effectively join lightweight materials. These methods not only accommodate advanced alloys’ unique properties but also enhance structural rigidity and corrosion resistance.
The shift has also driven innovation in casting and forming processes. High-pressure die casting of aluminum and magnesium components has become increasingly sophisticated, enabling the production of complex, thin-walled parts that contribute to weight reduction and design flexibility.
Aerospace Advancements: Alloys Taking Flight
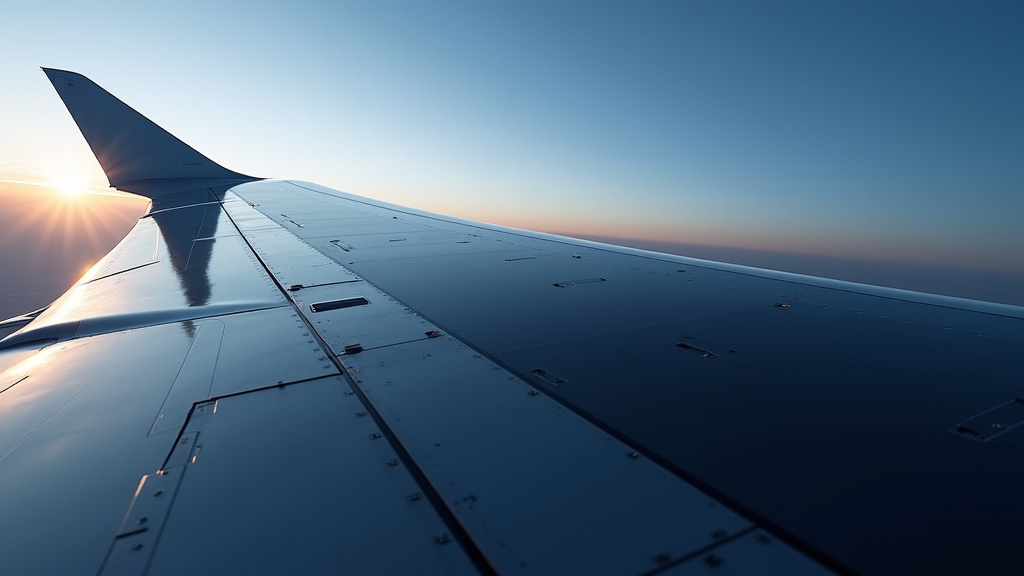
The aerospace industry has transformed significantly in recent years, largely due to innovations in specialized alloys. These advanced materials have changed aircraft design, enabling the development of faster, more durable, and fuel-efficient planes that push the boundaries of flight. This article explores how titanium alloys, superalloys, and composite materials are reshaping modern aerospace engineering.
Titanium Alloys: Lightweight Champions
Titanium alloys are essential in aerospace engineering, valued for their exceptional strength-to-weight ratio. These materials offer a unique combination of high strength, low density, and excellent corrosion resistance, making them ideal for critical aircraft components.
One of the most widely used titanium alloys in aerospace is Ti-6Al-4V. This versatile material provides an outstanding balance of high strength, toughness, and resistance to fatigue and corrosion. It is commonly found in airframe structures, engine components, and landing gear systems.
A prime example of titanium’s impact is the development of the Boeing 787 Dreamliner. This aircraft extensively utilizes titanium alloys, contributing to its lightweight design and improved fuel efficiency. The use of titanium has allowed Boeing to create a more aerodynamic and cost-effective aircraft, setting new standards in commercial aviation.
Superalloys: Masters of Extreme Conditions
For withstanding extreme temperatures and pressures, superalloys are unmatched. These advanced materials, primarily based on nickel, cobalt, or iron, exhibit exceptional strength and corrosion resistance at high temperatures, making them crucial for jet engine components.
Inconel, a family of nickel-chromium-based superalloys, is indispensable in modern jet engines. These materials maintain their mechanical properties even at temperatures near their melting points, allowing engines to operate at higher temperatures and achieve greater efficiency.
The development of single-crystal superalloys has transformed turbine blade design. These materials, with their controlled microstructure, offer superior creep resistance and thermal stability. This innovation has enabled the creation of more powerful and efficient jet engines, advancing both commercial and military aviation.
Composite Materials: The Future of Aerospace
While metals continue to play a crucial role, composite materials are increasingly prominent in aerospace design. These engineered materials, typically combining strong fibers with a polymer matrix, offer unparalleled strength-to-weight ratios and design flexibility.
Carbon fiber reinforced polymers (CFRPs) have become particularly prominent in modern aircraft construction. These materials provide exceptional strength and stiffness while weighing significantly less than traditional metals. The Airbus A350 XWB showcases the potential of composites, with over 50% of its structure made from CFRPs.
Advanced composites are not limited to structural applications. Ceramic matrix composites (CMCs) are transforming jet engine design by allowing components to withstand temperatures exceeding 1,300°C (2,372°F). This remarkable heat resistance enables engines to operate at higher temperatures, significantly improving fuel efficiency and reducing emissions.
Pushing the Boundaries: Hypersonic Flight
The quest for hypersonic flight, traveling at speeds above Mach 5, is driving the development of even more advanced aerospace materials. Researchers are exploring novel alloys and composites capable of withstanding the extreme temperatures and stresses associated with hypersonic travel.
One promising area of research is the development of high-entropy alloys (HEAs). These materials, composed of five or more principal elements in near-equal proportions, offer a unique combination of strength, ductility, and thermal stability. HEAs have the potential to revolutionize hypersonic vehicle design, enabling aircraft to reach unprecedented speeds and altitudes.
Looking to the future, the continued advancement of aerospace alloys and composites will play a pivotal role in shaping the next generation of aircraft. From more efficient commercial airliners to cutting-edge military platforms, these materials are helping redefine possibilities in flight. Ongoing collaboration between materials scientists, aerospace engineers, and industry leaders promises even more exciting innovations in the years to come.
Future Prospects: Emerging Alloys and Their Potential
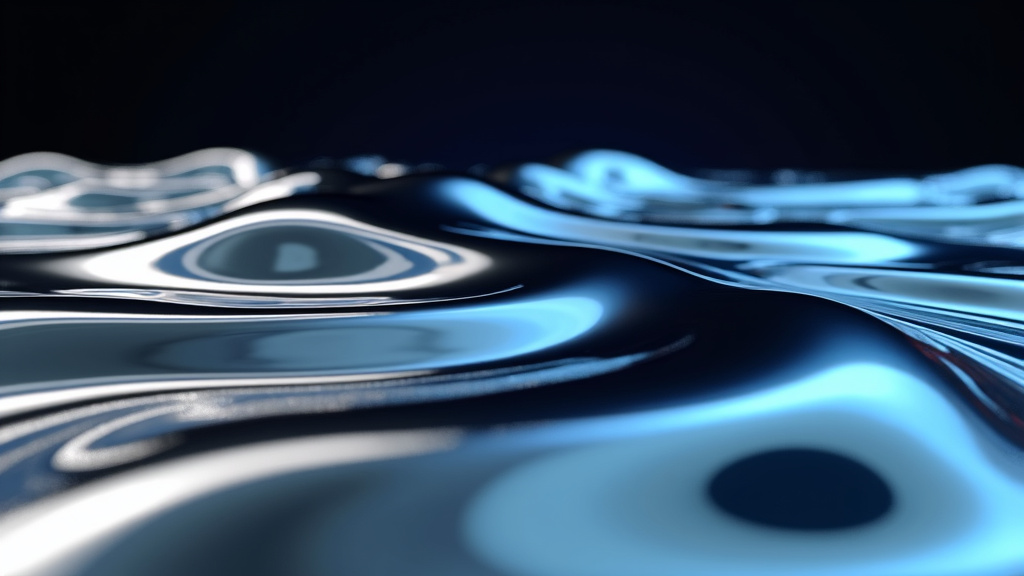
Looking ahead in materials science, two groundbreaking alloy technologies are set to transform the automotive and aerospace industries: shape memory alloys (SMAs) and high-entropy alloys (HEAs). These innovative materials promise to expand the limits of design, performance, and sustainability in unprecedented ways.
Shape Memory Alloys: Transforming Vehicle Design
SMAs are materials that can “remember” and return to their original shape when heated. This unique property presents numerous possibilities for automotive and aerospace applications. Imagine car bodies that can self-repair minor dents or aircraft wings that can change shape mid-flight to optimize aerodynamics.
In the automotive sector, SMAs are already making an impact. Engineers are exploring SMA-based actuators that could replace traditional hydraulic or electric systems, leading to lighter, more efficient vehicles. These materials could enable innovative designs for everything from engine valves to adaptive suspension systems, potentially transforming car performance and fuel efficiency.
For aerospace applications, the potential of SMAs is equally exciting. Researchers are developing SMA-based morphing wings that can adjust their shape in real-time, optimizing performance across different flight conditions. This technology could lead to aircraft that are more fuel-efficient and capable of operating in a wider range of environments.
High-Entropy Alloys: A New Frontier in Material Design
While SMAs push the boundaries of material behavior, HEAs are redefining alloy composition. These materials, composed of five or more elements in near-equal proportions, exhibit exceptional strength, hardness, and resistance to wear and corrosion.
The automotive industry is considering HEAs for their potential to create lighter, stronger vehicle components. Researchers are exploring HEAs for applications in engine parts, where their high-temperature stability and wear resistance could significantly extend component lifespans and improve engine efficiency.
In aerospace, HEAs offer the exciting prospect of materials that can withstand the extreme conditions of hypersonic flight. Their unique properties could enable the development of aircraft capable of speeds and altitudes previously thought unattainable, potentially transforming both military and civilian aviation.
The Sustainability Angle
Both SMAs and HEAs have the potential to significantly contribute to sustainability efforts in the automotive and aerospace sectors. By enabling lighter, more efficient vehicles and aircraft, these materials could play a crucial role in reducing fuel consumption and emissions.
Moreover, the durability of HEAs could lead to longer-lasting components, reducing the need for frequent replacements and minimizing waste. SMAs, with their potential for self-repair and adaptive capabilities, could further extend the lifespan of vehicles and aircraft, making them more sustainable over the long term.
As research into these innovative alloys continues, we stand on the brink of a new era in materials science. The future of automotive and aerospace design looks set to be shaped by these remarkable materials, promising vehicles and aircraft that are not just faster and more efficient, but also more sustainable and adaptable than ever before.
Property | Shape Memory Alloys (SMAs) | High-Entropy Alloys (HEAs) |
---|---|---|
Key Feature | Ability to remember and return to original shape when heated | Exceptional strength, hardness, and resistance to wear and corrosion |
Applications in Automotive | Actuators, engine valves, adaptive suspension systems | Engine parts, potentially lighter and stronger vehicle components |
Applications in Aerospace | Morphing wings for optimizing performance | Materials for hypersonic flight, capable of withstanding extreme conditions |
Sustainability | Potential for self-repair and adaptive capabilities | Durability leading to longer-lasting components |
How Okon Recycling Can Help with Alloy Recycling in Automotive and Aerospace Industries
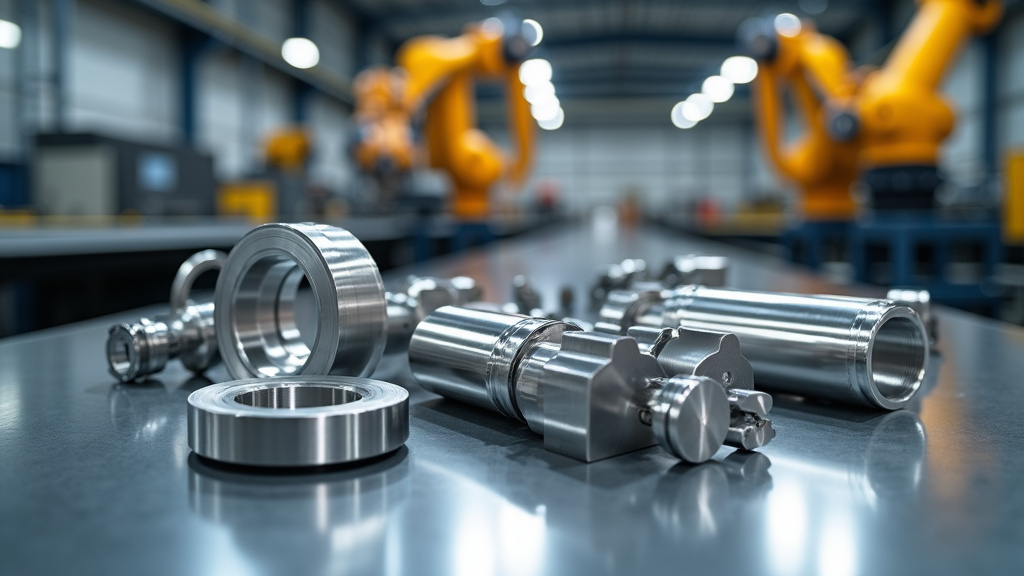
Alloy recycling is essential for the automotive and aerospace sectors, known for their rigorous material standards and complex metal compositions. Okon Recycling, with over a century of experience, transforms industrial scrap into valuable resources.
Since 1909, Okon has been committed to sustainability, gaining insights into the evolving needs of industries that rely on high-performance alloys.
Okon’s 20-acre facility in Dallas, Texas, is a technological marvel designed to handle challenging alloy compositions. Advanced sorting systems, including AI-powered technologies, ensure accurate processing of complex aerospace-grade materials.
Specialized Solutions for Automotive Alloys
The automotive industry’s shift towards lightweight, fuel-efficient vehicles increases the demand for specialized alloys. Okon Recycling excels in reclaiming these materials, handling everything from aluminum-based alloys in body panels to high-strength steels in safety components.
By partnering with Okon, automotive manufacturers can reduce waste and significantly lower the carbon footprint associated with alloy production. Recycling aluminum, a common component in modern vehicles, can save up to 95% of the energy required for primary production.
Okon’s commitment to quality ensures that recycled alloys meet or exceed industry standards, with rigorous quality control and advanced purification techniques resulting in materials indistinguishable from virgin alloys.
Aerospace Alloy Recycling: Precision and Purity
The aerospace industry uses exotic metals and strict material specifications, presenting unique recycling challenges. Okon Recycling addresses these with specialized processes for high-temperature alloys used in jet engines and turbines.
Okon recycles titanium alloys, superalloys, and other critical materials essential to aerospace manufacturing. This helps reduce reliance on increasingly scarce and expensive raw materials.
The environmental impact is significant, as aerospace-grade alloys often require energy-intensive production. Okon provides high-quality recycled alternatives, dramatically reducing energy consumption and carbon emissions.
Technological Edge in Alloy Management
Okon invests in cutting-edge technology, using advanced spectral analysis systems like X-ray fluorescence (XRF) sorting to precisely identify and separate alloy compositions. This accuracy is crucial for industries where material purity affects performance.
Okon’s facilities feature state-of-the-art melting and refining equipment, allowing them to process complex alloys with minimal loss of valuable elements, crucial for reclaiming rare earth elements in high-performance alloys.
These technologies ensure that recycled alloys meet the exacting standards of the automotive and aerospace industries, improving quality and expanding the range of alloys that can be effectively recycled.
Sustainable Partnership for Future Growth
As industries worldwide focus on sustainability, Okon Recycling is a vital partner in advancing a circular economy. They offer comprehensive waste management solutions tailored to automotive and aerospace manufacturers.
From on-site collection systems to detailed material tracking, Okon’s end-to-end solutions integrate seamlessly with clients’ operations, maximizing alloy recovery and helping companies meet environmental regulations and sustainability goals.
Partnering with Okon offers benefits beyond environmental considerations. Optimizing recycling processes can result in significant cost savings, with some programs reducing waste management costs by up to 40%, boosting the bottom line in industries with tight margins.
Embracing the Future of Alloys in Transportation
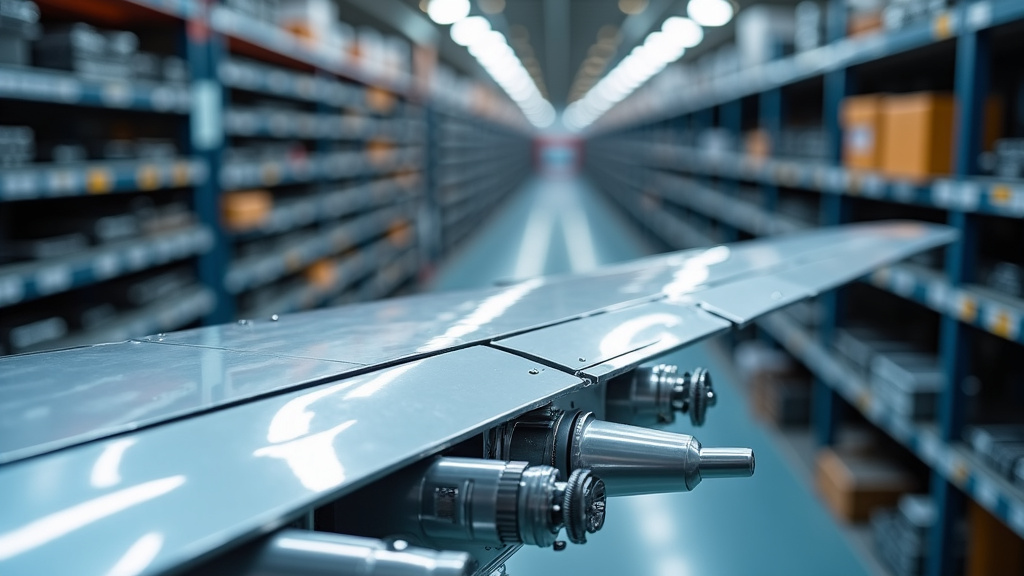
Alloys are crucial in transforming transportation, from lightweight aerospace components to robust automotive frames. These materials are reshaping how we move, offering a blend of strength, durability, and weight reduction essential for fuel efficiency and emissions reduction. However, the challenge remains: ensuring these resources serve us well into the future.
The circular economy reimagines our traditional ‘take-make-dispose’ approach. In this model, alloys are managed, recycled, and reintegrated into manufacturing, conserving resources and reducing the environmental impact of production.
Okon Recycling leads this sustainable initiative, closing the loop in alloy lifecycle management. Their innovative recycling solutions ensure that today’s transportation breakthroughs will continue to fuel progress for future generations.
To start a sustainable future in transportation alloys, contact Okon Recycling at 214-717-4083. Together, we can drive innovation while ensuring that today’s materials will benefit society for years to come.