5901 Botham Jean Blvd, Dallas, TX 75215
Unlocking The Secrets of Metal Extraction from Chillers
February 12, 2025Did you know your old refrigerator could be a hidden treasure trove of valuable metals? Outdated chillers collecting dust in junkyards contain zinc, lead, and other precious materials just waiting to be reclaimed. As the demand for new technologies grows, so does the need to recover these resources through advanced recycling methods.
Extracting metals from used chillers is no simple task—it requires cutting-edge techniques that push the boundaries of modern metallurgy. Three primary methods lead this effort: pyrometallurgy, which uses extreme heat to separate metals; hydrometallurgy, which relies on water-based solutions for extraction; and electrometallurgy, which uses electricity for precise metal recovery. Each plays a vital role in turning industrial waste into reusable materials.
At Okon Recycling, we specialize in recovering valuable metals from large-scale industrial equipment like chillers, ensuring that no resource goes to waste. By integrating these advanced recycling technologies, we help businesses reclaim materials efficiently while minimizing environmental impact.
This article explores how these innovative processes are revolutionizing metal recovery.
Advanced Techniques in Metal Recovery from Chillers
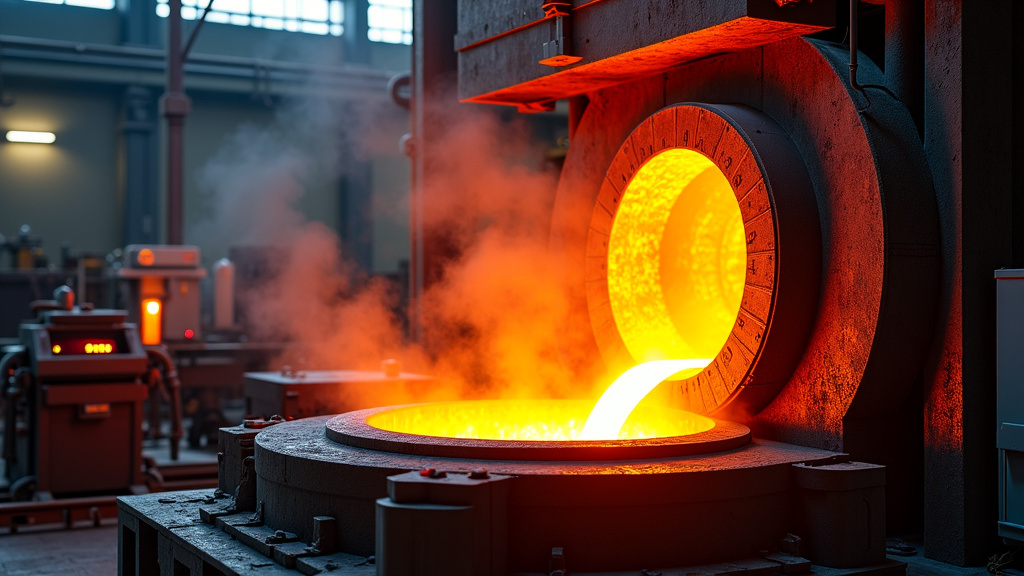
The recycling industry is continually evolving, aiming to extract maximum value from discarded materials. In chiller recycling, pyrometallurgical techniques have become transformative. These methods utilize high-temperature reactions to separate and recover valuable metals from end-of-life chiller units.
At the core of pyrometallurgical processes is smelting—an age-old technique revitalized through modern innovation. Today’s smelting operations do more than melt metal; they conduct complex chemical transformations, converting metallic impurities into usable, high-quality materials.
The Science Behind Advanced Pyrometallurgy
Pyrometallurgical techniques rely on precise temperature control to drive chemical reactions. As chiller components are heated to extreme temperatures, different metals react and separate based on their unique properties. This process allows recyclers to isolate copper, aluminum, and other valuable materials with remarkable efficiency.
Recent technological advancements have improved temperature management in pyrometallurgical systems. Cutting-edge furnaces now use sophisticated sensors and control systems, enabling operators to fine-tune temperatures with precision. This control maximizes metal recovery rates while minimizing energy consumption.
The benefits extend beyond efficiency. By optimizing reaction conditions, modern pyrometallurgical techniques also reduce harmful emissions and waste byproducts, making the recycling process more environmentally friendly—a critical consideration in today’s sustainability-focused world.
Enhancing Metal Yield Through Chemical Innovation
Temperature control is just one aspect. Equally important are the chemical reactions during smelting. Researchers have developed novel flux materials and additives that enhance metal separation and recovery.
These chemical innovations, combined with precise temperature control, boost metal yields. For instance, specially formulated fluxes can lower the melting point of certain metal compounds, allowing more efficient separation at lower temperatures. This improves recovery rates and reduces energy consumption—a win-win for recyclers and the environment.
The impact is significant. Many recycling facilities report metal recovery rates from chillers once thought impossible. Copper yields exceeding 99% purity are now achievable, and even trace amounts of precious metals can be economically extracted.
Real-World Impact: A Case Study in Efficiency
Consider the transformation of a mid-sized chiller recycling facility in the Midwest. Before implementing modern pyrometallurgical methods, this facility struggled with recovery rates around 70% for copper and even lower for other metals.
After upgrading to a state-of-the-art pyrometallurgical system with advanced temperature control and optimized chemical processes, the results were remarkable. Copper recovery rates soared to 98%, while the extraction of valuable trace metals became economically viable for the first time.
The facility’s energy consumption per ton of processed material decreased by 30%, significantly reducing operating costs and environmental impact. This case study demonstrates the transformative potential of advanced pyrometallurgical techniques in the chiller recycling industry.
Looking to the Future
As impressive as current pyrometallurgical methods are, researchers continue to push the boundaries. Emerging technologies like plasma-enhanced smelting and advanced sensor systems promise even greater control over the recycling process.
These innovations could unlock new possibilities in metal recovery, potentially allowing for the efficient extraction of critical materials that are currently difficult to recycle. As the demand for raw materials grows, maximizing recovery from electronic waste cannot be overstated.
The future of chiller recycling is promising, thanks to the relentless advancement of pyrometallurgical techniques. By combining precise temperature control, innovative chemical processes, and cutting-edge technology, the industry is set to play a crucial role in developing a more sustainable, circular economy.
Metal | Before Upgrade (%) | After Upgrade (%) |
Copper | 70 | 98 |
Other Metals | Lower than Copper | Improved to Economically Viable Levels |
The Role of Hydrometallurgy in Efficient Metal Extraction
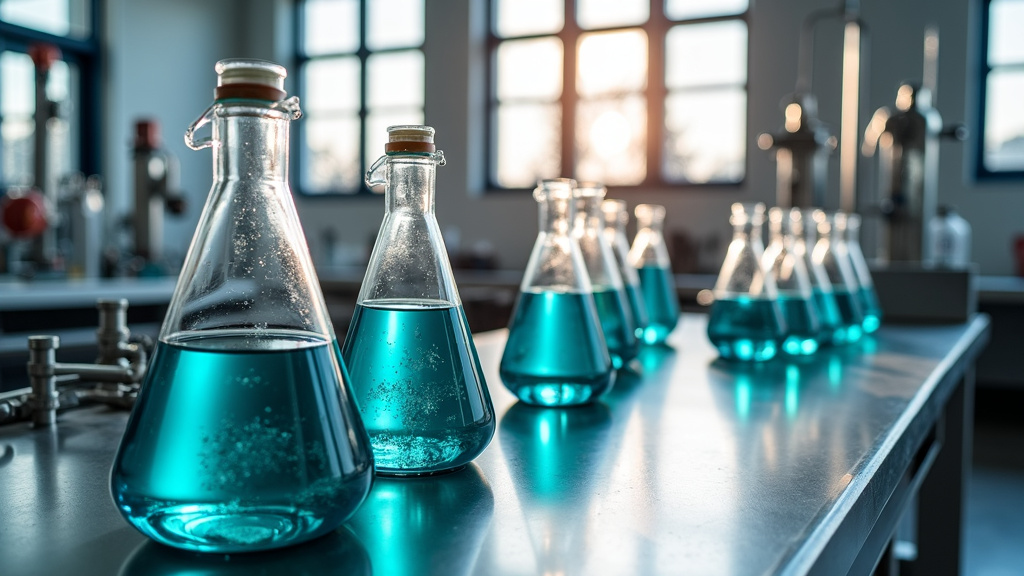
Hydrometallurgy has emerged as a transformative technique in metal extraction, utilizing aqueous solutions to recover valuable metals from ores, concentrates, and recycled materials. But what makes hydrometallurgy so unique?
Fundamentally, hydrometallurgy offers an environmentally friendly approach to metal extraction compared to traditional high-temperature methods. By utilizing chemical reactions in controlled aqueous environments, it significantly reduces greenhouse gas emissions, offering a more sustainable solution for an industry often associated with heavy environmental impacts.
The process of hydrometallurgy involves three key steps: leaching, solution concentration and purification, and metal recovery. Let’s explore these steps to understand their contribution to efficient metal extraction.
Leaching: The First Step in Metal Liberation
Leaching initiates the hydrometallurgical process by extracting metals from their ores. Aqueous solutions, which can be acidic or basic, are used to dissolve the desired metals into the solution.
Leaching is not a one-size-fits-all process. The choice of leaching agent and conditions depends on the specific metal and ore type. For instance, gold extraction often involves cyanide leaching, while copper might be leached using sulfuric acid.
The selectivity of leaching is a key factor in hydrometallurgy’s efficiency and environmental benefits.
Solution Concentration and Purification: Refining the Liquid Gold
Once metals are dissolved in the leach solution, the next step is concentration and purification to separate valuable metals from impurities.
Several techniques are employed here, each with its strengths. Solvent extraction uses organic solvents to selectively extract metal ions from the solution, while ion exchange resins adsorb specific metal ions for separation and concentration.
These methods act as fine-tuned filters, ensuring a solution rich in target metals and free from unwanted elements, achieving high metal recovery rates with minimal waste.
Metal Recovery: The Final Act
The final step in hydrometallurgy is recovering pure metals from the concentrated solution, transforming dissolved metal ions back into solid, usable metals.
Electrowinning plays a key role in recovering metals like copper and zinc, using electricity to deposit metal ions onto a cathode, resulting in high-purity metal products. Other methods, such as chemical reduction or precipitation, may also be used depending on the metal and desired end product.
This versatility allows for the production of metals with exceptional purity levels, meeting the stringent requirements of various industries.
Why Hydrometallurgy Shines in Efficient Metal Extraction
Hydrometallurgy excels by extracting metals efficiently while minimizing environmental impact. Operating at lower temperatures and pressures than pyrometallurgical processes, it consumes less energy and produces fewer emissions.
Additionally, the precision of hydrometallurgical techniques allows for processing low-grade ores and complex materials that might be uneconomical with traditional methods, improving resource utilization and opening new possibilities for metal recovery.
As demand for metals grows in our technology-driven world, hydrometallurgy provides a sustainable path forward, combining efficiency, environmental friendliness, and versatility to meet society’s metal needs while minimizing our ecological footprint.
Aspect | Hydrometallurgy | Pyrometallurgy |
---|---|---|
Energy Intensity | Lower | Higher |
Temperature Requirement | Lower | High |
Environmental Impact | Less emissions | High emissions |
Metal Recovery Process | Aqueous solutions | High heat |
Selective Metal Recovery | More selective | Less selective |
Innovations in Electrometallurgical Applications
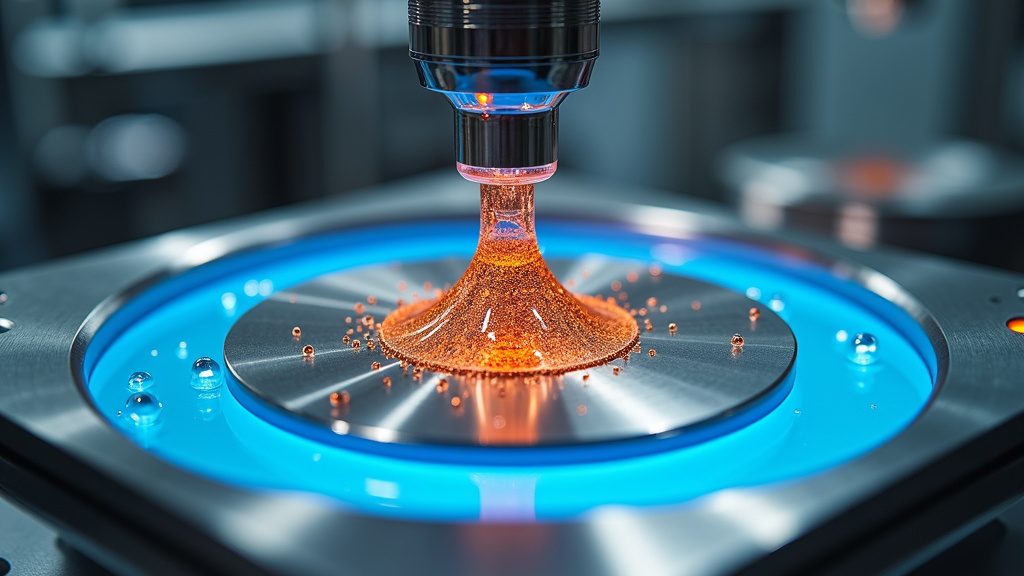
Electrometallurgy leads the way in metal extraction technology, offering a novel approach to obtaining high-purity metals. This process utilizes electrolytic cells, transforming metal production with its efficiency and environmental benefits.
Electrometallurgy uses electrical energy to extract and refine metals, achieving exceptional purity. This technique is particularly effective for metals like copper and nickel, crucial in industries from electronics to construction.
A major advantage of electrometallurgy is its cost-effectiveness. Applying an electric current to extract metals from solutions minimizes the need for extensive chemical treatments and reduces production costs.
Energy Conservation: A Key Benefit
In an era where energy conservation is crucial, electrometallurgy is a sustainable option. Unlike traditional methods requiring large amounts of heat and chemicals, electrolytic processes are energy-efficient.
This efficiency comes from the precise control over extraction. By fine-tuning electrical currents, metallurgists optimize energy use, effectively separating metal ions from solutions.
Moreover, the energy savings extend beyond extraction. High-purity metals produced through electrometallurgy often require less post-processing, further reducing the energy footprint of metal production.
Resource Preservation Through Innovation
Electrometallurgy’s impact on resource conservation is significant. Traditional methods often lead to waste and environmental damage. In contrast, electrolytic cells can process lower-grade ores and recycled materials efficiently.
This capability extends the life of ore deposits and opens possibilities for recovering metals from sources previously uneconomical. Electrometallurgy plays a crucial role in the circular economy, promoting the reuse and recycling of metal resources.
The precision of electrometallurgical processes means a higher percentage of the target metal can be extracted. This efficiency results in less waste and a more sustainable use of our mineral resources.
Advancements in Electrolytic Cell Design
Recent innovations in electrolytic cell design have enhanced electrometallurgy’s capabilities. Engineers have developed cells with improved electrode materials, leading to higher current densities and faster extraction rates.
These advancements have increased productivity and expanded the range of metals that can be extracted. From rare earth elements to refractory metals, the applications of this technology continue to grow.
Additionally, integrating automation and real-time monitoring has revolutionized electrolytic processes. These systems adjust parameters on the fly, ensuring consistent quality and maximum efficiency.
Environmental Impact and Future Prospects
Electrometallurgy’s reduced environmental impact is compelling. The process produces fewer emissions and requires less land disturbance, making it attractive for environmentally conscious industries.
As demand for high-purity metals rises, driven by renewable energy and electric vehicles, electrometallurgy will play a vital role. Its ability to deliver quality and sustainability positions it as key to the future of metal production.
Electrometallurgy represents a leap forward in metal extraction. Offering a cost-effective, energy-efficient, and environmentally friendly approach, it addresses many challenges facing the metallurgical industry. As research continues, we can expect further innovations, cementing electrometallurgy’s place in modern metal production.
Conclusion: Towards a Sustainable Metal Extraction Future
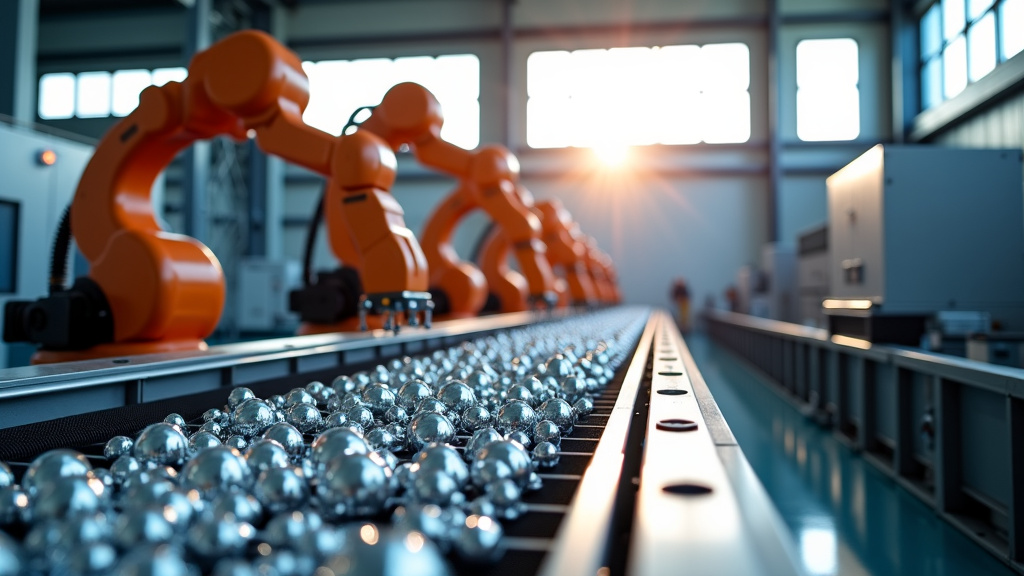
The metal recycling industry is undergoing a transformation, driven by cutting-edge advancements in pyrometallurgy, hydrometallurgy, and electrometallurgy. These innovations are not just improving recycling—they are reshaping sustainability and resource management on a global scale.
With AI-driven robotics, sensor-based sorting, and advanced chemical processes, we are achieving unprecedented efficiency in material recovery. The benefits are clear: lower environmental impact, conservation of finite resources, and progress toward a circular economy. As these technologies evolve, recycling rates will rise, creating new jobs, driving innovation, and strengthening supply chains.
However, the future of sustainable metal extraction requires collective action. Governments, businesses, and consumers must work together through supportive policies, corporate sustainability initiatives, and public awareness campaigns. The shift toward a greener future is not just an environmental necessity—it’s an economic imperative.
At Okon Recycling, we are at the forefront of this revolution, using advanced recycling technologies to recover valuable metals efficiently and responsibly. Now is the time to act. Contact Okon Recycling at 214-736-9509 to learn how your business can benefit from cutting-edge metal recovery solutions.
Together, we can turn yesterday’s waste into tomorrow’s resources—one recycled metal at a time.