5901 Botham Jean Blvd, Dallas, TX 75215
What Is the Future of Recycling Technology?
April 26, 2025The world generates over 2 billion tons of municipal solid waste each year, yet only 13.5% is recycled. This reality is driving advancements in recycling technology.
Innovations are transforming how we recover, process, and reuse materials that would otherwise end up in landfills. These technologies aim to close the loop in our resource systems and create sustainable waste management solutions.
The future of recycling is being reimagined through advanced sorting technologies using artificial intelligence and robotics. Companies like ZenRobotics have developed robotic waste sorting systems capable of processing up to 70 metric tons of waste per hour, surpassing human capabilities.
How Are Advanced Sorting Technologies Transforming Recycling?
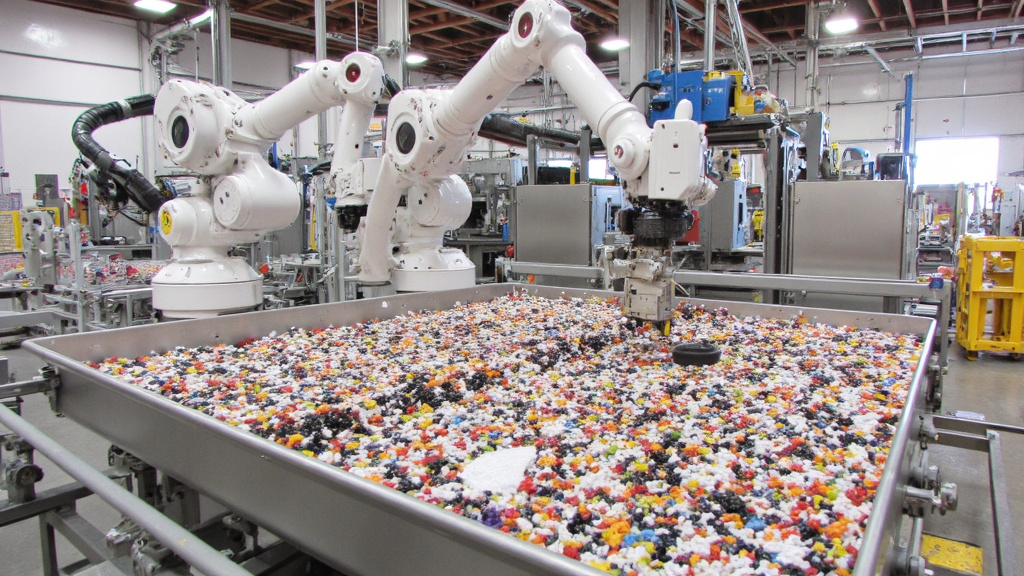
Advanced sorting technologies are revolutionizing recycling facilities globally. AI-powered systems now identify and separate materials with accuracy far exceeding traditional manual sorting. These automated solutions address a critical challenge in the recycling industry: contamination.
AI-equipped cameras with machine learning algorithms recognize materials based on shape, color, texture, and brand labels. They process images in milliseconds, enabling real-time identification of recyclables on fast-moving conveyor belts. The technology continually improves, learning to identify new packaging materials and adapting to changes in waste streams.
Optical sorting technologies use sensors to detect material properties. Near-infrared (NIR) scanners, for instance, identify various plastic types that appear identical to the human eye. When these scanners detect a specific material, they activate air jets to direct the item into the correct collection stream. This technology operates at remarkable speeds, processing tons of materials hourly with minimal errors.
Robotic Systems: The Physical Sorting Solution
Robotic arms with AI vision systems represent the next evolution in recycling technology. Companies like AMP Robotics have developed systems combining sophisticated computer vision with precise mechanical arms. These robotic sorters pick out specific items from mixed waste streams and place them in appropriate bins.
The impact of these robots extends beyond efficiency. By handling hazardous and contaminated materials, robots create safer working conditions for human employees. Recycling facilities can operate longer hours with consistent sorting accuracy, regardless of lighting conditions or worker fatigue.
The precision of these robotic systems significantly reduces contamination rates. A single contaminant can render an entire batch of recyclables unusable, so this improvement directly results in higher-quality recycled materials that command better market prices.
Real-World Results and Efficiency Gains
Recycling facilities using advanced sorting technologies report substantial improvements. Many operations have increased throughput by 50% while reducing sorting errors by up to 90%. For example, a single AI-powered robotic sorting system can replace the work of multiple human sorters while maintaining higher accuracy levels.
The financial benefits are equally impressive. While the initial investment in these technologies can be significant, facilities typically recoup costs through operational savings, increased material recovery, and higher-quality output. Contamination rates have dropped dramatically at facilities using these advanced systems, allowing them to produce cleaner material streams that meet strict quality standards in domestic and international markets.
Beyond the sorting line, these technologies generate valuable data about waste composition. This information helps facilities optimize their processes and provides insights to manufacturers about packaging design and recyclability. Such data-driven approaches create opportunities for continuous improvement throughout the recycling chain.
Advanced sorting technologies are transforming recycling from a labor-intensive, imprecise process into a high-tech industry capable of processing more materials with greater efficiency. As costs decrease and capabilities improve, these systems will likely become standard in recycling facilities of all sizes, playing a crucial role in building a more sustainable, circular economy.
What Innovations are Addressing Plastic Waste Challenges?
The global plastic waste crisis demands innovative solutions. With less than 15% of collected plastics being recycled through conventional methods, new technologies are emerging to tackle previously unrecyclable materials.
Chemical Recycling: Breaking Plastics Down to Build Them Back Up
Chemical recycling breaks down plastic waste into its primary chemical components. Unlike mechanical recycling, which works efficiently with specific plastic types, chemical processes can handle mixed plastic waste.
This technology uses processes like pyrolysis and depolymerization to transform plastics into valuable raw materials. Pyrolysis applies high temperatures without oxygen to break down plastic molecules into smaller components that can become new plastics or fuels.
The environmental benefits are substantial. Chemical recycling diverts the 90% of collected plastics that would otherwise end up in landfills, oceans, or incinerators, creating a circular economy where plastic waste becomes the feedstock for new products.
Enzymatic Recycling: Nature’s Solution to Synthetic Problems
Enzymatic recycling harnesses biological processes to break down plastic materials. This approach uses specially designed enzymes that can decompose plastic polymers into their basic building blocks.
The process works similarly to how enzymes in our bodies break down food. Scientists have identified and enhanced specific enzymes that can digest plastic polymers, effectively returning them to their original monomers.
The primary advantage of enzymatic recycling is its environmental friendliness. It operates under mild conditions without requiring the high temperatures or harsh chemicals used in other recycling methods.
Advanced Catalysis and Solvolysis
Scientists are developing more efficient catalysts to accelerate chemical recycling reactions while reducing energy requirements, making the process more economically viable and environmentally sustainable.
Solvolysis uses solvents to dissolve and purify plastics. Companies like Unilever and P&G have invested in solvent-based purification to create circularity within their polyethylene and polypropylene usage.
For challenging plastics like PET, depolymerization catalysts are an area of intense research, significantly increasing the cost-effectiveness of recycling processes.
Technology | Efficiency | Environmental Impact | Scalability | Cost |
---|---|---|---|---|
Chemical Recycling | High | Low | Medium | High |
Enzymatic Recycling | Medium | Very Low | Low | High |
Advanced Pyrolysis | Medium | Medium | High | Medium |
Solvent-Based Recycling | High | Low | Medium | High |
Microbial Decomposition | Low | Very Low | Low | Low |
AI-Powered Sorting | High | Low | High | Medium |
Plasma Pyrolysis | High | Medium | High | High |
Blockchain | High | None | High | Medium |
Biodegradable Plastics | Medium | Very Low | High | Medium |
Electrochemical Recycling | High | Very Low | Low | High |
Hydrothermal Treatment: A Newer Approach
Hydrothermal treatment (HTT) uses water under supercritical conditions to both heat and dissolve mixed plastics. Since no direct combustion occurs, HTT avoids producing toxic byproducts associated with some other methods.
This process generates higher product yields than pyrolysis or gasification. As a newer technology, HTT requires more refinement before widespread commercialization but shows great promise for creating a circular plastic economy.
Smart Sorting and Traceability Systems
Advanced technologies like artificial intelligence and IoT devices are revolutionizing waste sorting. Smart systems can accurately identify and sort different plastic types based on their chemical compositions and properties.
Traceability systems track recycled materials throughout the supply chain, ensuring transparency and accountability. These advancements streamline the recycling process and promote responsible management of plastic waste.
The combination of chemical innovation and digital technology creates a powerful framework for solving our plastic waste challenges. While no single solution can address the entire problem, these innovations collectively move us toward a future where plastic waste becomes a valuable resource rather than an environmental burden.
How is E-Waste Recycling Advancing?
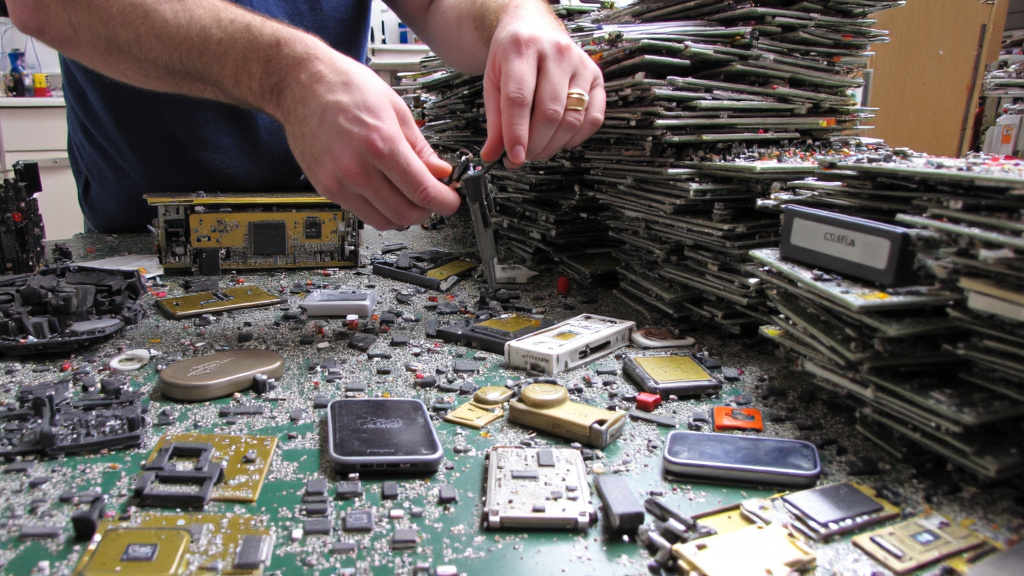
E-waste recycling is advancing through innovative methods to recover valuable materials from discarded electronics. Two key technologies leading this progress are urban mining and hydrometallurgical processes. These approaches transform what was once considered waste into valuable resources.
Urban Mining’s Impact
Urban mining marks a significant shift in resource recovery. Unlike traditional mining that extracts raw materials from the earth, urban mining retrieves precious metals and rare elements from discarded electronic products. This concept, evolved from landfill mining, offers new opportunities for reclaiming value from obsolete materials.
The process involves collecting electronic waste such as laptops, cellphones, and circuit boards. These items contain small but significant amounts of valuable materials including gold, silver, copper, tungsten, lithium, and neodymium. Urban mining reduces the need for virgin mining, which has reached a point of diminishing returns in technological advancement.
Recycling one ton of cell phones can yield more gold than processing one ton of ore from a gold mine, highlighting the efficiency of urban mining as electronic waste volumes grow worldwide.
Hydrometallurgy: A Chemical Approach
Hydrometallurgy is another powerful advancement in e-waste processing. This chemical-based approach uses aqueous solutions to extract and separate metals from electronic components. The technique is particularly effective for selective metal separation and can be implemented on a smaller scale than traditional recycling methods.
The process typically involves leaching metals using various chemicals, followed by separation and purification steps. Hydrometallurgical methods achieve high purity levels in recovered metals, making them suitable for producing materials that meet industrial standards for reuse in new electronics.
A key advantage of hydrometallurgy is its precision. Specific metals can be targeted and extracted with minimal waste, making the approach more efficient than conventional recycling methods. This process is effective for recovering precious metals like gold and platinum from circuit boards.
Biohydrometallurgy: The Eco-Friendly Alternative
A sustainable variation of hydrometallurgy is gaining traction in the recycling industry. Biohydrometallurgy uses microorganisms to facilitate metal extraction from e-waste, reducing the need for harsh chemicals in traditional hydrometallurgical processes.
Bioleaching employs bacteria that naturally extract and concentrate metals from materials. These microorganisms process electronic waste while minimizing environmental impact. The technique represents a green alternative that aligns with broader sustainability goals.
Biohydrometallurgy significantly decreases chemical consumption compared to traditional methods, creating both environmental and economic benefits for recycling operations. The technology continues to advance as researchers develop more efficient microbial strains.
Environmental and Economic Benefits
These technological advances deliver substantial environmental benefits. By recovering metals from existing products rather than mining virgin materials, urban mining and hydrometallurgy reduce the carbon footprint associated with resource extraction and minimize the volume of electronic waste entering landfills.
Economically, these processes create value from what was previously considered waste. The recovery of precious and rare earth metals provides manufacturers with alternative material sources, helping buffer against supply chain disruptions and price volatility in raw materials.
The economics of e-waste recycling depends on the specific technologies employed and the types of electronic waste processed. High-value components like circuit boards yield better returns than bulky items with fewer precious materials. As technology improves, the cost-effectiveness of these processes continues to increase.
The Future of E-Waste Processing
As e-waste volumes grow, recycling technologies must continue to evolve. Increased recycling rates and more efficient processing methods are essential for moving toward a circular economy. Both urban mining and hydrometallurgical approaches play crucial roles in this transition.
The combination of different techniques often yields the best results. Many recycling operations now use hybrid approaches that combine preprocessing with various metallurgical methods. This integrated strategy maximizes resource recovery while minimizing environmental impact.
Advances in automation and artificial intelligence are further enhancing e-waste processing. These technologies improve sorting accuracy and processing efficiency. Smart systems identify valuable components and optimize extraction methods based on material composition.
Metal | Urban Mining Recovery Rate | Traditional Mining Recovery Rate |
---|---|---|
Gold | 300 times more gold per ton of smartphones than gold ore | 1 ton of gold ore |
Copper | 85% less energy required | 4.5 tons of CO2 per ton of metal |
Aluminum | 95% less energy required | N/A |
As these technologies mature, they will become increasingly central to resource conservation strategies. The metals recovered through advanced e-waste processing will help meet growing demand for materials essential to electronics manufacturing, creating a more sustainable cycle of production and consumption in the electronics industry.
Conclusion: Recycle Smarter with Okon Recycling
Recycling technology is advancing rapidly—transforming waste into valuable resources and creating new economic and environmental opportunities. But these innovations only have an impact when recycled materials are collected, processed, and reintroduced responsibly into the supply chain.
Okon Recycling is proud to be part of this future. We help communities, businesses, and industries close the loop by responsibly recycling scrap metals, industrial magnets, and other valuable materials that traditional waste systems often overlook. Together, we can turn yesterday’s waste into tomorrow’s solutions.
Have recyclable materials ready? Contact Okon Recycling at 214-717-4083 today to be part of the smarter, more sustainable future.