5901 Botham Jean Blvd, Dallas, TX 75215
Recycled Magnet Materials: What Are They?
April 16, 2025Recycled magnet materials offer a sustainable alternative to virgin resources by reclaiming magnetic components from discarded electronic devices, industrial equipment, and household items. These valuable materials, especially those containing rare earth metals like neodymium and samarium-cobalt, as well as alnico (aluminum-nickel-cobalt) composites, are salvaged through specialized processes for reuse.
The environmental impact of traditional magnet production is significant, particularly with rare earth magnets. Mining and processing these elements involve resource-intensive operations that can leave a substantial ecological footprint. Recycling provides a promising solution by reducing the need for new raw material extraction and preventing hazardous components from reaching landfills.
Transforming discarded magnets into reusable materials involves a multi-stage process. This typically starts with the careful disassembly of original products, followed by the removal of non-magnetic components.
How Are Different Types of Magnets Recycled?
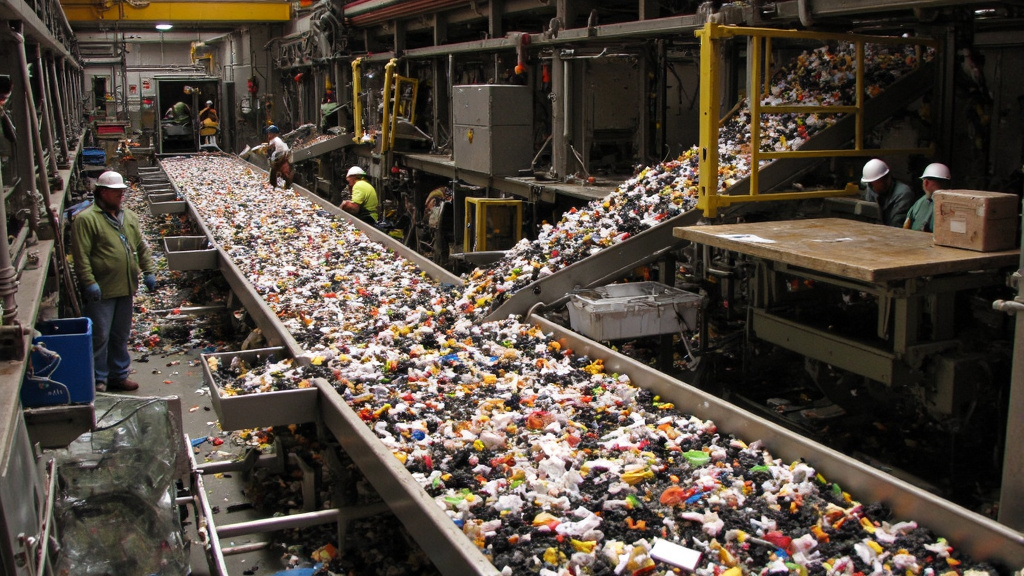
Each type of magnet presents unique challenges and opportunities for recycling due to their distinctive material compositions and manufacturing processes. The recycling approach varies significantly between magnet types, with some being more conducive to recovery than others.
SmCo (Samarium-Cobalt) Magnet Recycling
SmCo magnets, composed primarily of samarium and cobalt, are among the more valuable magnets to recycle due to the scarcity and economic value of their component materials. When these magnets are of good quality with minimal contamination, they can be effectively recycled through several methods.
The oxidative dissolution process is particularly effective for SmCo magnets. This method involves dissolving the magnet materials using trichloride ionic liquids that safely store chlorine gas. The process converts metals to corresponding metal chlorides while simultaneously reducing trichloride anions to chloride ions. The maximum capacity for this dissolution method reaches approximately 71 mg of SmCo magnet per gram of ionic liquid when additional coordinating chloride ions are present.
Direct recycling is considered the simplest approach, where the magnet is converted to an alloy powder that can be processed into new magnets. However, this method is only viable when working with a waste stream of consistent chemical composition and when the magnets are neither broken nor oxidized at the surface.
Alnico Magnet Recycling
Alnico magnets, made from aluminum, nickel, and cobalt, once dominated the market before rare earth magnets became widespread. Their recycling process involves melting the magnets down to recover the constituent metals, which can then be reused in new magnet production or other applications.
For efficient recycling, custom Alnico magnets can be designed with materials that are easier to recycle and can be effectively recovered at the end of their lifecycle. The cobalt content in these magnets makes them valuable for recycling but also presents certain challenges during the recovery process.
Like SmCo magnets, Alnico variants can be recycled if their quality remains high and contamination levels are low. The process typically requires specialized recycling facilities that can handle the separation and recovery of these valuable materials.
NdFeB (Neodymium-Iron-Boron) Magnet Recycling
NdFeB magnets are the strongest permanent magnets available and widely used in modern electronics, wind turbines, and electric vehicles. However, they present significant recycling challenges due to their susceptibility to corrosion and common nickel plating.
These magnets often feature protective nickel coatings that must be removed before recycling. Additionally, NdFeB magnets easily corrode when exposed to moisture, which can compromise their integrity and complicate the recycling process. Despite these challenges, the high value of neodymium makes their recycling economically viable when proper methods are employed.
The recycling process for NdFeB magnets typically involves separating the rare earth elements from other components. This can be accomplished through hydrometallurgical methods, which use acid leaching followed by selective precipitation or solvent extraction to isolate the valuable rare earth elements.
Ferrite Magnet Recycling
Ferrite magnets, also known as ceramic magnets, are the most common and inexpensive type. Made from iron oxide combined with barium or strontium carbonate, they are relatively simple in composition. Despite their widespread use, ferrite magnets present an interesting recycling paradox: while inexpensive to produce from virgin materials, they are costly to recycle.
The economic challenge stems from the low market value of the recovered materials compared to the energy and processing costs required for recycling. This unfavorable cost-benefit ratio often makes ferrite magnet recycling economically unviable unless performed at large scales.
When recycled, ferrite magnets can be processed through standard ferrous metal recycling systems, where they are typically melted down and repurposed as iron input for steel production rather than being remade into new magnets.
Flexible Magnet Recycling
Flexible magnets, commonly found in promotional products, refrigerator magnets, and door seals, consist of ferrite powder mixed with flexible polymer binders. Their recycling process involves grinding the materials up for reprocessing.
However, these magnets frequently contain additives such as paper, adhesives, or vinyl coatings that significantly complicate the recycling process. These non-magnetic components must be separated from the magnetic materials before effective recycling can occur, often requiring additional processing steps that increase the overall recycling cost.
The polymer matrix that provides the flexibility also creates challenges, as it must be broken down or separated from the magnetic particles. Despite these complications, the widespread use of flexible magnets makes developing efficient recycling methods for them increasingly important.
The Economics of Magnet Recycling
The economic viability of recycling different magnet types depends heavily on material value, processing costs, and market demand. Rare earth magnets like SmCo and NdFeB generally offer better economic returns due to the high value of their component materials, despite more complex recycling requirements.
For recycling facilities, the collection and transportation of magnets present additional challenges. Magnets are often embedded within larger products and devices, making extraction labor-intensive and potentially costly. Additionally, handling strong magnets requires specialized equipment due to their magnetic properties, which can cause them to attract to each other or to processing machinery.
As technologies advance and environmental regulations tighten, the economics of magnet recycling continues to evolve. Innovations in recycling processes aim to reduce costs while increasing material recovery rates, potentially making previously unviable magnet recycling economically feasible in the future.
What is the Future of Magnet Recycling?
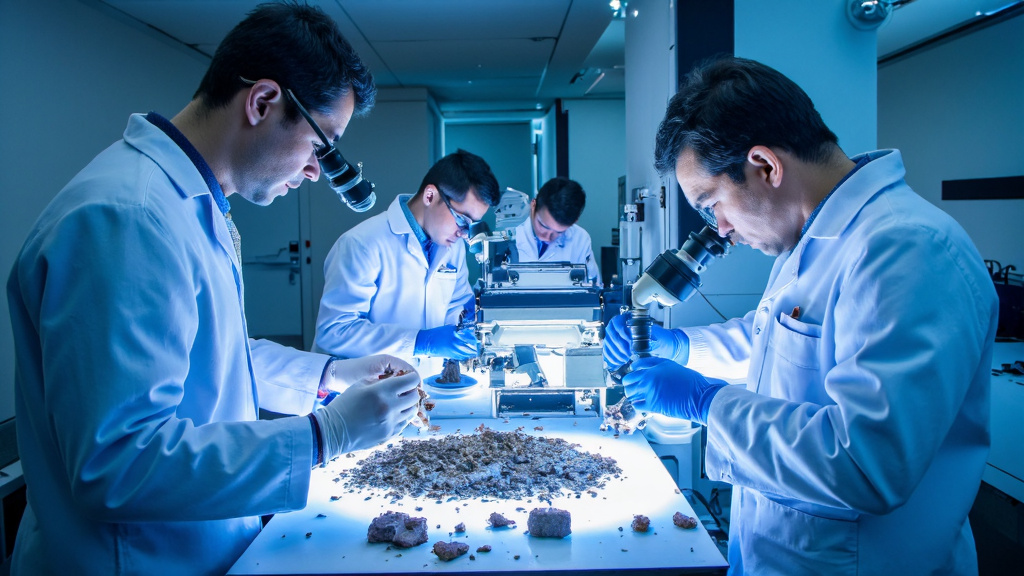
Scientists in a futuristic laboratory examining rare earth samples, surrounded by holographic market projections.
The future of rare earth magnet recycling is promising as technological advancements and growing environmental awareness drive innovation. With less than 1% of rare earth elements currently recycled globally, there is significant potential for growth as researchers develop more efficient and cost-effective techniques for recovering these valuable materials from end-of-life products.
One of the most promising developments is the advancement of hydrogen-assisted direct recycling methods.
This technology has progressed significantly and is nearing commercial readiness, with the capability to produce high-quality powders suitable for manufacturing high-performance N45+ magnets. The H2020 SUSMAGPRO project has demonstrated the HPMS (Hydrogen Processing of Magnetic Scrap) process at a pilot scale of 100 tonnes per year, showcasing its viability as an energy-efficient and environmentally friendly alternative to traditional recycling methods.
Final Words
For a viable circular economy in magnet recycling, improvements in eco-design and collection infrastructure are essential. Looking ahead, we can expect regulations addressing take-back programs, recycling rates, labeling requirements, and traceability. These measures, combined with increasing awareness among manufacturers and users of magnet-containing components, will help create a more sustainable supply chain for these critical materials.
As we address the challenges of securing rare earth elements for green technologies, recycling will play an increasingly important role in mitigating supply risks and reducing environmental impact. Contact Okon Recycling at 214-717-4083 to learn more about how our innovative recycling solutions can help your organization contribute to a more sustainable future for rare earth magnets.