5901 Botham Jean Blvd, Dallas, TX 75215
What is Eco-friendly Magnet Production?
April 16, 2025Eco-friendly magnet production marks a significant shift in manufacturing magnetic components for today’s world. This approach focuses on sustainable practices that reduce environmental impact while meeting the global demand for magnetic materials in products from smartphones to wind turbines.
The need for environmentally responsible magnet production is more urgent than ever. Traditional methods, especially for rare earth magnets like neodymium and samarium-cobalt, involve mining processes that generate toxic waste and consume large amounts of water and energy. These practices can lead to habitat destruction and release harmful pollutants into the environment.
As industries adopt cleaner technologies, eco-friendly magnet production is leading technological innovation and environmental care. By rethinking how these components are sourced, manufactured, and recycled, we can continue technological advancement while significantly reducing the ecological impact of the devices we use daily.
What Are the Environmental Challenges of Traditional Magnet Production?
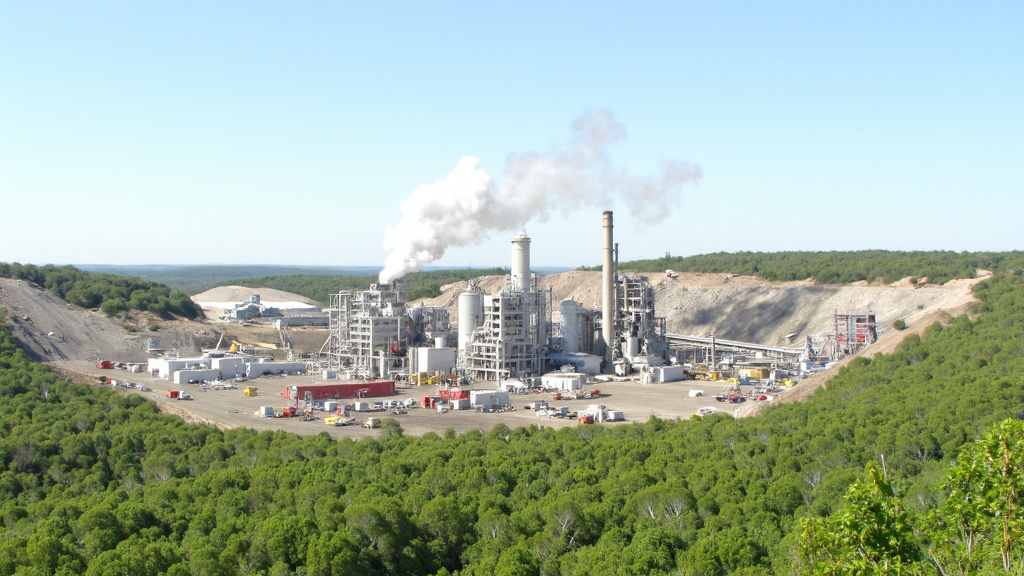
Traditional magnet production, especially for rare earth magnets like neodymium-iron-boron (NdFeB), leads to environmental issues that extend beyond the manufacturing facility. The journey from raw material to finished product leaves a trail of ecological disruption, raising serious sustainability concerns among environmental scientists and policymakers.
Destructive Mining Practices
Open-pit mining, commonly used for extracting rare earth elements, drastically alters landscapes and destroys local ecosystems. These operations strip away topsoil and vegetation, eliminating habitats for numerous plant and animal species while creating massive excavation sites visible from space.
The mining process affects more than just the immediate area—it creates ripple effects throughout surrounding environments. Groundwater patterns change, erosion accelerates, and once-thriving ecosystems become industrial wastelands that may take decades or centuries to recover, if ever.
Toxic Chemical Processing
After extraction, rare earth elements are separated from their ores using harsh chemicals that pose severe environmental risks. The process typically employs sulfuric acid, ammonia, and other caustic substances that can contaminate soil and water systems if improperly managed.
These chemicals generate “tailings”—toxic waste materials containing processing chemicals, heavy metals, and sometimes radioactive elements naturally occurring with rare earth deposits. When these tailings leach into groundwater or nearby water bodies, they can poison ecosystems and threaten human water supplies.
The separation process requires multiple chemical baths and treatments, with each step generating additional waste that must be carefully contained to prevent environmental contamination. Unfortunately, in regions with less stringent environmental regulations, this waste management often falls short of adequate standards.
Significant Energy Consumption
The energy requirements for processing rare earth elements into usable magnets are substantial, significantly contributing to their environmental footprint. High-temperature furnaces and energy-intensive separation processes drive up electricity consumption, often sourced from fossil fuels.
This energy usage directly translates into greenhouse gas emissions. Depending on the energy mix of the production country, the carbon footprint of rare earth magnet production can be substantial, with some studies suggesting it accounts for 20-50% of the total global warming impact in the magnet life cycle.
The pre-treatment processes alone can represent 5-25% of the total greenhouse warming potential, highlighting how energy-intensive these initial manufacturing stages are. When this energy comes from coal-heavy grids like those in China—which produces approximately 54% of global rare earth supplies—the climate impact intensifies.
Radioactive and Heavy Metal Waste
Perhaps most concerning is the radioactive waste generated during rare earth element processing. Many rare earth deposits naturally contain thorium and uranium, radioactive elements that concentrate in waste streams during processing.
These radioactive materials, along with other heavy metals present in the ore, create waste management challenges that persist long after manufacturing is complete. Improper handling of these materials has led to documented cases of soil and water contamination near production facilities.
Managing this waste requires specialized containment facilities and monitoring systems, adding to both the environmental burden and production costs. Even with careful management, these waste materials remain hazardous for generations.
Aspect | Traditional Methods | Alternative Approaches |
---|---|---|
Environmental Impact | High due to toxic waste and energy consumption | Reduced by 95% using MnAlC instead of NdFeB |
Energy Consumption | High, often from fossil fuels | Lower energy requirements |
Resource Depletion | Significant due to rare earth mining | Less reliance on rare earth elements |
Waste Generation | Toxic tailings and radioactive waste | Less hazardous waste |
The combined impact of these environmental challenges has prompted increased scrutiny of the rare earth magnet supply chain, especially as demand grows for these materials in green technologies like wind turbines and electric vehicles. The irony is striking—materials essential for many clean energy technologies come with their own significant environmental costs.
How Can Recycling and Alternative Materials Promote Eco-friendly Magnet Production?
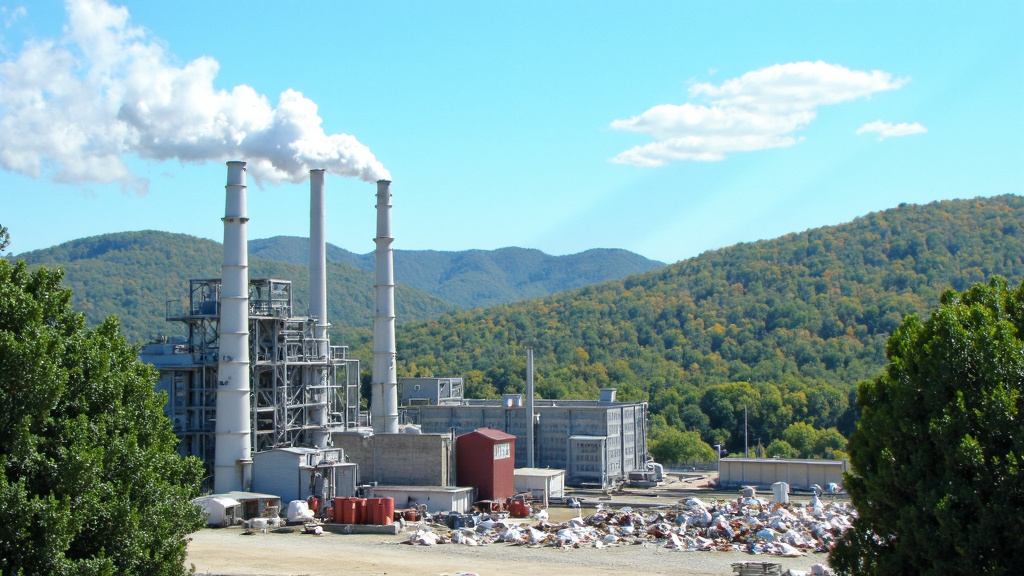
Recycling rare earth elements from discarded magnets and electronic waste is a key strategy for sustainable magnet production. With increasing demand for high-performance magnets in clean energy applications like wind turbines and electric vehicles, the environmental impact of traditional mining and processing is a growing concern.
Extracting rare earth elements involves energy-intensive processes that generate toxic waste and greenhouse gas emissions. Mining can disrupt habitats, cause soil erosion, and contaminate water. Recycling strategies help reduce these impacts while meeting the demand for magnetic materials.
Innovative Recycling Methods for Rare Earth Elements
Two main approaches for recycling rare earth magnets are short-loop and long-loop recycling. Short-loop recycling directly reprocesses magnets with less energy but may result in lower purity. Long-loop recycling, though more resource-intensive, yields higher purity materials for demanding applications.
Hydrometallurgical and pyrometallurgical processes are promising for reclaiming rare earth elements. These methods can recover neodymium, dysprosium, and others with high efficiency. For instance, acid leaching techniques can extract over 95% of rare earth content from discarded magnets, offering an alternative to mining virgin materials.
Electronic waste is rich in rare earth elements. A typical hard drive contains 10-20 grams of neodymium, and with billions of devices reaching end-of-life annually, the recycling potential is significant. Companies like REEcycle are pioneering commercial-scale recovery operations, turning e-waste into valuable resources.
Alternative Materials: Reducing Rare Earth Dependency
While recycling offers immediate benefits, researchers are also developing alternative magnetic materials. Iron nitride magnets, for example, are sustainable as they can be produced from abundant, low-cost materials without the need for environmentally damaging extraction processes. Toyota plans to phase out rare earth elements in their electric motors, showing industry interest in these alternatives.
Magnetocaloric materials are another promising area. These materials change temperature in magnetic fields and can be used in low energy consumption applications. Though still in development, magnetocaloric technology could provide an eco-friendly alternative to conventional magnetic cooling systems.
Greener Manufacturing Processes
Improving manufacturing procedures can also yield environmental gains. Green processes focus on reducing energy use, minimizing waste, and eliminating toxic chemicals. Advanced sintering techniques enhance magnetic properties while minimizing waste. Spark plasma sintering (SPS) produces high-performance magnets with less energy. Additive manufacturing (3D printing) of polymer-bonded magnets allows complex shapes with minimal waste.
Surface coating improvements enhance sustainability by increasing magnet durability and reducing replacement needs. Corrosion-resistant coatings using materials like nickel or zinc extend magnet lifespan, crucial for offshore wind turbines exposed to saltwater.
Economic and Environmental Benefits
Life cycle assessments show recycling rare earth elements significantly lowers environmental impacts compared to primary production. Recycling magnets requires 75-85% less energy than primary production, reducing greenhouse gas emissions.
Economic incentives reinforce these environmental advantages. As rare earth prices fluctuate, recycling offers a more stable, cost-effective supply chain. The European Commission invests in research programs to establish sustainable rare earth supply chains through recycling and material substitution.
Developing rare earth-free magnets reduces market volatility. By decreasing dependence on geographically concentrated resources, manufacturers can hedge against supply disruptions while reducing environmental impact.
Recycling Method | Description | Key Features |
---|---|---|
Hydrometallurgy | Uses aqueous solutions to dissolve and separate valuable elements | Resource-intensive, significant energy and chemical use |
Pyrometallurgy | Involves heating and smelting | Higher energy consumption, potential impurity issues |
Direct Recycling | Dismantling and reusing magnets | Least resource use, suitable for similar product reuse |
Hybrid Processes | Combination of pyro and hydro methods | High purity, involves complex processes |
Hydrogen Processing | Demagnetizes and forms alloy powder | Lower costs and carbon footprint |
As renewable energy technologies expand, the sustainability of their materials is crucial. Through innovative recycling technologies, alternative material development, and improved manufacturing processes, the magnet industry is moving toward environmentally responsible practices that support sustainability goals of clean energy systems.
What Role Do Green Manufacturing Processes Play in Eco-friendly Magnet Production?
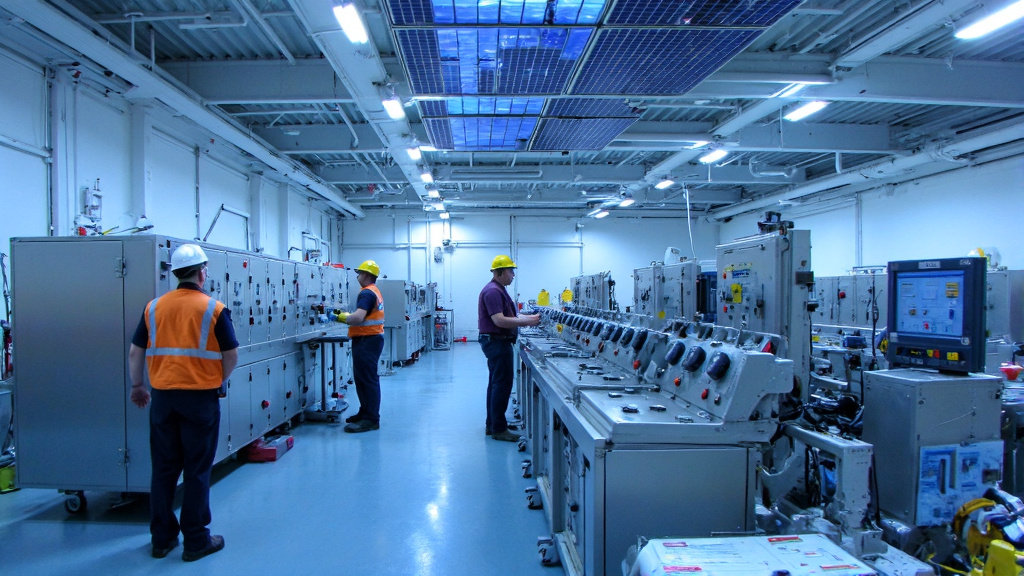
Green manufacturing processes are transforming magnet production, particularly for rare earth permanent magnets essential for renewable energy technologies and electric vehicles. These eco-friendly approaches significantly reduce the environmental impact of an industry traditionally known for its resource-intensive and polluting practices.
Traditional magnet production, especially for rare earth magnets like NdFeB (neodymium-iron-boron), faces substantial environmental challenges. The extraction and processing of rare earth elements often involve energy-intensive operations, toxic chemical usage, and the generation of radioactive waste byproducts containing thorium and uranium. These conventional methods can contaminate groundwater, soil, and air while consuming vast amounts of energy from non-renewable sources.
Renewable Energy Integration in Magnet Manufacturing
One of the most impactful innovations in green magnet manufacturing is the integration of renewable energy sources. Leading manufacturers are increasingly powering their facilities with solar panels and wind turbines, significantly reducing carbon emissions. For example, some facilities in Europe have cut their carbon footprint by up to 60% by transitioning from coal-powered electricity to on-site solar arrays combined with wind energy.
Beyond environmental protection, companies implementing renewable energy in their manufacturing processes report long-term cost savings of 15-30% on energy expenditures after the initial investment period. These savings contribute to economic sustainability while reducing dependence on fluctuating fossil fuel markets.
Water Conservation and Management Systems
Water conservation is another critical aspect of green magnet manufacturing. Traditional rare earth processing can consume between 200-400 cubic meters of water per ton of rare earth oxide produced. Advanced facilities now implement closed-loop water systems that recycle up to 90% of water used in production processes.
Beyond reducing consumption, these systems often incorporate advanced filtration technologies to remove contaminants before any water is discharged, protecting local watersheds and aquatic ecosystems. Some manufacturers have reduced their freshwater intake by implementing rainwater harvesting systems and drought-resistant landscaping around their facilities.
Energy-Efficient Equipment and Processes
The adoption of energy-efficient equipment throughout the magnet production process delivers substantial environmental and economic benefits. High-efficiency motors, variable speed drives, and advanced furnaces with precise temperature controls can reduce energy consumption by 20-40% compared to conventional equipment.
Process optimization also plays a crucial role. For instance, spark plasma sintering (SPS) technology used in some advanced magnet manufacturing facilities operates at lower temperatures and shorter processing times than traditional sintering methods. This approach not only reduces energy requirements but also enhances the magnetic properties and thermal stability of the final products.
Eco-Friendly Materials and Chemical Processes
The use of eco-friendly materials extends throughout the magnet manufacturing supply chain. Biodegradable cleaning agents have replaced harsh chemical solvents in many facilities. Some manufacturers have developed water-based coating processes for corrosion protection instead of using toxic chemical coatings.
Perhaps most promising is the growing use of recycled components in magnet production. The recycling of rare earth elements from end-of-life products and manufacturing waste helps close the material loop and reduces the need for environmentally damaging mining operations. While technical challenges remain, short-loop recycling methods that preserve the alloy composition are showing particular promise for reducing environmental impact while maintaining material quality.
Successful Implementation: Siemens Wind Power Case Study
Siemens Wind Power demonstrates the successful implementation of green manufacturing processes in magnet production for wind turbine generators. Their facilities utilize a comprehensive approach that combines renewable energy usage with advanced waste reduction strategies. By leveraging solar power for approximately 30% of their energy needs and implementing a closed-loop water recycling system, they’ve reduced water consumption by 75% compared to industry standards.
The company has also pioneered techniques for recovering and reusing rare earth materials from production scrap, achieving an impressive 95% recovery rate for neodymium and dysprosium. These integrated approaches have not only reduced their environmental impact but have also resulted in documented production cost reductions of approximately 12% over a five-year period.
Aspect | Traditional Manufacturing | Green Manufacturing |
---|---|---|
Energy Source | Fossil fuels | Renewable energy (solar, wind) |
Water Usage | High consumption | Closed-loop systems, rainwater harvesting |
Waste Management | Radioactive and heavy metal waste | Recycling and eco-friendly materials |
Environmental Impact | High CO2 emissions and pollution | Reduced carbon footprint, lower emissions |
Cost | High due to waste management | Lower long-term costs with renewable energy |
Balancing Cost, Quality, and Sustainability
While the benefits of green manufacturing in magnet production are clear, implementation challenges remain. The initial investment costs for renewable energy infrastructure and advanced equipment can be substantial, though decreasing technology costs and available incentives are improving the economic equation. Maintaining strict quality standards while implementing new processes requires careful engineering and quality control measures.
Despite these challenges, the market for eco-friendly magnets continues to grow, driven by consumer demand, regulatory pressures, and the commitment of major industries to reduce their environmental footprint. The increasing adoption of green manufacturing processes not only benefits the environment but also contributes to the long-term economic viability of magnet production by reducing resource dependencies and operational costs.
Conclusion: The Future of Eco-friendly Magnet Production

The environmental challenges of traditional rare-earth magnet production—from mining impacts to processing emissions—require innovative approaches that balance performance with ecological responsibility. The future of magnet manufacturing involves a multi-faceted approach combining recycling technologies, alternative materials, and greener production methods.
Recycling innovations show particular promise. Research into alternative materials such as manganese-aluminum-carbon (MnAlC) alloys offers viable paths to reduce reliance on critical rare-earth elements. Life cycle assessments indicate that when evaluated on functional energy density rather than mass alone, these alternatives can provide comparable environmental profiles to traditional neodymium magnets while avoiding supply chain vulnerabilities.
For businesses, municipalities, and sustainability officers addressing these challenges, a circular approach to magnet usage will be essential as global demand for these components rises with the expansion of renewable energy technologies and electric mobility.
For assistance with recycling solutions that can help reduce your organization’s environmental footprint while maintaining access to these critical materials, contact Okon Recycling at 214-717-4083.