5901 Botham Jean Blvd, Dallas, TX 75215
About Specialty Metal Processing Plants
February 21, 2025In the expansive field of modern manufacturing, specialty metal processing plants are vital, shaping the foundation of numerous industries. These facilities, often working behind the scenes, play a crucial role in transforming raw metals into precision-engineered components that power our world.
At the core of this complex ecosystem is the art and science of metal processing. It’s a domain where brute force meets finesse, where large-scale operations coexist with microscopic precision. Companies like Okon Recycling have become industry leaders, setting the standard for quality and innovation.
But what exactly happens within these metal marvels?
Imagine massive machines meticulously grinding stainless steel sheets, transforming rough surfaces into mirror-like finishes. Picture skilled technicians expertly buffing aluminum components to achieve a luster that would impress even the most discerning automotive designer.
The Critical Role of Metal Processing
Why does all this matter? In a world increasingly dependent on high-performance materials, the significance of specialty metal processing is immense. These plants are the unsung workhorses behind aerospace innovation, medical device precision, and cutting-edge electronics.
Consider the aerospace industry. Every aircraft relies on components that undergo rigorous processing. From the fuselage to the tiniest bolt, each metal piece must meet exacting standards of strength, weight, and durability. It’s here that specialty metal processors excel, polishing the future of flight.
In the medical field, the stakes are even higher. Surgical instruments, implants, and diagnostic equipment demand perfection. A microscopic flaw in a metal surface could mean the difference between a successful procedure and a catastrophic failure. This is where industry leaders like Specialty Metals Processing are invaluable, ensuring every scalpel and stent meets the highest standards of quality and safety.
A Symphony of Services
The range of services offered by these specialized facilities is impressive. Metal grinding, a cornerstone of the industry, involves precision removal of material to achieve specific dimensions or surface qualities. It’s a process that requires both brute force and delicate control, often removing mere microns of metal to achieve perfection.
Buffing and polishing, while often used interchangeably, are distinct processes that enhance metals. Buffing smooths surfaces and removes minor imperfections, while polishing creates a lustrous, mirror-like finish. These processes aren’t just about aesthetics; they significantly enhance a metal’s corrosion resistance and overall performance.
But the expertise doesn’t stop there. Many specialty metal processing plants offer a comprehensive suite of services, including advanced techniques like waterjet cutting, precision slitting, and surface treatments. This holistic approach allows them to tackle complex projects across diverse industries.
The Future of Metal Processing
As we look ahead, the world of specialty metal processing continues to evolve. Advancements in automation and AI are pushing the boundaries of what’s possible, allowing for even greater precision and efficiency. Meanwhile, the growing demand for sustainable practices is driving innovation in recycling and waste reduction within the industry.
The future promises exciting developments, from nano-scale surface treatments to revolutionary alloys that push the limits of material science. At the center of it all will be the specialty metal processing plants, continuing their vital work in shaping the metals that shape our world.
Advanced Techniques in Metal Processing
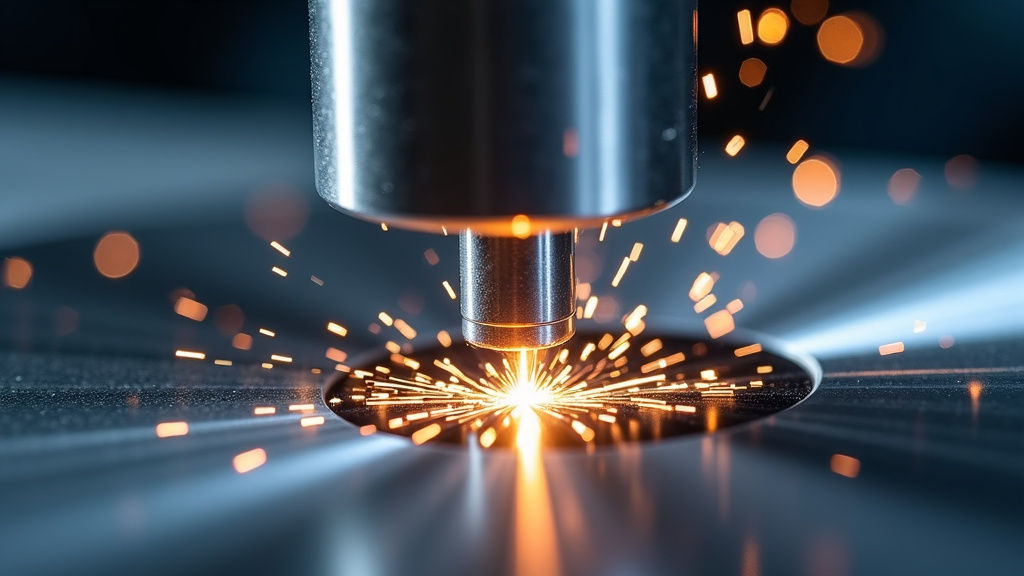
In metal fabrication, precision is crucial. Advanced techniques in metal processing have transformed material refinement, especially in industries where quality is imperative. Leading this transformation are precision grinding and advanced surface finishes.
Precision grinding, a key aspect of modern metal processing, uses abrasive wheels to remove small amounts of material from a workpiece. This method achieves tolerances as tight as ±0.0001 inches, essential for components in aerospace and medical applications. Consider the crafting of a hip replacement joint or critical jet engine parts – even the smallest flaw can lead to failure.
The Art of Precision Grinding
The aerospace industry relies on precision grinding to produce turbine blades, fuel injectors, and other vital parts. These components must endure extreme conditions while performing optimally. A jetliner at 35,000 feet is no place for inferior engineering.
Similarly, in medicine, precision-ground surgical instruments and implants must meet strict standards to ensure safety and success. The difference between a successful operation and a complication is often measured in microns – where precision grinding excels.
Grinding is just the start. Surface finishes add another layer to advanced metal processing, enhancing both the appearance and functionality of metal parts.
Elevating Quality with Surface Finishes
Surface finishing techniques like anodizing create a hard, durable oxide layer on aluminum parts. This process, common in aerospace and medical industries, boosts corrosion resistance and provides a base for further treatments. Anodized aluminum in satellites must withstand space’s harsh environment, where errors are unacceptable.
Electropolishing, another advanced finishing method, removes a microscopic metal layer to achieve an ultra-smooth, reflective surface. This technique is crucial for stainless steel medical devices, where a mirror-like finish prevents bacterial growth and eases sterilization.
The combination of precision grinding and advanced surface finishes has opened new frontiers in metal processing. These techniques enhance surface properties, improving durability, corrosion resistance, and functionality. In high-performance alloys used in cutting-edge industries, these processes are essential.
As we push the boundaries of metal fabrication, these advanced techniques continue to evolve. The pursuit of perfection in metal processing isn’t just about meeting current standards – it’s about setting new ones, advancing material science and engineering.
In conclusion, precision grinding and advanced surface finishes represent the pinnacle of metal processing technology. They are the unsung heroes in the products we rely on daily, from airplanes to lifesaving medical devices. As industries demand higher performance and reliability, these techniques will play an even more crucial role in shaping our technological future.
Technique | Precision Grinding | Surface Finishing |
Description | Uses abrasive wheels to remove minute amounts of material, achieving high tolerances. | Enhances surface properties, improving durability and aesthetics. |
Application | Used in aerospace and medical industries for components like turbine blades and surgical instruments. | Used to improve corrosion resistance and provide reflective surfaces. |
Benefits | Achieves tolerances as tight as ±0.0001 inches, crucial for high-performance components. | Improves corrosion resistance, durability, and aesthetic appeal. |
Examples | Turbine blades, fuel injectors, surgical instruments. | Anodizing aluminum parts, electropolishing stainless steel devices. |
Innovations Shaping the Future of Metal Processing
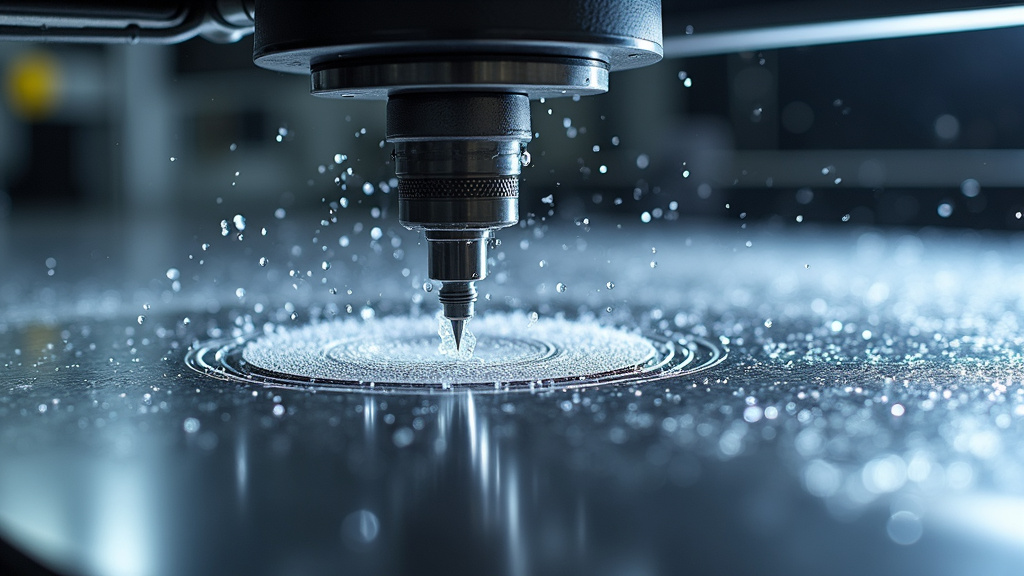
The metal processing industry is on the brink of significant technological advancements. New developments are transforming how we shape, cut, and finish metals, leading to unmatched precision and customization. Leading this change are two significant technologies: waterjet cutting and custom finish matching.
Waterjet cutting, which uses high-pressure water mixed with abrasive particles, is changing metal fabrication across industries. This method offers exceptional accuracy and versatility. According to KMT Waterjet, sectors like aerospace, automotive, and electronics greatly benefit from waterjet cutting solutions.
Beyond precision, waterjet cutting enables intricate designs and complex shapes once deemed impossible or impractical. It quenches the thirst for innovation across various sectors by overcoming previous limitations.
The Power of Precision: Waterjet Cutting Unleashed
Picture a water jet powerful enough to slice through metal like a hot knife through butter. This is the essence of waterjet cutting. By accelerating water to nearly three times the speed of sound and mixing it with abrasive particles, this technology becomes a precise and versatile cutting tool.
Waterjet cutting can handle materials ranging from soft rubber to hardened steel, all without the heat-affected zones common in traditional methods. It’s like having a Swiss Army knife for the industrial age—one tool that can tackle numerous materials and tasks.
The true magic of waterjet cutting is its ability to create complex shapes with minimal material waste. In a world focused on sustainability, this aspect is revolutionary. It’s not just cutting—it’s sculpting with water, turning metal sheets into intricate, functional art.
Custom Finish Matching: Where Art Meets Industry
While waterjet cutting reshapes metal formation, custom finish matching redefines perception. This process allows unprecedented customization in metal finishes, meeting the rising demand for unique, tailored solutions across industries.
Custom finish matching isn’t just about aesthetics—it enhances the functional purposes of metal surfaces. From corrosion resistance to electrical conductivity, a metal component’s finish can be as crucial to its performance as its shape or composition.
The versatility of custom finish matching is remarkable. Whether a mirror-like polish for reflection or a textured grip for a tool, this technology delivers. It offers a palette of infinite textures, resistances, and properties.
Meeting Evolving Industry Demands
The combination of waterjet cutting and custom finish matching responds to the evolving demands of modern industries. In today’s fast-paced market, one-size-fits-all solutions are no longer sufficient.
Industries require components that are both precisely crafted and uniquely tailored. The automotive sector, for example, needs metal parts with complex geometries and specialized finishes for optimal performance and aesthetics. Aerospace demands lightweight yet strong components with finishes that withstand extreme conditions.
These innovations in metal processing meet these challenges head-on, not only keeping pace with industry demands but also setting the pace, pushing the boundaries of metal fabrication.
The Future is Now: Embracing Metal Processing Innovations
The future of metal processing is clear: the industry is entering a new era. The convergence of technologies like waterjet cutting and custom finish matching creates possibilities once considered science fiction.
These innovations aren’t just about technical capabilities—they’re about practical benefits. They create more efficient processes, reduce waste, and deliver products that meet end-user needs precisely. They make the metal processing industry smarter, more adaptable, and more responsive to the rapidly changing world.
The future of metal processing is bright, shaped by these advanced technologies. As industries evolve and demand more specialized solutions, innovations like waterjet cutting and custom finish matching will continue to transform raw metal into precisely crafted components, pushing the boundaries of possibility.
In this new landscape of metal processing, the only limit is our imagination. With these tools at our disposal, that limit is pushed further every day. The metal processing industry isn’t just keeping up with the future—it’s creating it, one precisely cut, perfectly finished piece at a time.
Feature | Waterjet Cutting | Custom Finish Matching |
---|---|---|
Material Compatibility | Wide range including metals, composites, glass | Various finishes for metals |
Heat Affected Zone | None | N/A |
Precision | High precision, intricate designs | Customizable finishes for specific functions |
Environmental Impact | Minimal waste, sustainable | Enhances durability and performance |
Cost-Effectiveness | Reduces material waste | Improves product longevity |
Sustainable Practices in Metal Processing Plants
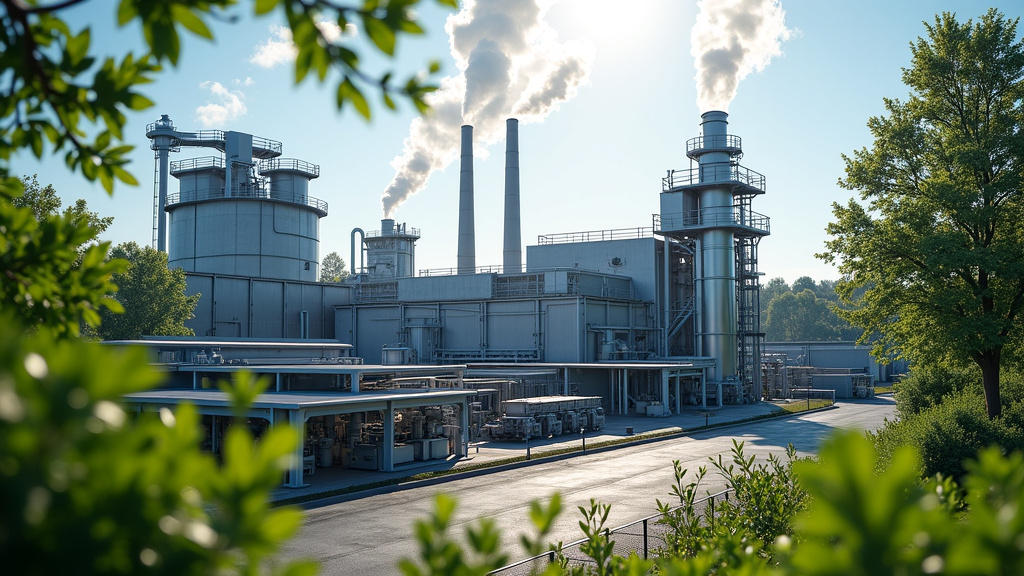
Metal processing plants are adopting sustainable practices to reduce their environmental impact while enhancing efficiency and cutting costs. These approaches focus on two main areas: zero waste initiatives and eco-friendly technologies.
Zero waste initiatives aim to minimize or eliminate waste production throughout the metal processing lifecycle. This approach involves examining each production stage to find opportunities for material recovery and reuse. Industry efforts include recycling scrap metal, which reduces the need for raw materials and cuts greenhouse gas emissions.
Eco-friendly technologies are transforming metal processing operations. These solutions focus on improving energy efficiency, reducing water consumption, and minimizing harmful emissions. For instance, advanced gas cleaning systems can capture and filter pollutants, ensuring cleaner air while recovering valuable resources.
Environmental Benefits
Adopting sustainable practices in metal processing plants offers significant environmental benefits. By implementing zero waste strategies, companies dramatically reduce landfill waste, preserving valuable land resources. This also lessens the demand for virgin raw materials, conserving natural resources and biodiversity.
Moreover, eco-friendly technologies are crucial in reducing the carbon footprint of metal processing operations. Energy-efficient equipment and processes lower greenhouse gas emissions, supporting global efforts to combat climate change. Additionally, water conservation techniques help preserve this vital resource, especially in water-stressed areas.
Sustainable practices also improve air and water quality in surrounding communities. By reducing emissions and managing wastewater effectively, metal processing plants can become better neighbors and corporate citizens.
Cost Savings and Efficiency
While the environmental benefits of sustainable practices are evident, many metal processing companies find these initiatives also lead to substantial cost savings and improved efficiency. Energy-efficient solutions throughout the process chain result in lower energy consumption and reduced utility costs.
Recycling and reusing materials within production not only minimizes waste but also cuts raw material procurement expenses. This closed-loop approach can lead to significant savings, especially as virgin material prices rise due to increased demand and supply constraints.
Furthermore, adopting eco-friendly technologies often leads to process optimizations that enhance productivity. For example, advanced sorting systems using AI can improve the accuracy and speed of material identification, leading to higher-quality recycled metals and more efficient operations.
Sustainable practices can also open new revenue streams. By-products once considered waste can become valuable commodities, creating additional income sources for metal processing plants. This not only improves the bottom line but also contributes to the circular economy.
Challenges and Future Outlook
While the benefits of sustainable practices in metal processing are clear, implementing these changes can present challenges. Initial investments in eco-friendly technologies and process redesigns can be substantial, requiring careful financial planning and sometimes creative funding solutions.
However, as technologies advance and become more accessible, barriers to adoption are decreasing. Collaborative efforts between industry players, research institutions, and policymakers are driving innovation and making sustainable practices more feasible for companies of all sizes.
Looking ahead, the future of metal processing is green. As environmental regulations tighten and consumer demand for sustainably produced materials grows, companies embracing sustainable practices will be better positioned to thrive in the evolving market landscape.
Sustainable practices in metal processing plants offer a win-win solution, delivering both environmental benefits and economic advantages. By investing in zero waste initiatives and eco-friendly technologies, companies can reduce their ecological impact, save on costs, and improve efficiency. As the industry evolves, these practices will likely become standard, paving the way for a more sustainable and prosperous future in metal processing.
Technology | Environmental Impact | Cost | Examples |
Traditional Steel Production | High CO2 emissions, significant environmental impact | Variable, depends on scale and efficiency | Conventional casting, extrusion, rolling |
Green Steel Production | Lower CO2 emissions, more sustainable | Potentially higher due to new technologies | Closed-loop recycling, renewable energy usage |
Metal Additive Manufacturing | Higher CO2 footprint per kg compared to traditional methods | Higher unit costs | 3D printing |
Eco-Friendly Metal Fabrication | Lower emissions, reduced waste | Can lead to cost savings over time | Laser cutting, renewable energy, low-VOC coatings |
Conclusion: The Importance of Specialty Metal Processing
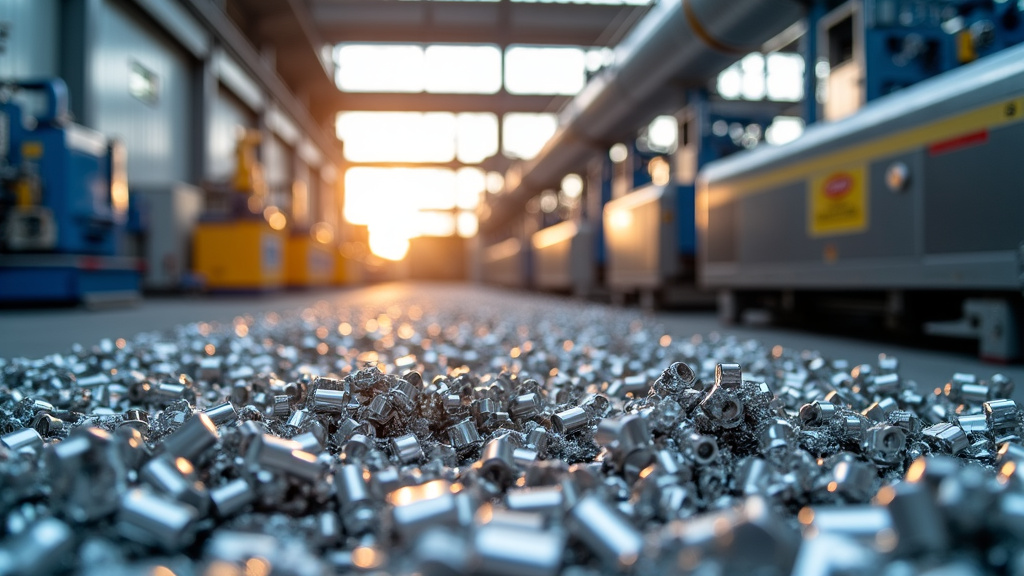
Specialty metal processing is essential across industries, ensuring high-quality manufacturing and supporting sustainability efforts. Companies like Okon Recycling are leading the charge by implementing innovative recycling and waste management solutions, reducing environmental impact, and promoting a circular economy.
The industry’s future is shaped by advancements in energy-efficient processing, water conservation, and advanced recycling technologies. These innovations enhance sustainability, drive economic growth, and improve competitiveness in an evolving global market.
To reduce waste, lower costs, and enhance sustainability in metal processing, partner with Okon Recycling. Contact us at 214-717-4083 to explore customized recycling solutions that support your business and the environment.