5901 Botham Jean Blvd, Dallas, TX 75215
Specialty Metal Recycling Workshops: Key Concepts
February 19, 2025With sustainability taking center stage, specialty metal recycling workshops are playing a crucial role in resource conservation. Today, 30% of the world’s precious metals come from recycling, proving how essential these efforts are in reducing waste and maximizing valuable materials. Okon Recycling is at the forefront of this movement, ensuring metals are recovered efficiently and sustainably.
Specialty metal recycling goes beyond scrapping old materials—it includes reclaiming tungsten carbide from tools and extracting gold, silver, and platinum from outdated electronics. These workshops drive urban mining, transforming discarded items into valuable resources while reducing the demand for environmentally harmful mining.
The benefits extend beyond sustainability. Recycling metals saves raw materials, reduces energy use, and cuts carbon emissions—for example, recycling a ton of steel conserves 1.5 tons of iron ore and 40% of the water needed for primary production. Okon Recycling and other industry leaders are making these efficiencies possible, helping businesses adopt greener practices while stabilizing material markets and lowering costs.
Join us as we explore the cutting-edge techniques behind specialty metal recycling, the challenges the industry faces, and how Okon Recycling is shaping a more sustainable, resource-efficient future.
Exploring the Techniques in Specialty Metal Recycling
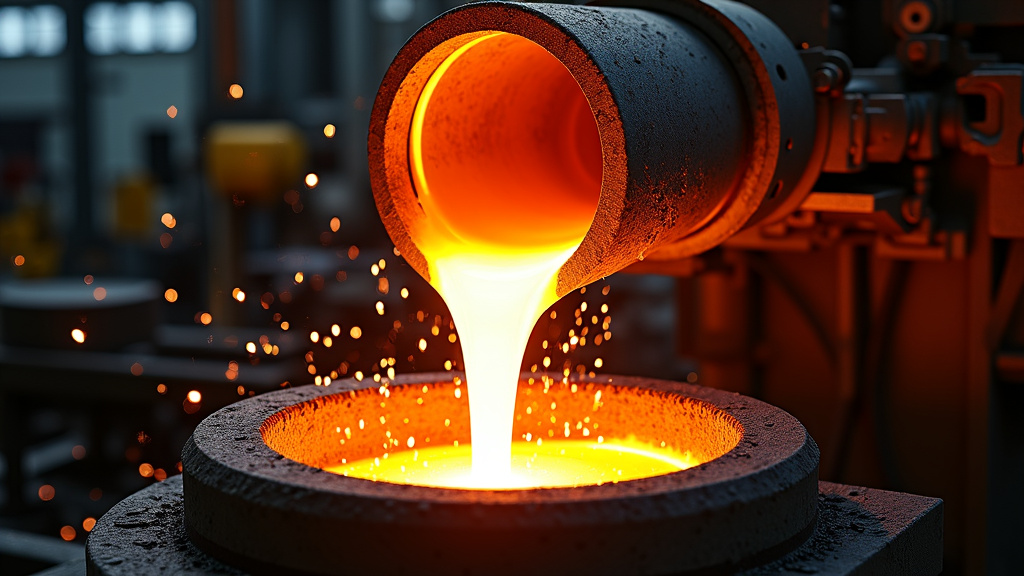
The specialty metal recycling industry is rapidly advancing, with new techniques enhancing the recovery of valuable materials. Here, we explore some innovative processes transforming the extraction of precious metals like platinum and rhodium from scrap materials.
Melting: The Foundation of Metal Recycling
Melting is central to specialty metal recycling. This technique involves heating metal scraps to their melting point in specialized furnaces. For platinum, this occurs at 1,768°C (3,214°F), while rhodium melts at 1,964°C (3,567°F).
Modern melting techniques use electric arc furnaces, which employ high-voltage electricity to reach temperatures over 3,500°C. These furnaces are efficient and more environmentally friendly than traditional methods. Franklin Metals notes that controlling the furnace atmosphere is crucial to prevent oxidation and manage the chemical composition of the molten metal.
The melting process enables recyclers to separate metals based on their melting points, which is useful when handling complex scrap materials containing multiple metals.
Metal | Melting Point (°C) | Melting Point (°F) |
---|---|---|
Platinum | 1768 | 3214 |
Rhodium | 1964 | 3567 |
Milling: Breaking Down Materials for Better Recovery
Before melting, many recycling operations use milling techniques to reduce larger scrap pieces into smaller particles, improving process efficiency.
Advanced milling technologies employ machinery to crush, grind, and pulverize metal scraps. These methods not only reduce material size but also separate components, facilitating the isolation of valuable metals like platinum and rhodium.
An innovative milling approach is cryogenic grinding, which cools scrap materials to low temperatures, making them brittle and easier to break down. It’s particularly effective for tough or flexible materials at room temperature.
Refining: Purifying Precious Metals
After melting and separation, refining begins. This step is where the true value of metals like platinum and rhodium is realized. Refining techniques have become more sophisticated, achieving higher purity levels and better recovery rates.
Electrorefining is one advanced method. An electric current passes through a solution containing the impure metal, depositing pure metal onto an electrode and leaving impurities behind. This technique is effective for producing ultra-pure platinum and rhodium.
Another approach is solvent extraction, a chemical process for selectively separating metals from a solution. It’s useful for complex mixtures of precious metals, isolating specific elements with high precision.
Sustainability in Specialty Metal Recycling
Advancements in melting, milling, and refining aren’t just about efficiency—they’re also enhancing industry sustainability. By recovering valuable metals from scrap, these processes reduce the need for new mining activities, which can have significant environmental impacts.
Many recycling facilities now implement closed-loop systems to minimize waste and energy consumption. For example, heat generated during melting can be captured and reused, improving energy efficiency.
Recycling specialty metals like platinum and rhodium is crucial for sustainability. These metals are key in catalytic converters, which reduce vehicle emissions. Efficient recycling ensures a steady supply for this vital technology.
As technology advances, more innovative techniques will likely emerge in specialty metal recycling, improving recovery rates and contributing to a more sustainable economy for these valuable resources.
The Economic Impact of Specialty Metal Recycling Workshops

With growing environmental awareness and resource scarcity, specialty metal recycling workshops have become significant economic contributors. These facilities not only support sustainability but also generate substantial profits, transforming industrial waste management.
The economic impact of metal recycling is both significant and diverse. By reclaiming valuable metals from industrial byproducts and end-of-life products, companies can significantly reduce raw material and capital costs. According to a study published in ScienceDirect, recycled metals can be 2-10 times more cost-effective than mining virgin materials.
The advantages extend beyond cost savings. Innovative recycling operations are discovering new revenue streams from what was once considered worthless waste. For example, printed circuit boards from electronics can contain 100-150 grams of gold per ton, a concentration higher than most gold ore deposits. By expertly extracting these precious metals, recyclers are tapping into a lucrative “urban mining” industry.
Case Studies in Successful Metal Recycling
Several companies have demonstrated the immense profit potential in specialty metal recycling. Umicore, a materials technology company, has become a recycling powerhouse. Their integrated metals smelter and refinery in Belgium processes complex waste streams to recover precious and specialty metals, generating over €700 million in annual revenue from recycling activities alone.
Consider Electronic Recyclers International (ERI), which has built a successful business around recycling e-waste. By developing technologies to efficiently extract valuable metals from discarded electronics, ERI has grown into a $120 million company with eight locations across the United States. Their success highlights the economic opportunities created by the rapidly growing e-waste recycling market.
Driving Industry-Wide Cost Reductions
Beyond creating new business opportunities, metal recycling workshops help reduce costs across industries. The automotive sector is a prime example. By incorporating recycled metals into their supply chains, car manufacturers can significantly lower production expenses. A Boston Consulting Group report found that using recycled steel can reduce production costs by up to 20% compared to virgin materials.
The aerospace industry also benefits economically from metal recycling. With the high cost of specialty alloys used in aircraft manufacturing, recycling programs can lead to significant savings. Boeing, for instance, reported reclaiming over 130 million pounds of aerospace-grade aluminum alloy scrap in a single year, offsetting their raw material costs.
Challenges and Future Outlook
While the economic potential of specialty metal recycling is clear, challenges remain. Fluctuating metal prices can impact profitability, and developing efficient recycling processes for complex materials requires ongoing innovation. However, as technologies advance and awareness of economic benefits grows, the metal recycling industry is poised for continued expansion.
The future looks promising for specialty metal recycling workshops. As industries increasingly prioritize sustainability and seek to reduce costs, these facilities will play a crucial role in the global economy. By transforming waste into valuable resources, they not only support the environment but also forge a path to profitability in the circular economy.
Overcoming Challenges in the Specialty Metal Recycling Industry
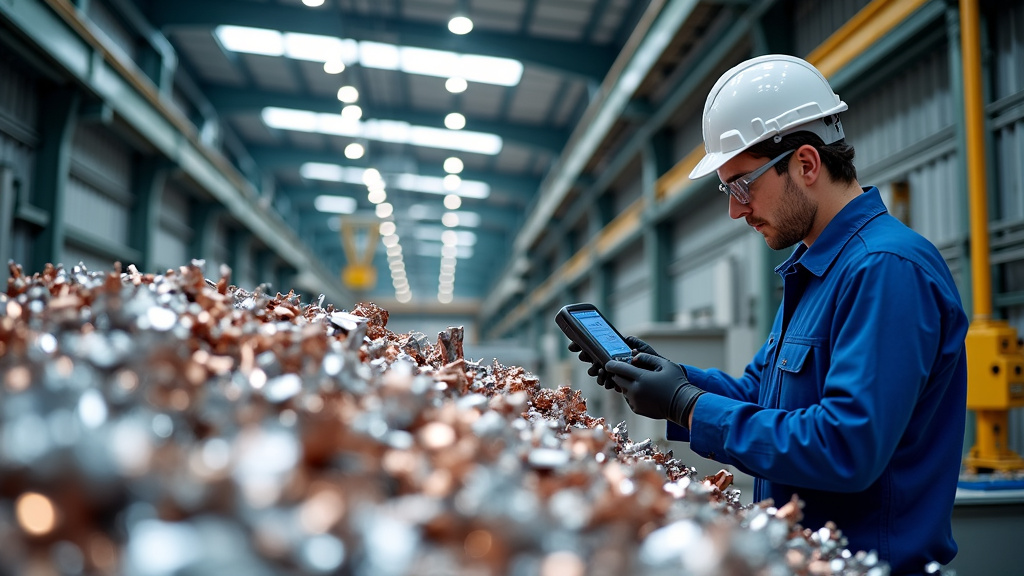
The specialty metal recycling industry faces unique hurdles requiring innovative solutions. Key challenges include sorting diverse metal types and accurately identifying their compositions, which can significantly impact the efficiency and profitability of recycling operations if left unaddressed.
A primary obstacle is the variety of metals and alloys entering recycling streams. From common materials like steel and aluminum to exotic alloys used in aerospace, each type requires specific handling and processing. Traditional reliance on manual sorting methods risks material loss and increases labor strain and operational costs.
To tackle these challenges, the industry is adopting cutting-edge technologies. Alloy analyzers have become essential tools, using advanced techniques like X-ray fluorescence (XRF) to identify metal compositions accurately. These tools provide instant analysis, enabling quick, informed decisions and dramatically improving efficiency.
Enhancing Sorting Precision with Advanced Technologies
Implementing sophisticated sorting technologies marks a significant leap forward. Sensor-based systems, using X-ray transmission (XRT) and near-infrared (NIR) sensors, detect and separate metals based on their unique properties. This precision ensures even closely related alloys are properly categorized.
Artificial intelligence (AI) and machine learning algorithms further enhance these systems. They learn from vast datasets, improving their ability to sort metals as new compositions enter the recycling stream, resulting in an adaptable and efficient process.
Technology | Description |
---|---|
X-Ray Fluorescence (XRF) | Sorts metals by detecting their spectral signatures, achieving high purity levels. |
X-Ray Transmission (XRT) | Combines with XRF for enhanced sorting by analyzing material density and composition. |
AI-Powered Optical Sorting | Uses high-resolution cameras and algorithms to differentiate materials based on visual characteristics. |
Near-Infrared (NIR) Technology | Detects and sorts materials by their spectral signatures, effective for plastics. |
Robotics and Automated Sorting | Employs AI and precision gripping for high-speed, accurate material handling and sorting. |
Enhanced sampling techniques complement these high-tech solutions. By developing representative sampling methods, recyclers ensure accurate composition analysis of large metal batches, crucial for high-value specialty metals where inaccuracies can have financial impacts.
Addressing Contamination and Purity Concerns
Contamination is a persistent challenge, especially for specialty alloys where purity is vital. Advanced cleaning and preprocessing methods, like thermal decoating and chemical treatments, remove surface contaminants without compromising metal integrity.
Innovative metallurgical processes are emerging to handle complex, multi-material components in modern products. These processes separate and recover metals from intricate assemblies, opening new recycling opportunities.
The Future of Specialty Metal Recycling
As the industry evolves, integrating these technologies promises to transform specialty metal recycling. Combining advanced sorting, precise analysis, and innovative processing techniques leads to higher recovery rates, improved purity, and greater efficiency.
Adopting these solutions addresses current challenges and positions the industry to handle future complexities. As product designs become more sophisticated and new alloys are developed, the recycling industry’s ability to adapt and innovate will be crucial for maintaining a circular economy for specialty metals.
While challenges in the specialty metal recycling industry are significant, technological advancements offer promising solutions. By embracing these innovations, recyclers can overcome sorting complexities, improve composition analysis, and contribute to a more sustainable, resource-efficient future.
Innovative Future: Specialty Metal Recycling Workshops in a Circular Economy
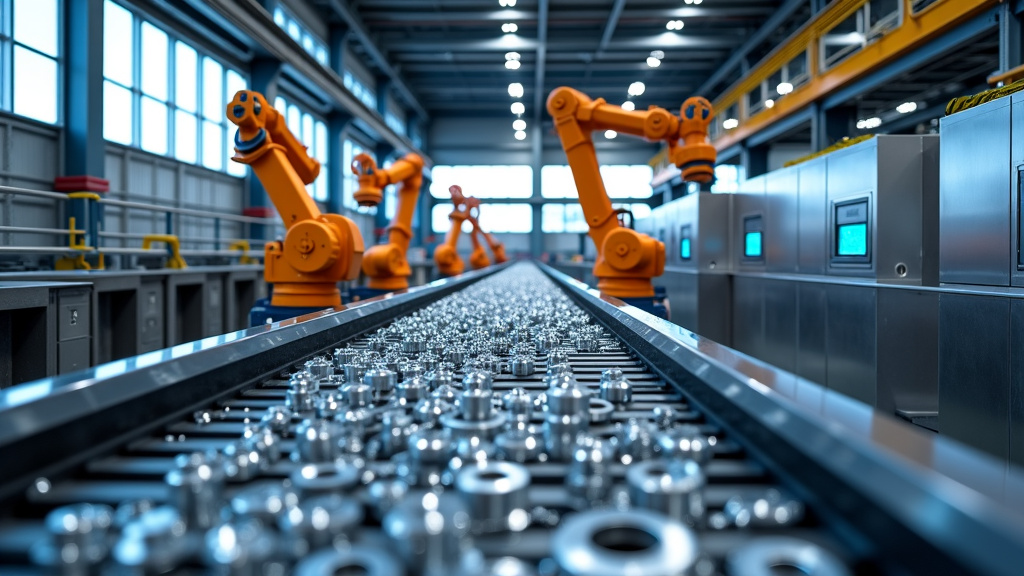
Looking to the future of metal recycling and reuse, specialty workshops are set to play a crucial role in driving sustainable growth and advancing the circular economy. By harnessing cutting-edge technologies and progressive policies, these innovative facilities are transforming metal recovery and recycling.
Artificial intelligence is revolutionizing scrap metal sorting and processing. Advanced AI systems can now identify and categorize various metals with remarkable speed and accuracy, far surpassing traditional methods. This technology enables recyclers to efficiently separate mixed metal streams, maximizing the recovery of valuable materials that may have previously been lost or contaminated.
Policy advancements are equally vital in shaping the future landscape of metal recycling. Forward-thinking regulations are creating incentives for businesses to prioritize recycling and reuse over virgin material extraction. For example, extended producer responsibility policies encourage manufacturers to design products with recycling in mind, facilitating easier disassembly and material recovery at end-of-life.
The convergence of AI-driven sorting and supportive policies is fostering a new era of sustainable growth in the recycling industry. By optimizing metal reuse, these workshops are conserving valuable resources and reducing the environmental impact associated with primary metal production. This shift towards a more circular approach is creating new economic opportunities while addressing pressing environmental challenges.
Final Words
The future of specialty metal recycling is full of potential, with innovative workshops driving sustainability and efficiency. These advancements are not just transforming an industry—they are reshaping how we value and reuse resources.
To accelerate progress, investment in research, technology, and collaboration will be essential. Businesses that embrace these innovations can reduce waste, lower costs, and contribute to a circular economy.
Ready to be part of the change? Contact Okon Recycling at 214-717-4083 to explore cutting-edge recycling solutions that support both environmental responsibility and business growth. The future is sustainable—let’s build it together.