5901 Botham Jean Blvd, Dallas, TX 75215
How to Recycle Industrial Steel: A Complete Guide
February 12, 2025Recycling just one ton of steel conserves 2,500 pounds of iron ore, 1,400 pounds of coal, and 120 pounds of limestone—a testament to the massive environmental impact of industrial steel recycling. As industries strive for greater sustainability, understanding how to recycle steel efficiently is more critical than ever.
Steel is the backbone of industries like construction, automotive, and manufacturing, and its 100% recyclability makes it one of the most sustainable materials available. Unlike other materials, steel can be recycled indefinitely without losing strength or quality, offering a powerful solution to global resource conservation challenges.
At Okon Recycling, we specialize in industrial steel recycling, helping businesses reduce waste, cut energy consumption, and minimize their environmental footprint. Using recycled steel requires 60% to 74% less energy than producing new steel, significantly reducing carbon emissions while keeping valuable materials in circulation.
This article explores the innovative technologies and processes revolutionizing industrial steel recycling.
Essential Techniques for Recycling Industrial Steel
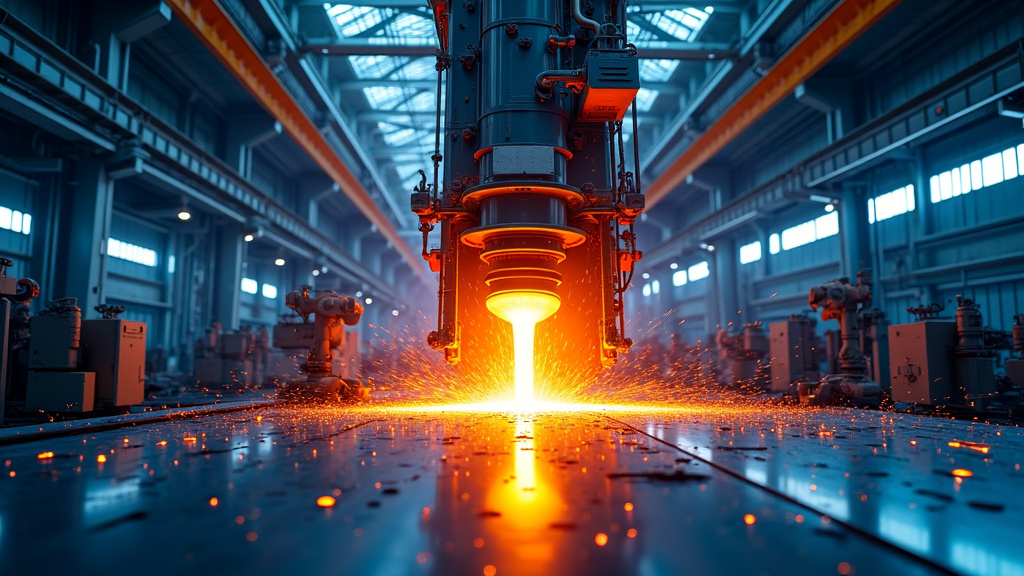
Recycling industrial steel has evolved into a sophisticated process, leveraging advanced technologies to maximize efficiency and minimize environmental impact. As the backbone of numerous industries, steel’s recyclability plays a crucial role in sustainable manufacturing and construction practices.
Let’s explore the key techniques that make modern steel recycling a marvel of industrial ingenuity.
Collection and Sorting: The Foundation of Effective Recycling
The journey of recycled steel begins with meticulous collection and sorting. Gone are the days of manual separation; today’s recycling facilities employ advanced technologies to ensure precision and speed. Magnetic separation and optical sorting systems have transformed this initial stage, distinguishing ferrous from non-ferrous metals with remarkable accuracy.
These sorting technologies use a combination of magnets, sensors, and artificial intelligence to identify and categorize different types of steel scrap. The result is a cleaner, more homogeneous feedstock for the subsequent stages of recycling, which is essential for producing high-quality recycled steel.
Some facilities have begun experimenting with robotic sorting arms guided by machine learning algorithms. These systems can ‘learn’ to recognize different grades of steel based on visual and physical properties, further refining the sorting process.
Shredding: Breaking Down Barriers to Recyclability
Once sorted, industrial steel scrap undergoes a transformative shredding process. Modern shredders are marvels of engineering, capable of reducing large pieces of steel—from defunct machinery to automotive parts—into manageable fragments in mere seconds.
The efficiency of these shredders isn’t just about brute force; it’s about precision and energy conservation. Many facilities now use hydraulic shredders that adjust their power output based on the material being processed, optimizing energy consumption and reducing wear on the equipment.
An innovative development in this field is the introduction of ‘smart shredders’ equipped with sensors that monitor the composition of the scrap in real-time. These systems can adjust their operations on the fly, ensuring optimal shredding for different types of steel alloys.
Melting: Where Science Meets Sustainability
The melting phase is where significant advancements in steel recycling have occurred. Electric Arc Furnaces (EAFs) have become the gold standard for melting recycled steel, offering unparalleled energy efficiency compared to traditional blast furnaces.
These furnaces use high-current electric arcs to melt steel scrap, consuming significantly less energy than methods that rely on coal or natural gas. The precision control afforded by EAFs allows for exact temperature management, crucial for maintaining the quality of the recycled steel.
Moreover, some cutting-edge facilities are integrating renewable energy sources to power their EAFs, further reducing the carbon footprint of the recycling process. Imagine a future where solar-powered furnaces transform yesterday’s scrap into tomorrow’s skyscrapers—it’s closer than you might think.
Refining and Purification: Crafting Quality from Chaos
The final stages of industrial steel recycling involve refining and purifying the molten metal to meet stringent quality standards. Advanced spectrometry techniques allow for real-time analysis of the steel’s composition, enabling precise adjustments to achieve the desired properties.
Innovative purification methods, such as vacuum degassing and ladle metallurgy, remove impurities and fine-tune the steel’s chemical makeup. These processes ensure that recycled steel can match or even exceed the quality of steel produced from virgin materials.
The byproducts of this refining process, such as slag, are increasingly being repurposed for use in construction materials, exemplifying the circular economy principles at the heart of modern recycling efforts.
Energy Efficiency: The Invisible Innovation
Throughout each stage of the recycling process, energy efficiency remains a top priority. From variable frequency drives in shredders to heat recovery systems in melting furnaces, every aspect of industrial steel recycling is optimized to reduce energy consumption.
Some facilities have implemented sophisticated energy management systems that use predictive analytics to optimize power usage across the entire recycling operation. These systems can shift energy-intensive processes to off-peak hours or when renewable energy is most abundant, further reducing the environmental impact of recycling.
As we continue to push the boundaries of what’s possible in steel recycling, one thing is clear: the future of industrial steel is not just strong and durable, but increasingly sustainable and energy-efficient. Through these essential techniques and ongoing innovations, the steel industry is forging a path toward a greener, more circular economy.
Technology | Efficiency Gain | Impact |
---|---|---|
Magnetic Separation | Improved purity of recycled steel | Enhanced sorting speed and accuracy |
Electric Arc Furnace (EAF) | Reduced energy consumption by 60-74% | Less reliance on coal, lower carbon emissions |
Advanced Shredders | Optimized energy use | Increased processing speed and reduced wear |
X-ray Fluorescence (XRF) | Higher precision in sorting | Ensures high-quality recycled steel |
AI-driven Sorting | Enhanced material recognition | Optimized recycling workflow |
Industrial Steel Recycling: Challenges and Solutions
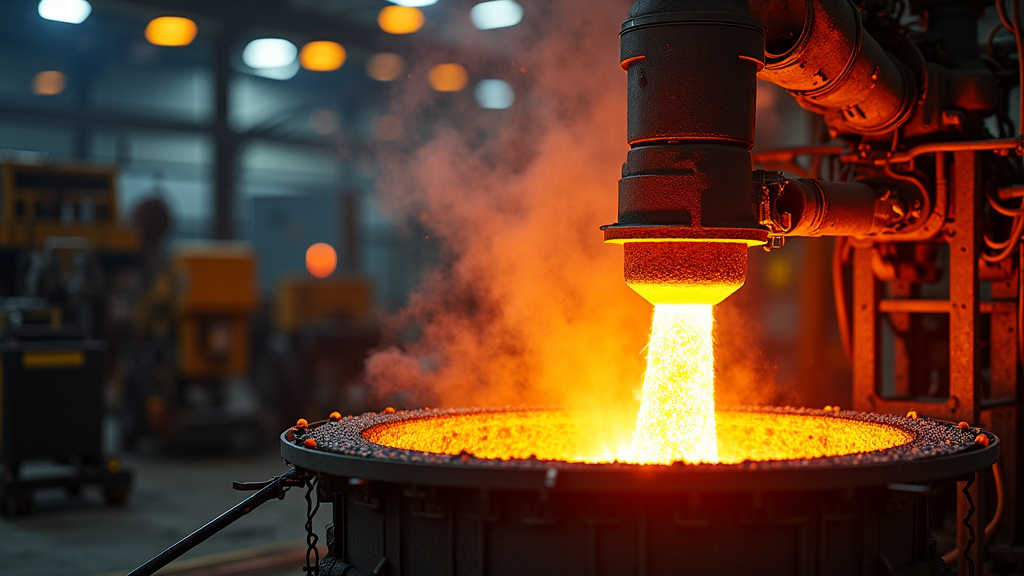
Steel recycling is crucial for sustainable industry practices, yet it faces challenges. Transforming scrap metal into high-quality reusable steel involves navigating technical and logistical hurdles. Let’s explore these issues and the innovative solutions advancing the industry.
The Mixed Scrap Challenge
Managing the varied nature of scrap metal sources is a significant challenge in steel recycling. Recyclers often encounter a mix of materials, each with different compositions and contaminants, which can affect the recycling process and the final product’s integrity.
Advanced sorting technologies like spectrometers and X-ray fluorescence (XRF) analyzers now allow for rapid, precise identification of metal types and alloys. These tools help recyclers separate materials accurately, ensuring each batch meets quality standards.
Moreover, artificial intelligence is enhancing the sorting process. Machine learning algorithms can predict scrap loads’ composition, optimizing workflow and improving efficiency. This technological advancement is crucial for maintaining high standards in industries like aerospace and automotive manufacturing.
The Purity Imperative
Ensuring the purity of recycled steel is essential, especially for high-performance applications. Contaminants like copper, tin, or non-metallic materials can negatively impact steel’s properties. The challenge is to remove these impurities during melting and refining.
Advanced purification techniques like vacuum induction melting (VIM) have become vital. By melting steel in a vacuum, VIM effectively removes volatile impurities and gases, resulting in ultra-pure recycled steel. This process is especially important for producing high-grade alloys used in critical components.
Another solution is slag engineering. By controlling the slag composition in the steelmaking process, recyclers can more effectively remove unwanted elements from molten steel. This technique improves purity and enhances recycling efficiency.
Partnerships: Collaborating for Success
The complexities of steel recycling have led to new industry partnerships. Specialized recycling facilities are collaborating with steel producers, creating a beneficial relationship for both parties and the environment. These collaborations drive innovation and set new standards for recycled steel quality.
Some steel mills are co-locating with recycling facilities, creating integrated ‘mini-mills’ that process scrap and produce finished steel products in one location. This setup reduces transportation costs and emissions while allowing for tighter quality control throughout the recycling process.
Partnerships between recyclers and technology providers are accelerating the development of new recycling technologies. From advanced sensors to robotics, these collaborations push the boundaries of steel recycling, constantly improving material output and quality.
Conclusion: The Growing Impact of Steel Recycling
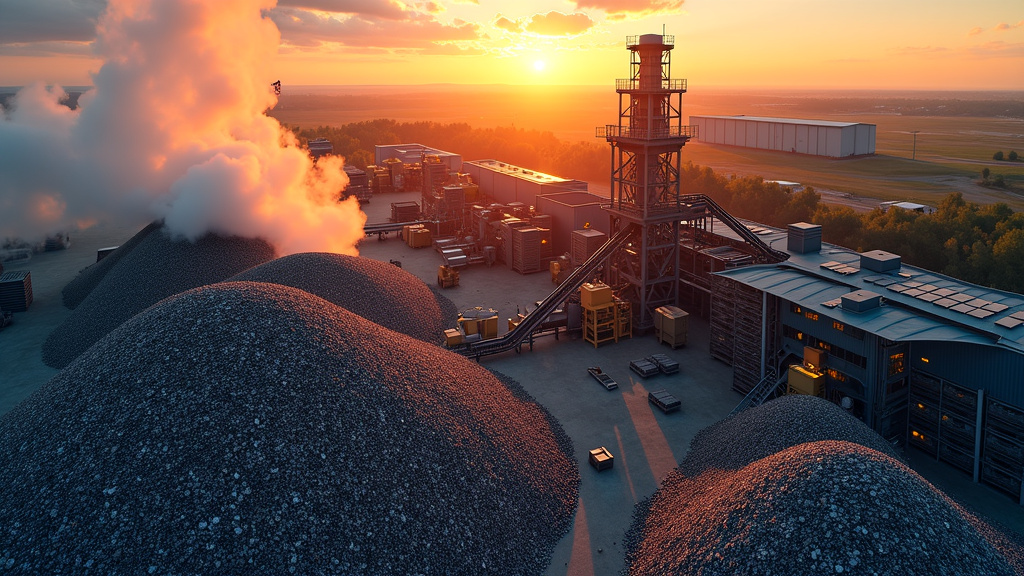
Steel recycling isn’t just an environmental responsibility—it’s a pillar of sustainable industrial development. By recycling steel, industries reduce landfill waste, conserve energy, and cut greenhouse gas emissions, making a tangible impact on both the economy and the environment.
The numbers speak for themselves: every ton of recycled steel saves 1.4 tons of iron ore, 0.8 tons of coal, and 0.3 tons of limestone, while also reducing energy consumption by 60% to 74% compared to virgin steel production. As technology advances, sensor-based sorting innovations like X-ray fluorescence (XRF) and laser-induced breakdown spectroscopy (LIBS) are refining the recycling process, enabling higher-purity, high-performance applications.
At Okon Recycling, we are at the forefront of this transformation. With cutting-edge facilities and a commitment to sustainability, we recover and repurpose industrial steel efficiently, ensuring businesses maximize resource efficiency while reducing environmental impact. From energy-efficient processing to water recycling systems, Okon is setting new standards in eco-friendly steel recycling.
The future of sustainable industry depends on action today. Businesses that embrace efficient steel recycling reduce costs, strengthen supply chains, and contribute to a greener planet. Join us in leading this change. Contact Okon Recycling at 214-736-9509 to explore how your company can benefit from sustainable steel recycling solutions.