5901 Botham Jean Blvd, Dallas, TX 75215
How Industrial Magnets Enhance Material Handling Efficiency
February 6, 2025Safety and efficiency are paramount in the current manufacturing environment. Enter the unsung heroes of material handling—powerful NdFeB (Neodymium Iron Boron) magnets.
These tools are enhancing how industries move and manipulate ferrous materials, offering enhanced safety, improved operational efficiency, and significant cost savings. Now, how do these magnetic tools work their magic?
Imagine replacing those precarious chains and hooks with a sleek, contactless lifting system. NdFeB magnets, engineered with a 3 to 1 safety factor, grip materials with unwavering strength, reducing the risk of dangerous slips and falls. It’s like giving your material handling process a super-powered safety net.
Now, let’s talk dollars and cents.
While the initial investment in magnetic systems might raise eyebrows, the long-term savings are undeniable. Reduced labor costs, minimized equipment wear and tear, and fewer workplace accidents all contribute to a healthier bottom line. It’s an investment that pays off in both safety and profitability.
But what happens when these powerful magnets reach the end of their lifecycle? That’s where Okon Recycling steps in.
Specializing in the recovery and repurposing of industrial magnets, Okon ensures that these essential tools don’t go to waste. By reclaiming NdFeB magnets from decommissioned machinery, Okon Recycling supports sustainability while keeping valuable materials in circulation.
As we explore the world of industrial magnets, we’ll see how these powerful tools are transforming material handling across diverse industries.
Enhancing Safety with Industrial Magnets in Material Handling
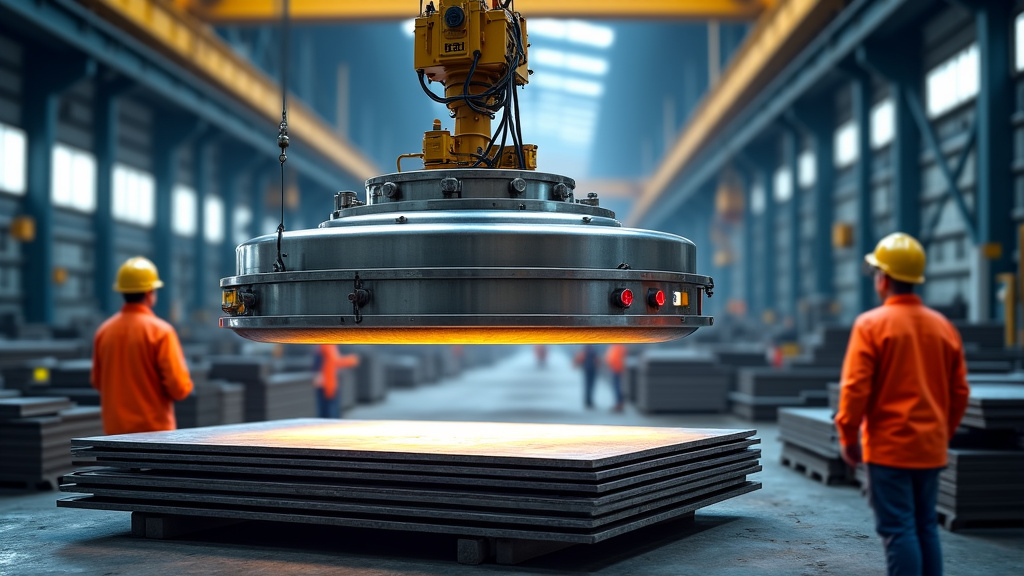
The built-in safety factor of industrial magnets is a game-changing feature that distinguishes them from conventional lifting methods. This factor ensures that the magnet’s lifting capacity exceeds the weight of the load by a significant margin, providing extra protection against unexpected load shifts or environmental factors.
For example, a magnet rated for 1000 pounds might actually lift 1500 pounds, offering a 50% safety margin. This overengineering significantly reduces the likelihood of load drops, even in challenging conditions. Thoughtful design like this has made industrial magnets indispensable in high-risk environments.
This safety factor not only prevents accidents but also instills confidence in operators, allowing them to work more efficiently and with less stress. This psychological benefit can lead to improved productivity and job satisfaction.
The Future of Safety in Material Handling
As technology advances, we can expect even more sophisticated industrial magnets to emerge. Innovations in electromagnet design and smart control systems are paving the way for magnets that can adapt to different loads and conditions in real-time, enhancing their safety capabilities.
The integration of sensors and IoT technology with industrial magnets is another exciting frontier. These smart magnets can provide real-time data on load weight, magnetic field strength, and operational parameters, allowing for predictive maintenance and more precise safety controls.
The advent of industrial magnets with built-in safety factors marks a significant leap forward in workplace safety for material handling operations. By drastically reducing risks associated with load slippage and operational failures, these magnets are not just tools, but guardians of worker safety.
Boosting Operational Efficiency with Material Handling Magnets
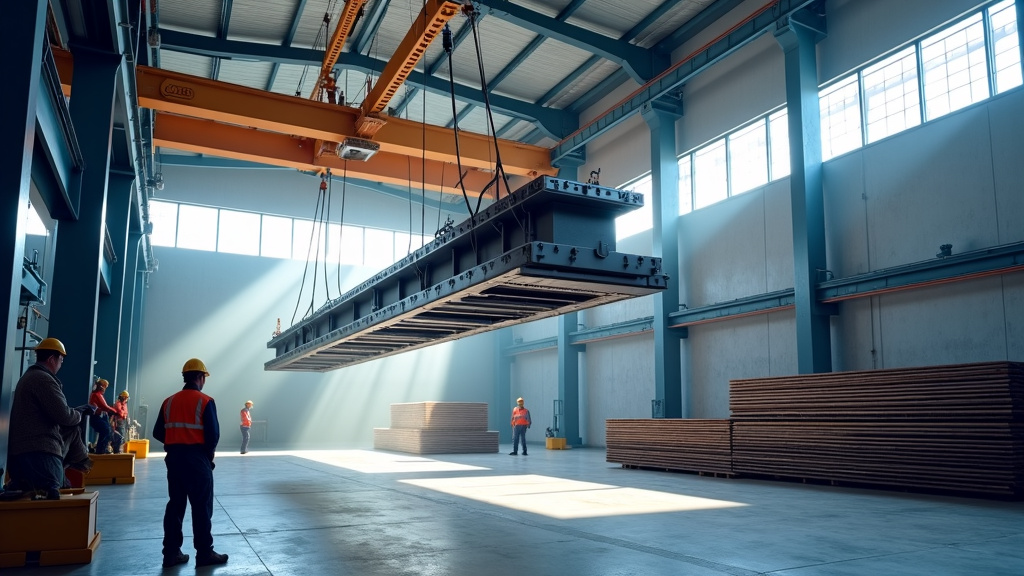
In industrial operations, material handling magnets have transformed how businesses move heavy loads. These powerful tools offer significant efficiency improvements over traditional lifting methods, reducing the time and manpower needed for material movement.
Their appeal lies in their ability to streamline operations. Unlike conventional chains, slings, or mechanical lifts that require extensive setup and manual intervention, material handling magnets enable swift and nearly effortless lifting of ferrous materials. This efficiency translates directly into enhanced productivity across various industries.
The efficiency gains are particularly striking when examining the operational mechanics. Traditional methods typically involve a laborious process of securing loads with chains or slings, a time-consuming task that exposes workers to potential safety risks. In contrast, magnetic lifting systems eliminate these steps entirely, allowing operators to engage and disengage loads with a simple lever operation.
Comparative Advantages: Magnets vs. Traditional Methods
The superiority of material handling magnets is evident when comparing them with traditional lifting techniques. Let’s explore some key areas where magnetic systems excel:
Speed and Efficiency: Magnetic lifters enable rapid load engagement and release, significantly reducing handling times. This speed boost can lead to substantial increases in overall operational throughput, especially in high-volume environments like warehouses or manufacturing plants.
Labor Reduction: By simplifying the lifting process, magnetic systems minimize the need for multiple workers to secure loads. This not only cuts labor costs but also allows staff to be reallocated to other value-adding tasks, further enhancing overall productivity.
Cost-Effectiveness of Adopting Industrial Magnets for Material Handling
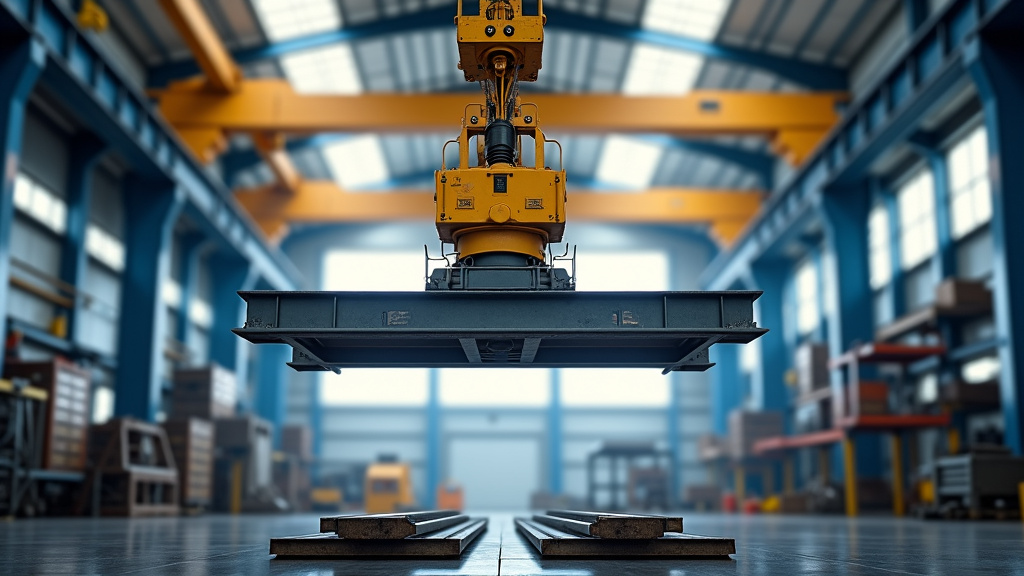
Investing in industrial magnets is a smart financial move. These reliable factory tools boast exceptional durability and require minimal maintenance, leading to significant long-term savings. But there’s more to consider.
Traditional material handling methods often result in costly downtime due to machine breakdowns and worn-out parts. Industrial magnets, however, provide consistent performance, reducing interruptions and maximizing production time.
Breaking Down the Cost Savings
While the initial investment in industrial magnets may seem steep, the payoff is substantial. Industry reports suggest that high-quality industrial magnets can last for decades with proper care. Compared to frequent replacements needed for conventional lifting equipment, the cost savings are evident.
Beyond longevity, these magnets handle heavier loads more efficiently than traditional methods. This increased capacity directly improves productivity, translating into financial gains.
Maintenance Savings: The Hidden Gem
Industrial magnets excel in low maintenance. Unlike complex mechanical systems requiring constant attention, these magnets need little upkeep. No hydraulic fluids to change or intricate parts to repair, making them a major cost-saver.
Sarah Johnson, a plant manager at a leading steel fabricator, shares her experience: “We used to spend thousands each month on maintenance for our old lifting systems. Since switching to industrial magnets, those costs have plummeted. It’s a remarkable difference.”
This reduction in maintenance needs not only saves money directly but also reduces repair downtime, keeping production lines moving and profits flowing. In today’s competitive manufacturing landscape, such reliability is invaluable.
The Long-Term Outlook: A Smart Investment
Adopting industrial magnets goes beyond immediate gains. It’s a strategic move that pays off over the years. As energy costs rise and labor markets tighten, the efficiency of these magnets becomes even more valuable.
Their versatility allows them to adapt to changing production needs. Whether handling sheet metal today or steel beams tomorrow, industrial magnets can keep up with evolving business demands. This flexibility ensures your investment remains relevant and valuable as operations change.
Ultimately, the cost-effectiveness of industrial magnets for material handling is clear. From reduced downtime and maintenance costs to improved efficiency and longevity, these tools offer a strong return on investment. For manufacturers looking to sharpen their competitive edge, industrial magnets are a necessity.
Equipment Type | Cost Considerations | Efficiency Factors |
---|---|---|
Conveyors | High initial investment | Suitable for continuous flow |
Industrial Trucks | Moderate cost, flexible | Best for intermittent use |
Cranes and Hoists | Varies with payload capacity | Useful for large item handling |
Robots | High cost, versatile | Operates in hostile environments |
Versatility and Customization with Material Handling Magnets
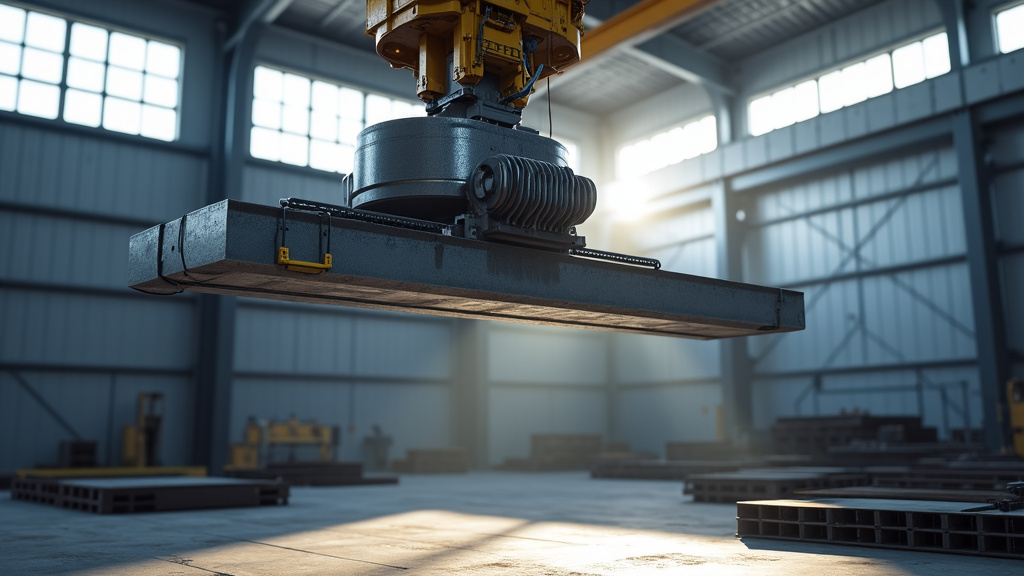
In the industrial world, one size doesn’t fit all, and material handling magnets recognize this. Whether dealing with flat plates, awkward angles, or uniquely shaped materials, there’s a magnet designed for the job.
For example, in the automotive industry, custom magnets lift and position heavy engine components with precision, enhancing assembly line efficiency. It’s like having a craftsman’s hands with the strength of a titan.
In construction, these magnets excel at handling large steel beams and plates, reducing accident risks and speeding up project timelines. Magnets truly excel in these applications.
Adapting to Various Workflows
The adaptability of material handling magnets is remarkable. They integrate seamlessly into existing workflows, often becoming the unsung heroes of operational efficiency, making everything run smoother.
In the recycling industry, these magnets sort and separate ferrous metals from non-metallic materials, streamlining the recycling process. They act as super-powered sorters that never tire or err.
In manufacturing, these magnets are multitaskers, integrating into automated systems to reduce manual labor and minimize workplace injuries. They combine efficiency and safety in one magnetic package.
Customization: The Key to Optimal Performance
While off-the-shelf solutions have their place, customization is where material handling magnets truly shine. Companies increasingly turn to tailored magnetic solutions to address specific operational challenges.
In the aerospace industry, where precision is crucial, specialized magnets handle delicate components with care. They act as personal bodyguards, protecting parts throughout the manufacturing process.
The customization process begins with identifying specific lifting needs and consulting experts for guidance on the best magnet type and specifications. Companies like Dura Magnetics work closely with manufacturers to deliver custom magnet solutions that offer superior performance and quality.
In summary, material handling magnets are game-changers in the industrial landscape. Their versatility and customization open new possibilities for efficiency and safety across various industries. As technology advances, we can expect even more magnetic innovations in material handling.
Magnet Type | Features | Applications |
---|---|---|
Permanent Lifting Magnet | High reliability, no external power needed, easy maintenance | Metal fabrication, machining, steel manufacturing |
Electromagnetic Lifter | Requires external power, adjustable magnetic force, efficient for varied load sizes | Scrapyards, warehouses, recycling facilities |
Electro Permanent Lifting Magnet | Combines reliability of permanent magnets with efficiency of electromagnets, energy-saving | Steel erection, shipbuilding, construction |
Precision and Control in Material Handling with Advanced Magnetic Features
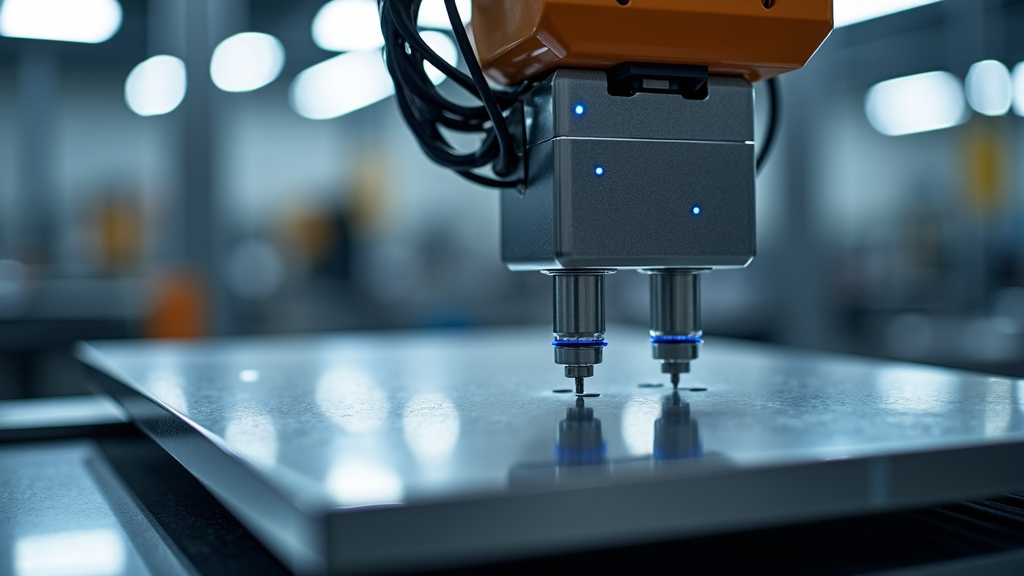
When it comes to powering these magnetic marvels, versatility is key. The industry has embraced a multi-pronged approach, offering solutions that cater to diverse operational needs. Let’s break down the power players:
Battery Power: For operations requiring mobility, battery-powered magnetic systems are invaluable. These portable powerhouses allow for material handling in locations where access to AC power is limited or non-existent. It’s like having a supercharged magnet on wheels, ready to tackle tasks anywhere on the factory floor or construction site.
AC Power: When continuous operation is the priority, AC-powered systems step up to the plate. These setups provide unwavering magnetic strength for as long as needed, making them ideal for high-volume material handling tasks that require sustained performance. Think of it as the marathon runner of the magnetic world—steady, reliable, and always ready for action.
Precision That Pushes Boundaries
The precision afforded by these advanced magnetic features is remarkable. Operators can now control the magnetic field with pinpoint accuracy, allowing for the delicate handling of materials that would have been challenging with traditional methods. This precision isn’t just about avoiding damage—it’s about optimizing every aspect of the material handling process.
Consider the implications for industries like automotive manufacturing or aerospace. The ability to manipulate components with micrometer-level accuracy can mean the difference between a flawless product and a costly mistake. It’s this level of control that’s pushing the boundaries of what’s possible in modern manufacturing and construction.
Conclusion: The Strategic Advantage of Industrial Magnets in Material Handling
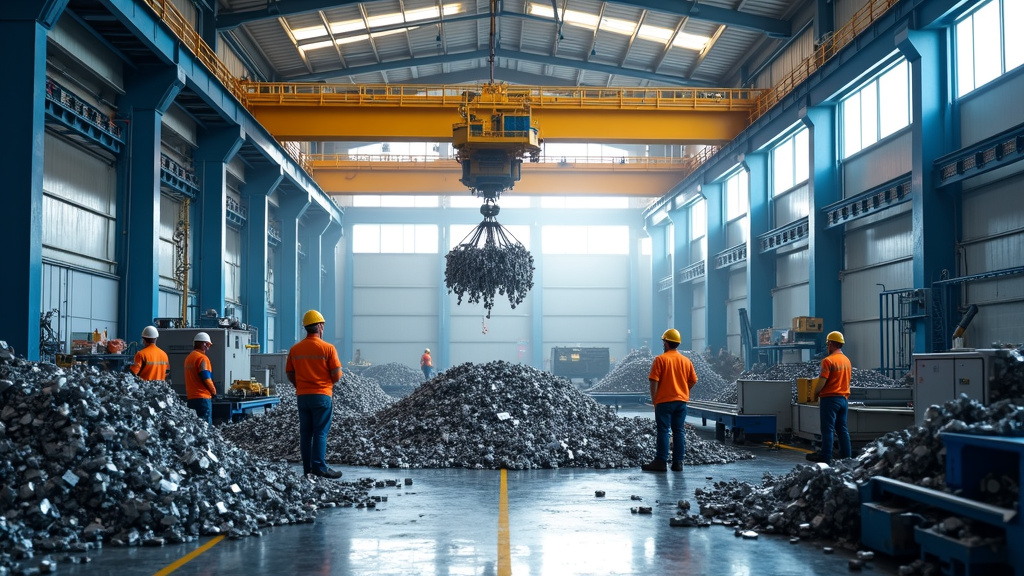
The benefits of integrating these powerful magnetic solutions extend beyond immediate operational gains. By streamlining processes and reducing physical strain on workers, industrial magnets create a safer, more productive work environment. This not only improves morale but also leads to long-term cost savings through fewer workplace injuries and better retention rates.
Importantly, adopting industrial magnets aligns with the growing need for sustainable practices in industry. As businesses face increasing pressure to minimize their environmental impact, these innovative tools offer a way to achieve greener operations without compromising productivity.
However, sustainability doesn’t stop at implementation—it extends to what happens when these magnets reach the end of their lifecycle. That’s where Okon Recycling plays a crucial role.
By recovering and repurposing NdFeB magnets from decommissioned machinery, Okon ensures that valuable materials are kept in circulation rather than discarded. This commitment to recycling reduces waste, supports resource efficiency, and helps industries maintain a more circular approach to material handling.
The future of material handling is magnetic, and the time to act is now. Whether you’re looking to optimize efficiency, enhance workplace safety, or embrace sustainable practices, Okon Recycling provides the expertise and solutions needed to make it happen.
Contact Okon Recycling today at 214-426-6566 to discover how industrial magnets—and responsible recycling—can drive your business toward a more prosperous and sustainable future.